Conair: Going All In on AI
A dozen new products debut at NPE, but the company says new AI-based conveying technology is the true game changer.
With 12 new products about to be unveiled at its booth, there was plenty for Conair to talk about during its press conference the Sunday before NPE2024. But the auxiliary equipment innovator was most excited to tout its first-of-its-kind conveying system that utilizes artificial intelligence (AI) to manage changing conveying conditions.
“When Conair went to NPE2018, all the buzz was about Industry 4.0,” says Sam Rajkovich, vice president of sales and marketing. “We’re still installing Industry 4.0 solutions for customers, and we’re still refining that product. It’s still a very relevant technology, but there’s this new topic that is entered the manufacturing space, which is artificial intelligence. Since the pandemic, we’ve spent a lot of time developing products that make use of things like sensor technology and advanced controls, so that controls essentially take over the operation of the equipment and make informed decisions about how the equipment is going to operate without operator input. That way, the equipment is always maximizing its performance to the betterment of the plant operation.”

Conair calls its solution “Conveying with Optimizer.” It’s a patented AI-driven feature for material handling systems using the Conair SmartFLX conveying control. Now, a SmartFLX conveying control equipped with the Optimizer package automatically detects source-to-destination conditions (vacuum, receiver distance, material bulk density and other factors) then autonomously adjusts the conveying system in real time to move material under optimal conditions. This breakthrough AI-driven conveying system feature is fully operational in a live demonstration at the Conair booth.
Rajkovich continues, “We introduced Wave Conveying technology in 2016, but Conveying with Optimizer is a new spin on how customers could convey. It adds sensor technology and advanced controls technology to the conveying algorithm that we’ve developed, and essentially what it can do is it can use the sensor technology and control technology to do things that previously were unheard of. Let’s say that over time you develop a leak in your conveying line. This control technology will recognize the leak and self-adjust and give you the same rate and conveying output that you received with a leak in your conveying line that you received prior to having a leak in your conveying line. It'll still give you an alert, but it essentially will handle the leak as if it didn’t exist and allow you to continue to make the same rate.”
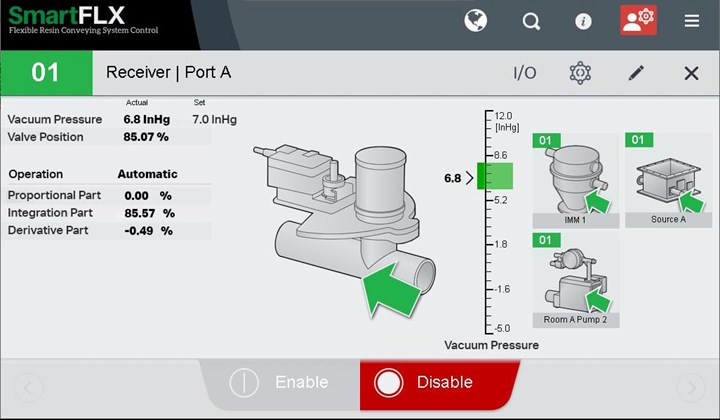
The autonomous capabilities of the Conveying with Optimizer feature were designed to overcome the trickiest, most labor-intensive part of conveying operations: the need to manually adjust air and material ratios (using manual air valves) from source to destination. In practical terms, that means operators must constantly change settings on distribution boxes, pickup boxes or gaylord wands to move material amid constantly changing system conditions.
When systems are properly tuned and when operators guesstimate right, material usually moves predictably. But an incorrect manual adjustment or any number of other changes — conveying distance, material bulk density/regrind ratio, relocated equipment or even a minor vacuum leak caused by a hose or coupling — can spell conveying problems that result in downtime: empty receivers, clogged lines, overloaded pumps, resin losses or excessive system wear.
The AI built into Conveying with Optimizer replaces error-prone human decisions, instead making autonomous system adjustments that move material while compensating for typical conveying system faults. The Optimizer package combines novel software, hardware, sensors and intelligence with the high-speed computing power of the SmartFLX control. Together, these elements sense, calculate and compensate for changing conditions far faster than a human could, while ensuring optimal air/material ratios and trouble-free conveying. And, the machine learning capability of the Optimizer feature enables it to continually refine and perfect each conveying cycle over time.
So, it’s no longer necessary for a processor to pay an operator to walk to the material distribution box, make a feed tube adjustment and then walk to the conveying control to issue a command. Now, the operator simply enters the command — locally on the SmartFLX control or remotely via Conair SmartServices on a connected device — and leaves the Conveying with Optimizer intelligence to figure it out and complete the conveying cycle.
The only prerequisite for Conveying with Optimizer is a conveying system equipped with a SmartFLX control. The Optimizer package may be ordered with a SmartFLX control from the factory or installed to an existing SmartFLX control in the field. Optimizer hardware, which is available in line sizes from 1.5 to 4 inches OD, is installed at material pickup points, while Optimizer software upgrade is loaded into the SmartFLX control
Related Content
Wisconsin Firms Unite in Battle Against Covid
Teel Plastics opened new plant in record time, partnering with AEC & Aqua Poly Equipment Co. to expand production of swab sticks to fight pandemic.
Read MoreMini Vent Provides Dust Separation in Bin or Feeding Applications
Separates dust from displaced air when a vessel is filled with bulk solids.
Read MoreFinding Efficiencies in How Components Work Together
Auxiliary systems are vital to the proper functioning of a plastic processing line, and they can be a source of major cost and efficiency improvements.
Read MoreCut Loading Time Through Direct Charge Blending
Direct charge blender loading, a vacuum-powered automation process, can dramatically improve loading time and reduce material costs. In this article, we address ten common questions to help you determine if the systems are right for your facility.
Read MoreRead Next
People 4.0 – How to Get Buy-In from Your Staff for Industry 4.0 Systems
Implementing a production monitoring system as the foundation of a ‘smart factory’ is about integrating people with new technology as much as it is about integrating machines and computers. Here are tips from a company that has gone through the process.
Read MoreFor PLASTICS' CEO Seaholm, NPE to Shine Light on Sustainability Successes
With advocacy, communication and sustainability as three main pillars, Seaholm leads a trade association to NPE that ‘is more active today than we have ever been.’
Read More