‘Breakthough’ Nucleating Agent for Range of PP Applications
CAI Performance Additives’ new ST-NAP32 nucleator boosts PP performance for improved lithium battery separators, injection-molded products and PP-R pipe.
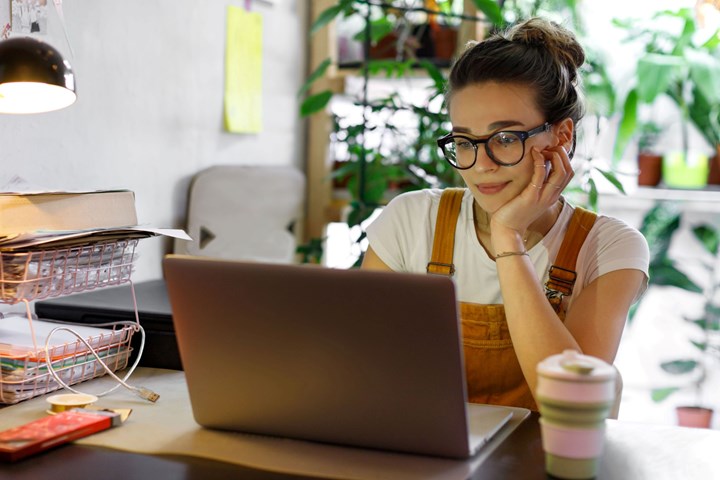
A new formulated β (beta) crystal nucleating agent is said to be a “breakthrough” in improving performance of PP in applications such as lithium battery separators. Newly available from CAI Performance Additives, the sole distributor of high-performance additives produced by China’s Starbetter Chemical Materials, ST-NAP32 falls in the special class beta nucleators, which cause a different crystal structure of PP to form when a molded or extruded part is cooled from the melt.
Certain properties of PP are drastically altered by this change in crystal structure as β crystals are known for their superior properties, including high impact strength, high heat distortion temperature, and good thermal stability.
ST-NAP32 is said to increase impact strength, heat distortion temperature, and porosity of PP products. It has been shown to be very useful for better performing separators for lithium ion batteries, but can also be used to improve the performance of a wide range of other PP products, including PP-R pipe and injection molded PP products. Easy-to-use ST-NAP32 can be added directly to PP resin or as a masterbatch.
Related Content
-
In Sustainable Packaging, the Word is ‘Monomaterial’
In both flexible and rigid packaging, the trend is to replace multimaterial laminates, coextrusions and “composites” with single-material structures, usually based on PE or PP. Nonpackaging applications are following suit.
-
The Fundamentals of Polyethylene – Part 1: The Basics
You would think we’d know all there is to know about a material that was commercialized 80 years ago. Not so for polyethylene. Let’s start by brushing up on the basics.
-
Melt Flow Rate Testing–Part 1
Though often criticized, MFR is a very good gauge of the relative average molecular weight of the polymer. Since molecular weight (MW) is the driving force behind performance in polymers, it turns out to be a very useful number.