Compounding and Injection Molding Combined in Circularity Display
NPE2024: KraussMaffei aims to “make plastic green” with in-booth moldings and recycled plastics converted into other applications through a combination of injection molding, extrusion and inline compounding.
KraussMaffei is promoting sustainability across all its manufacturing platforms, including injection molding with a series of displays emphasizing circularity and carbon footprint reduction. At the show, KraussMaffei is molding single-use medical blood vials and then, through a series of processes, convert them into durable, long-life bottle openers.
An all-electric PX 251-1400 is molding medical blood vials from a 32-cavity mold using ExxonMobil PP 9074 MED material. After shredding, these vials serve as base material for the upcycling process carried out on the ZE 28 BluePower twin-screw extruder. At the extruder, various additives (including bonding agents and liquid pigments) are added, mixed and homogenized. The resulting compound is fed to an all-electric PX 81-180, which will utilize the company’s APCplus dynamic control to account for viscosity fluctuations in the recycled blood-vial resin and mold bottle openers.
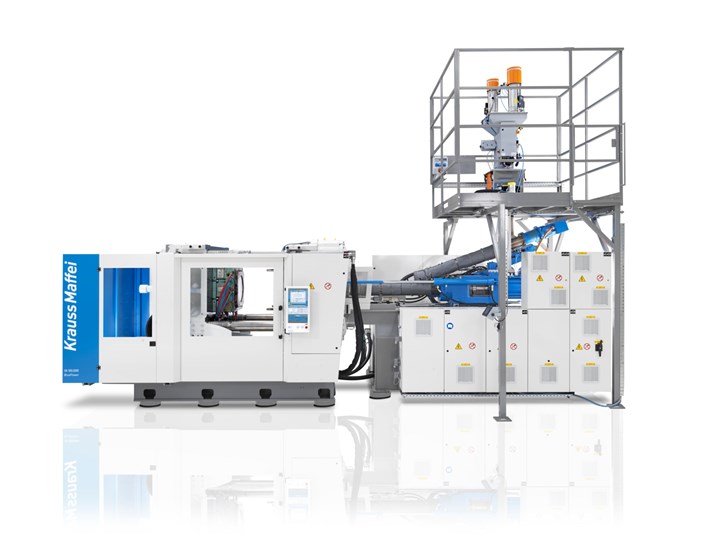
GX 1100-4300 DCIM system features a single-screw extruder in a piggy-back position on top of the molding machine. Source: KraussMaffei
Elsewhere, KraussMaffei’s Direct Compounding Injection Molding (DCIM) process is producing reusable crates from three different recycled materials. The GX 1100-4300 DCIM system features a single-screw extruder in a piggyback position on top of the molding machine. The extruder conveys compounded melt into the plasticizing unit in a single heating process, reducing heat degradation of the polymer. This one-step process also reduces energy consumption and carbon dioxide output. In this cell, KraussMaffei’s smartOperation machine function simplifies press startup and control.
The company is also showcasing a MuCell screw with 30% higher plasticizing performance. The HPS-Physical Foaming screw has a longer three-zone area, which can be universally used for all plastics, including those with and without fiber reinforcement. This increase enables smaller screw diameters to be selected, reducing overall investment, or it can enable greater output by applying the same screw but getting more production.
A PX 121-180 SilcoSet is molding LSR headlight lenses with the help of the APCplus software. ACH Solution supplied the 2-cavity mold and its Servoshot 2G electro-pneumatic valve-gate system, which has needle valve control down to 2 µm. A KraussMaffei LRX 150 linear robot using an end-of-arm-tool from ACH Solution enables inline inspection, including weight check, and separation.
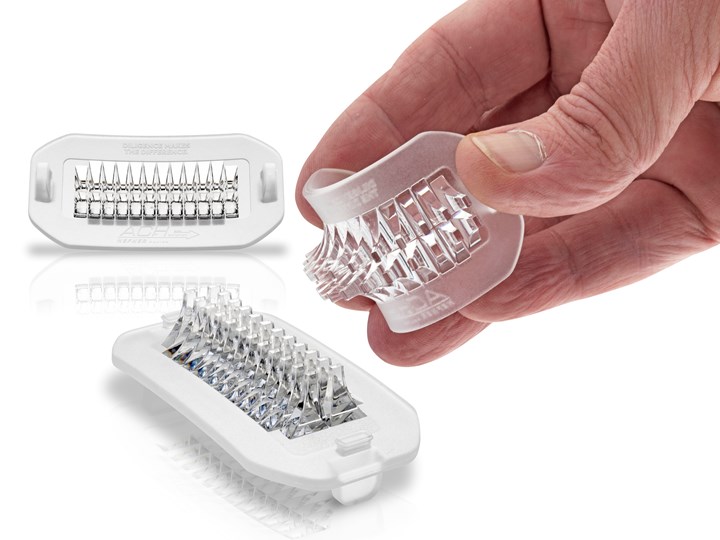
These LSR headlight lenses apply valve-gate technology from ACH Solution. Source: KraussMaffei
KraussMaffei is also highlighting its partnership with the National Institute for Aviation Research (NIAR) at Wichita State University at NPE2024. NIAR will bring its “Frankenstein” manufacturing demonstrator to Orlando. This demonstration model showcases different examples of automotive-matured ultrahigh-rate manufacturing technologies to aerospace, part of a joint KraussMaffei/NIAR research program. NIAR is also showing an aircraft window plug that is undergoing certification efforts for passenger-aircraft-to-cargo conversion activities at NIAR. These composite parts are manufactured using the company’s FiberForm technology, which combines thermoforming of organic sheets and injection molding in a single process.
KraussMaffei’s booth also features a driverless concept vehicle designed for the year 2035, developed at Clemson University with the help of ExxonMobil Chemical and Honda North America. The resulting car is composed 18% by weight from plastics and composites — nearly double the 10% market average.
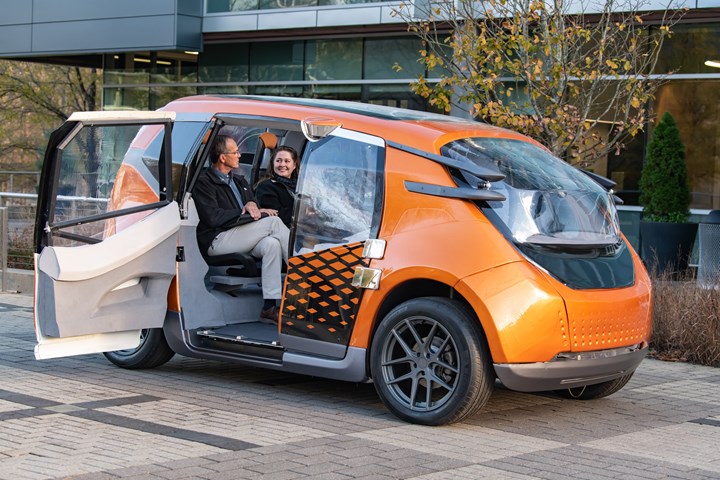
This Clemson University driverless car concept is made up of 18% by weight of plastics and composites. Source: KraussMaffei
Also in mobility, TIME Bicycles, in partnership with KraussMaffei, Fraunhofer USA and Clemson once again, is highlighting their special development project to introduce High-Pressure Resin Transfer Molding (HP-RTM) to the cycling industry. At the show, the first U.S.-produced HP-RTM bicycle is on display. Visitors can register to win the bike, which has a retail value of $8,000. Founded in France in 1987, TIME Bicycles was and is the leading European manufacturer of carbon fiber bicycles, specializing in resin transfer molding (RTM).
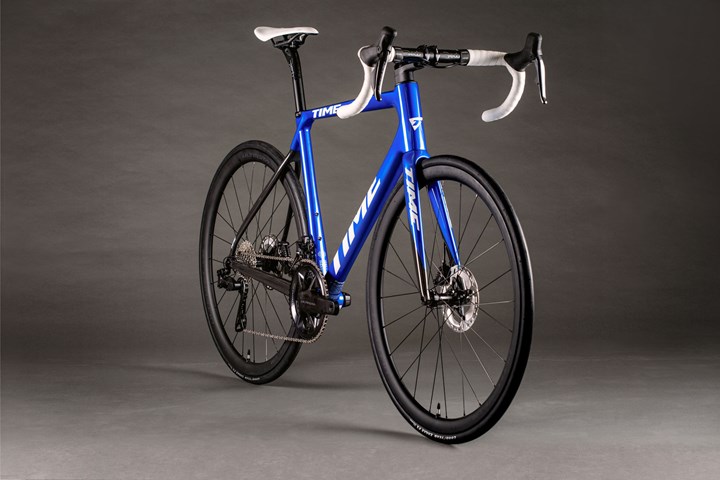
The first U.S.-produced HP-RTM bicycle will be on display at NPE2024. Visitors can register to win the bike with a retail value of $8,000. Source: KraussMaffei
Related Content
Avoid Four Common Traps In Granulation
Today, more than ever, granulation is an important step in the total production process. Our expert explains a few of the many common traps to avoid when thinking about granulators
Read MoreScaling Up Sustainable Solutions for Fiber Reinforced Composite Materials
Oak Ridge National Laboratory's Sustainable Manufacturing Technologies Group helps industrial partners tackle the sustainability challenges presented by fiber-reinforced composite materials.
Read MorePregis Performance Flexibles: In the ‘Wow’ Business
Pregis went big and bold with investment in a brand-new, state-of-the-art plant and spent big on expanding an existing facility. High-tech lines, well-known leadership and a commitment to sustainability are bringing the “wow” factor to blown film.
Read MoreCalculating an Injection Molding Machine’s Carbon Footprint
Arburg has utilized the ISO TS 1467:2018 standard, which determines the greenhouse gas emissions of a product, to help its customers calculate the product carbon footprint (PCF) of its injection molding machines.
Read MoreRead Next
Recycling Challenges Become Opportunities with the Aid of New Technologies
The latest recycling equipment on view at the K Show handles more materials, is more efficient and produces higher quality output than ever achieved before.
Read MoreTechnology Combines Processes for Strong, Lightweight Components
Krauss Maffei's FiberForm technology in an injection molding macine enables the production of fiber-reinforced plastic components.
Read MoreKraussMaffei and NIAR Propel Injection Molded Thermoplastic Composites
The maker of plastics processing equipment has placed a machine and an injection molding expert in NIAR’s ATLAS lab in Wichita, Kansas, to help molding, composites and aerospace take off.
Read More