Interface Six-Axis Robots with Injection Molding Presses
Yaskawa Motoman’s new SPI-67 hardware/software interface for six-axis robots is designed for parts removal from horizontal injection molding machines.
The Motoman Robotics Div. of Yaskawa America, Inc. has introduced a hardware and software interface for its six-axis industrial robots that’s said to easily accommodate the requirements of parts removal from horizontal injection molding machines. The SPI-67 interface can be installed in the YRC controller and connected to HC-Series and GP-Series Yaskawa Motoman robots.
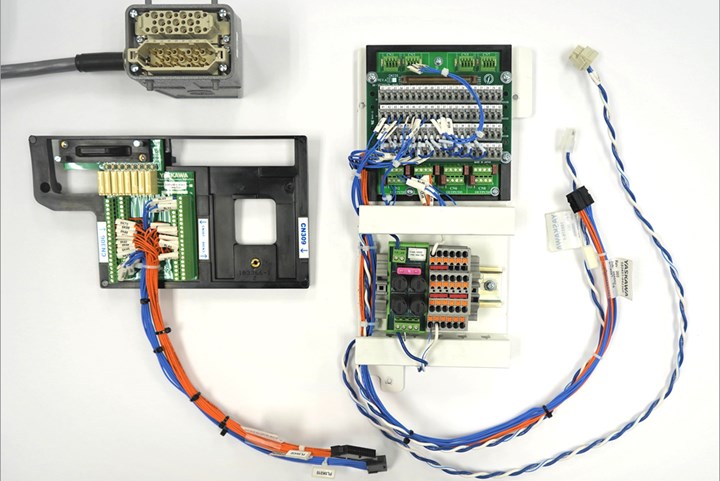
New SPI-67 interface for Yaskawa Motoman six-axis robots and horizontal injection molding machines. (Photo: Yaskawa Motoman)
Prior to this product there were two options—either an external cabinet containing the necessary I/O interfaces, but without some of the integrated components, and at significantly higher cost to customer; or manually connect to available I/O blocks through trial and error and make sure everything is connected correctly, which requires significantly higher expertise.
The SPI-67 interface is said to comply with EuroMap 67 standards for robot-to-press communications and with U.S. SPI electrical interface guidelines. A 50-pin connector acts as a physical link between the robot and the injection machine. Dual-channel/redundant safety signals allow direct connection the press. The SPI-67 transmits standard handshaking signals such as door status, robot operating and ejector position.
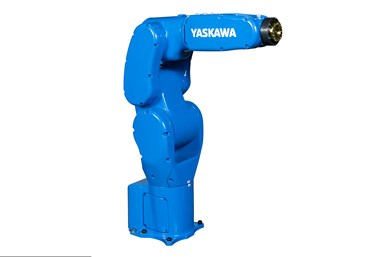
New SPI-67 interface is designed for Motoman GP-Series (pictured) and HC-Series six-axis robots.
(Photo: Yaskawa Motoman)
The new interface mounts within the YRC-1000 controller, so there is no need for an additional cabinet. Direct Connect I/O cards allow easy access to the robots native 40 inputs and 40 outputs, while adding valuable relay outputs. Two unused dual-channel safety contacts can be used to interface with safety input devices, such as light curtains or safety scanners, or can be paired with the Functional Safety Unit (FSU) output functions to obtain dual-channel, dry-contact safety-rated outputs.
Related Content
-
Cobot Creates 'Cell Manufacturing Dream' for Thermoformer
Kal Plastics deploys Universal Robot trimming cobot for a fraction of the cost and lead time of a CNC machine, cuts trimming time nearly in half and reduces late shipments to under 1% — all while improving employee safety and growth opportunities.
-
50 Years...600 Issues...and Still Counting
Matt Naitove marks his first half-century in plastics reporting, with a few of his favorite headlines.
-
How Was K 2022 for Blow Molding?
Over a dozen companies emphasized sustainability with use of foam and recycle, lightweighting and energy savings, along with new capabilities in controls, automation and quick changeovers.