At NPE, Cypet to Show Latest Achievements in Large PET Containers
Maker of one-stage ISBM machines will show off new sizes and styles of handled and stackable PET containers, including novel interlocking products.

FIG. 1 Cypet one-stage ISBM machines are based on a horizontal injection machine base. Images: Cypet Technologies
At the upcoming NPE2024 show in Orlando, Florida, Cypet Technologies of Cyprus will display PET containers made on its one-stage injection stretch-blow molding (ISBM) machines, including several new applications with unusual and even unique shapes. As reported in a February 2022 Close-Up article, Cypet builds machines for PET bottles, jars, jerrycans, drums and pressure vessels. Its equipment can mold containers from 20 ml up to 120 L or more, but it tends to specialize in systems for larger containers. In 2022, Cypet announced its largest machine yet, capable of making 1,000 L intermediate bulk containers (IBCs) from PET. It is now building its first commercial machine for molding these large cubes, expected to begin prototype production in June.
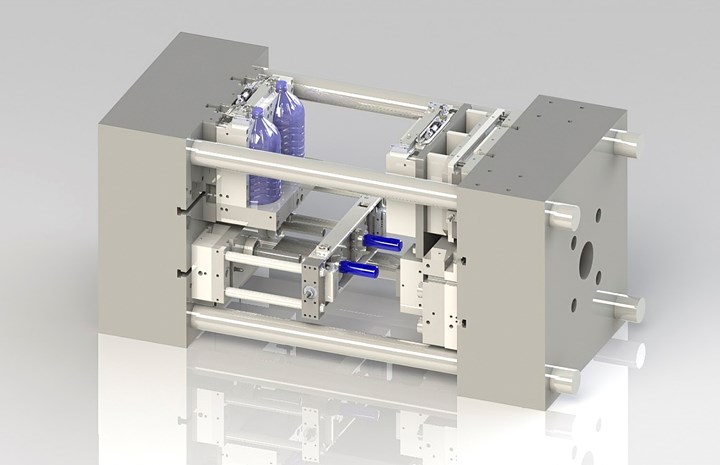
FIG 2 Cypet tooling system molds the preforms horizontally, after which they rotate to a vertical position for extraction by a robot, which places them in the stretch-blowing cavities.
Multifunctional Tooling
As previously described, Cypet’s one-stage ISBM machines are based on an injection molding machine frame (Figure 1), to which special tooling and automation have been added. Preform injection and container stretch-blowing cavities are contained in the same mold. The preforms are molded horizontally, then the cavities rotate to a vertical position, where a robot extracts the preforms and places them in the blowing cavities located above injection cavities (Figure 2). Among recent modifications of the system is a means of rotating the preform before blowing to orient the injection-molded handles in a particular position. Business development leader Michalis Sideris says Cypet now has three machines installed in the U.S. (one started up in February) and two in Mexico.
New Capabilities
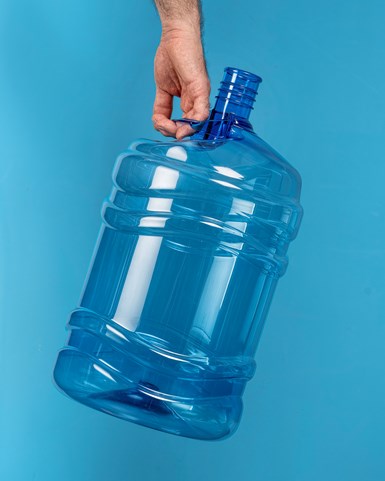
FIG 3 Cypet now can mold four PET 5-gallon returnable water bottles in four cavities using one extruder — said to be a first. Photo Credit: Cypet Technologies
According to Sideris, Cypet produced several “firsts” in 2023. One was its first machine producing 5-gallon returnable water bottles with a new version of an integrated ring handle (injection molded with the neck finish) in four cavities (Figure 3). Sideris says this is the first one-stage ISBM machine capable of such a large PET product in four cavities. Other ISBM systems can handle at most two cavities and require two extruders. Cypet’s system uses one extruder. The water bottle (18.9 L) has a 55-mm neck diameter and weighs 600 to 720 g. It can accommodate up to 50% rPET.
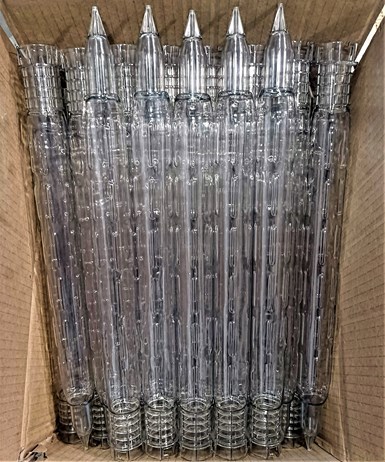
FIG 4 Novel PET agricultural application uses an unstretched base with a pointed extension that interlocks with the neck of an identical part and also enables the assembly to be driven into the soil to support plant growth. Photo Credit: Cypet Technologies
A second new achievement is a novel PET product developed for an agricultural application in Mexico. The finished product is a 424-mm long tube, 40 mm wide with a 40.5-mm neck (Figure 4). Internal volume is only 0.3 L; weight is 62 g. The most unusual feature is a pointed tip in the unstretched base, which enables it to be driven into the soil to serve as a support for plants to grow up around it. Tight tolerances are required in the injection molded base so that it interlocks with the neck of an identical part. In use, five of these parts will be connected end to end, enabling the combined structure to extend 2 meters above the ground. It’s molded in 16 cavities.
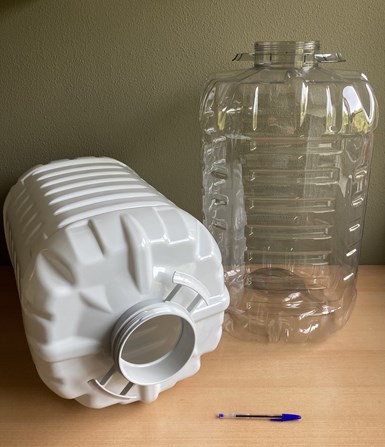
FIG 5 New from Cypet are 60L stackable PET industrial containers with twin integral handles, entering a market where 20 L was the typical size. Photo Credit: Cypet Technologies
Also new in 2023 was Cypet’s first 60-L stackable industrial container with twin integral handles (Figure 5). Up to now, 20 L has been a more typical size in the market for such a container, Sideris says. This container has a 137-mm neck and weighs 1,250 g. It’s stackable two-high.
Other new developments last year were not so much new to the industry as the first time they had been made on Cypet’s machines:
• A PET jar with a blown neck, made by molding a dome above the neck and then removing it with a spin trimmer. Stretch-blowing the neck reportedly saves considerable weight compared with an injection molded neck. This product can use up to 100% rPET.
• Cypet’s first 20-L stackable container with four-high stackability, aimed at edible oil and chemicals. Before, Cypet had made such containers for stacking three high. The new version has thicker walls and comes in model with or without a recess for a funnel. It’s molded in four cavities.
• Cypet’s first family of PET jars with a deep groove grip, available in sizes from 1.3 L to 2.2 L (Figure 6).
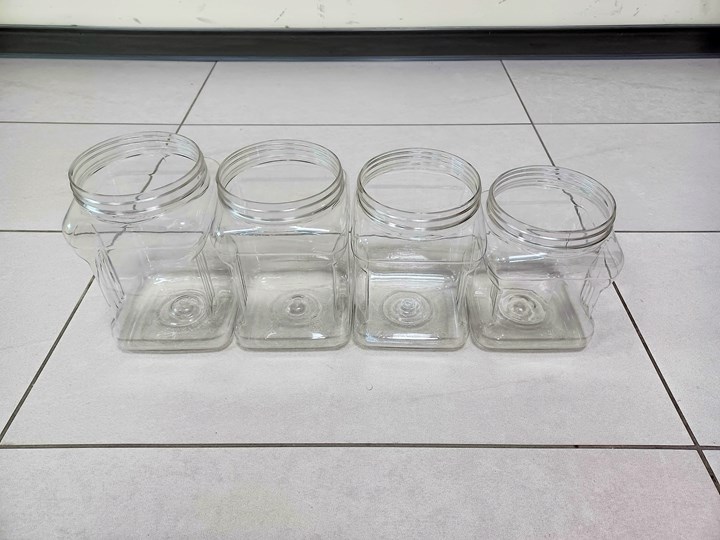
FIG 6 Cypet offers machines and tooling for its first series of PET jars with deep groove grips, from 1.3 L to 2.2 L.
Related Content
Use Interactive Production Scheduling to Improve Your Plant's Efficiencies
When evaluating ERP solutions, consider the power of interactive production scheduling to effectively plan and allocate primary and secondary equipment, materials and resources on the overall production capacity of the business and conclude that this is a key area that cannot be overlooked.
Read MoreHow Inline Vision Inspection Can Minimize Scrap in Molding
Once viewed by injection and blow molders as a necessary evil, machine vision technology today can continuously monitor and improve production while reducing costs.
Read MoreUnderstanding the ‘Science’ of Color
And as with all sciences, there are fundamentals that must be considered to do color right. Here’s a helpful start.
Read More50 Years...600 Issues...and Still Counting
Matt Naitove marks his first half-century in plastics reporting, with a few of his favorite headlines.
Read MoreRead Next
Stretch-Blow 1000-Liter IBCs from PET
Cypet introduces a one-stage ISBM system to provide a clear alternative to HDPE bulk containers.
Read MoreRecyclable One-Way PET Keg
CYPET’s blow-molded keg addresses safety and cost issues of steel kegs.
Read MoreProcessor Turns to AI to Help Keep Machines Humming
At captive processor McConkey, a new generation of artificial intelligence models, highlighted by ChatGPT, is helping it wade through the shortage of skilled labor and keep its production lines churning out good parts.
Read More