Compounding
In compounding, various materials (polymers, additives, etc.) are mixed and melted—generally in an extruder of some type—then pelletized. Most compounding extruders purchased nowadays are of the twin-screw corotating/intermeshing variety, though counterrotating twins are used for some applications. Compounding extrusion lines are typically equipped with gravimetric feeding systems that dose materials into the extruders at very specific rates. In certain applications, extruders are equipped with vent ports that pull unwanted moisture and other volatiles from the polymer stream.
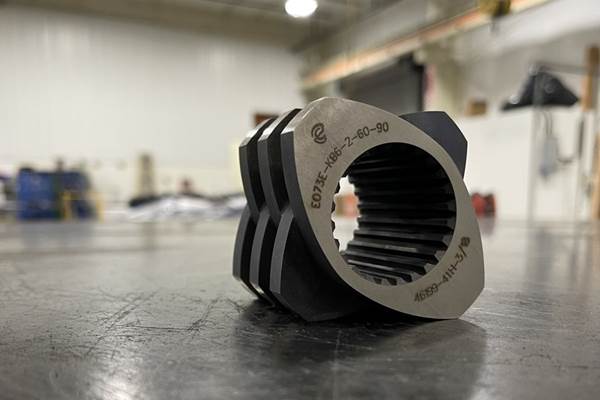
Narrow Your Compounding Search
ESSENTIAL READING
VIEW ALLHow to Configure Your Twin-Screw Extruder for Mixing: Part 5
Understand the differences between distributive and dispersive mixing, and how you can promote one or the other in your screw design.
Read MoreHow to Configure Your Twin-Screw Extruder: Part 3
The melting mechanism in a twin-screw extruder is quite different from that of a single screw. Design of the melting section affects how the material is melted, as well as melt temperature and quality.
Read MoreHow to Configure Your Twin-Screw Extruder -- Part 2
Follow these tips to configure your twin-screw elements to promote feeding and solids conveying.
Read MoreWhat to Know About Your Materials When Choosing a Feeder
Feeder performance is crucial to operating extrusion and compounding lines. And consistent, reliable feeding depends in large part on selecting a feeder compatible with the materials and additives you intend to process. Follow these tips to analyze your feeder requirements.
Read MoreHow to Configure Your Twin-Screw Barrel Layout
In twin-screw compounding, most engineers recognize the benefits of being able to configure screw elements. Here’s what you need to know about sequencing barrel sections.
Read MoreImproving Twin-Screw Compounding of Reinforced Polyolefins
Compounders face a number of processing challenges when incorporating a high loading of low-bulk-density mineral filler into polyolefins. Here are some possible solutions.
Read MoreLatest Compounding News And Updates
Equipment for Compounding, Reactive Extrusion, Devolatilization, Foaming and Direct Extrusion
NPE2024: Leistritz to focus on advances made via twin-screw extrusion.
Read MoreTwin-Screw Showcased in Circular Economy Demo
A KraussMaffei twin will upcycle pelletized blood vials, which will then be overmolded on another press to produce bottle openers.
Read MoreTwin-Screw Compounder Reduces Energy Consumption in Recycling
NPE 2024: ZSK FilCo combines filtration and compounding in a single step.
Read MoreSystem Quickly, Safely Cleans and Wipes Pelletizing Dies
Unit mounts directly to the die body in a space-saving design that avoids thermally dependent dimension stackups.
Read MoreStar Plastics Names New CEO
Star Plastics, a custom compounder, has named Daniel T. McMullen CEO.
Read MoreRibbon Blenders Boost Powder Blending Efficiency, Safety
Solid double ribbon agitator is well suited for center discharge.
Read MoreFeatured Posts
Configuring the Twin Screw Extruder: Part 4
For many compounding operations, material is fed to the extruder at the feed throat. This is the case when feeding a single polymer or a blend of polymers mixed with solid additives. Some ingredients, however, present a challenge in feeding. Here’s how to solve to them.
Read MoreCompounder ‘Walks the Walk’ on Sustainability
Sustainability is one of Techmer PM’s four pillars and guiding principles. And the company has recently earned third-party certification that ensures at least 99% of its waste is diverted from landfills.
Read MoreHow to Maintain Pelletizing Quality When Acid Attacks
Developments in the chemistry of polymers and additives have made corrosion a real problem in pelletizers. Here’s how to ward it off.
Read MoreHow to Configure Your Twin-Screw Extruder: Part 3
The melting mechanism in a twin-screw extruder is quite different from that of a single screw. Design of the melting section affects how the material is melted, as well as melt temperature and quality.
Read MoreMore Than a Compounder: They Have the Science to Create New Custom Materials
Insight Polymers & Compounders leverages its expertise in polymer chemistry to develop next-generation materials.
Read MoreHow to Configure Your Twin-Screw Extruder -- Part 2
Follow these tips to configure your twin-screw elements to promote feeding and solids conveying.
Read MoreFAQ: Compounding
How can I optimize my twin-screw compounding process?
We identify problems in compounding as “chronic” if the results are the same every time a particular formulation is run. For these problems, the treatment requires redesigning the screw configuration or modifying the compounding process. This is the only way to cure such problems.
Many new players have emerged in the biopolymer space with new materials and many new formulations. Co-rotating twin-screw extruders provide excellent material mixing capabilities for all polymers, including biopolymers. You should consider your machinery supplier as a development partner to achieve your goals in the areas of melt and mix quality, production rates, and other parameters, regardless of formulation. Make sure your machinery supplier has the facilities and the know-how to help you test material formulations and improve your processes.
Pelletizers are essential components in resin manufacture, compounding, masterbatch production, and recycling. A high-volume system that is appropriate for a polymerization plant will be very different from one that suits the needs of a toll compounder. One that can produce micropellets for use in masterbatch may not be the best choice for processing post-consumer regrind. Here are some different types of pelletizers.
- UNDERWATER PELLETIZERS
- WATERRING PELLETIZERS
- STRAND PELLETIZERS
Compounding Supplier Categories
- Rebuilt Screws or Barrels
- Blenders (non-intensive)
- Automation/Systems Integration
- Web Winders, Unwinds, Rewinds
- Single-screw Extruders
- Recycling--Purchasing Scrap or Waste Plastics
- Technical and Trade Associations
- Custom Compounding, Formulating--Thermoplastics
- Barrier Surface Treatment
- Liquid Mixers
- Plastics Trade Shows/Conferences
- Machine Alignment Services
- Slot Orifice Coaters
- Machinery Rebuilding
- Sheet Take-off Systems
- Film Take-off Systems
- Web Brakes, Clutches, Chucks
- Extrusion Dies
- Training Programs in Plastics
- Shipping & Logistics
- R&D, Training Institutes
- Web Inspection Systems
- Rebuilt Motors and Drives
- Pipe Take-off Systems
- Web Guides, Edge Detectors
- Wire and Cable Take-off Systems
- Prototyping Services
- Pipe Thickness Measuring Equipment
- Roll Coaters
- Mold/Tooling Simulation and Analysis Services
- Curtain Coaters
- Custom Machine Builders
- Custom Size-reduction (Grinding) Services
- Profiles, Tubing, Hose Take-off Systems
- Consultants - Design, Manufacturing, Purchasing
- Plastic Lumber Extrusion/Molding Systems
- Web Slitter/Rewinders
- Part/Mold Inspection or Digitizing
- Knife Coaters
- Materials Testing Services
- Film, Sheet, Coated Web Thickness Measuring Equipment
- Hydraulic Oil Filtering/Reclaim Service
- Web Tension Controls
- Motionless Mixers
- Publishers of Plastics Information (Books, Reports, CDs)
- Mold Texturing, Tool Engraving
- Intensive Nonfluxing Mixers
- Multiple-screw Extruders
- Web Cleaning Equipment
- Machine Installation Services
- Hard Facing, Surface Treating of Tooling, Equipment
- Mold/Tooling Design Services
- Coextrusion Dies, Feedblocks
- Web Slitters
- Business Services for Plastics (Finance, Insurance, Leasing)
- Plasma Coating Systems
- Ram Extruders
- Intensive Fluxing (melting) Mixers
- Monofilament/Multifilament Take-Off Systems
- Radiation Processing Services
- Machine Maintenance Services
- Rotary Screwless Extruders
- Used Molds
- Used Machinery
- Environmental Monitoring and Analysis
- Equipment Cleaning Services
- Custom Decorating/Finishing Services
- Profiles, Tubing, Wire Thickness Measuring Equipment
- Tumblers
- Scanning & Metrology Services
- Roll Mills