Sweden's Site Zero Sorts Plastic Packaging Waste Into 12 Fractions
Svensk Plastatervinning polymer sorting plant has a 3.1-mile sorting line that separates postconsumer waste, including polyeolefins, PET, PS, EPS, PVC and more for recycling.
Svensk Plastatervinning of Sweden celebrated the opening of Site Zero, a plastic sorting plant in Motala, Sweden. The plant features Tomra and Sutco equipment, and can sort plastic packaging waste into 12 fractions for recycling.
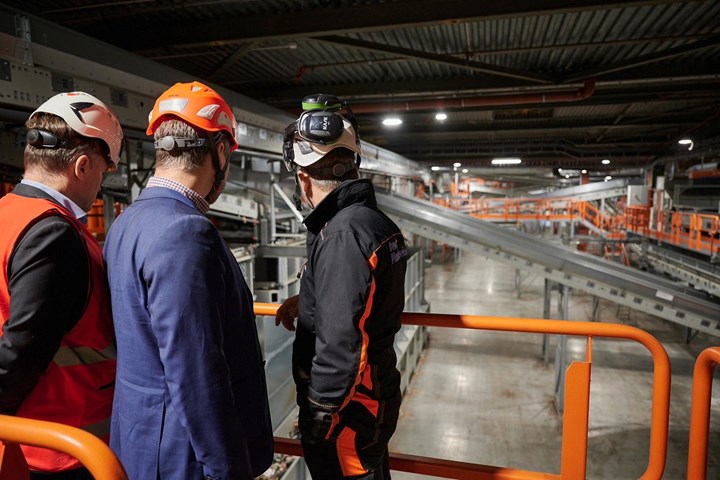
Svensk Plastatervinning conducted a tour of the Site Zero facility, which is now operational. Photo Credit: Tomra
Originally opened in 2019, the plant was built in collaboration with Sutco and featured Tomra sorting technology. With the new extension, the plant is expected to process 46.3 tons of material per hour and recover 12 different types of plastics from mixed plastic packaging waste.
“Around 33% of plastic packaging in Sweden is recycled, but unfortunately there is still a lot of recyclable materials lost. This offers great potential, one that we are committed to unlocking and transforming into a valuable opportunity for the country and the environment,” says Mattias Philipsson, Svenks Plastatervinning CEO. “Since 2019, we have successfully been producing four different types of plastics for recycling. We always wanted to do more and with the latest technology, we’re able to accomplish our goals.”
Site Zero is equipped with more than 60 Tomra Autosort machines. The 3.1-mile long sorting line can separate postconsumer waste into 12 different polymer types, including a variety of polyolefins, PET, PS, EPS, PVC and more. According to Tomra, purity levels of up to 98% can be achieved. The clean material fractions are then sent to recyclers in the EU, but Site Zero is also planning to add recycling capacities to further process the main fractions locally.
The Autosort machines are connected to Tomra Insight, a cloud-based data platform for monitoring of all sorting lines. “It keeps the pulse of the sorting plant by collecting sorting data, creating reports, and sends notifications if there are any inconsistencies that affect the overall performance of the sorting line,” says Oliver Lambertz, VP and head of operations and feedstock sourcing at Tomra Feedstock. “If this data is used as a strategic management tool, efficiencies can be increased and costs lowered.”
Related Content
-
Foam-Core Multilayer Blow Molding: How It’s Done
Learn here how to take advantage of new lightweighting and recycle utilization opportunities in consumer packaging, thanks to a collaboration of leaders in microcellular foaming and multilayer head design.
-
Breaking News From NPE2024
Here is a firsthand report of news in injection molding, extrusion, blow molding and recycling not previously covered.
-
Scaling Up Sustainable Solutions for Fiber Reinforced Composite Materials
Oak Ridge National Laboratory's Sustainable Manufacturing Technologies Group helps industrial partners tackle the sustainability challenges presented by fiber-reinforced composite materials.