New Name, Products, Technology— But Same Service Philosophy
Schoeneck Containers is now Radius Packaging, but customer needs are still the focal center of this blow molder’s business. Those customers will benefit from the company’s push toward automation, sustainability, and new products in injection molding and stretch-blown PET.
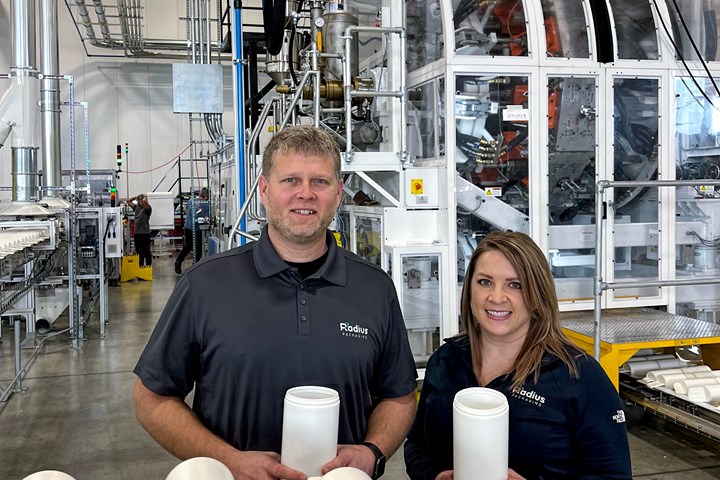
At its new plant in Delavan, Wis., Radius Packaging operates high-output machines like this new Graham wheel for long runs with fully automated product conveying and packing. Shown here, Josh Kouba, v.p. of engineering, and Crystal Humphreys, dir. of marketing. (All photos: Radius Packaging)
Change has been a consistent theme for half a century at Radius Packaging, known until last month as Schoeneck Containers Inc. Thirty years ago, this blow molder focused mainly on PVC. But today, the company processes mainly HDPE, plus a little PVC and some PP. And there’s PET in its future, according to Josh Kouba, v.p. of engineering. “We’ve looked into EPET but are not yet set on it,” he elaborates. “This year, however, we will start injection stretch-blow molding of PET on one-stage machines.” This new direction for the company was set by its customers’ desires for a more recyclable high-clarity alternative to PVC, Kouba notes. Sustainability is driving other initiatives at Radius, but those are only some of the changes afoot at the company.
The company’s focus has changed over the years from PVC to HDPE, and now it sees a growth opportunity in PET.
Since its launch by Bob Schoeneck in 1972, Schoeneck Containers operated out of the same plant (though much enlarged over time) in New Berlin, Wis. But in mid-2019, the company opened its second plant, in Delavan, Wis. In addition to 173,000 ft2 in New Berlin, the Delavan plant has 250,000 ft2, which is ample room for the new PET ISBM machines, as well as the drying system to serve them.
Though the company’s DNA is in blow molding, there is some injection molding going on at Delavan. The company has been molding caps for some time, but it just obtained a patent on an injection molded canister and lid. “It’s
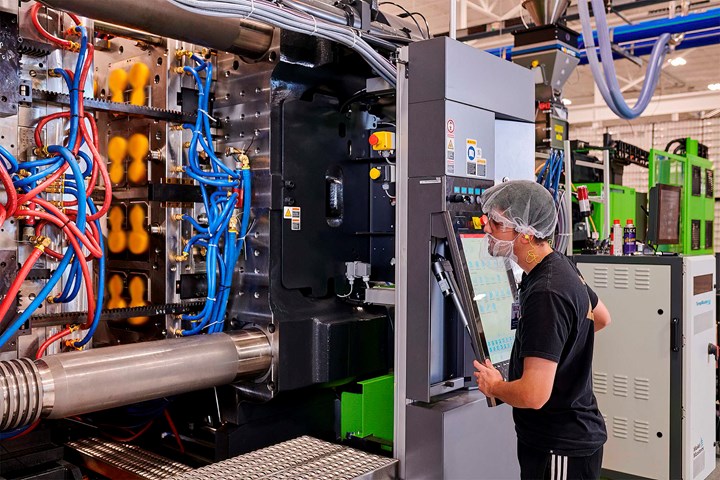
Besides molding caps, Radius sees opportunity in proprietary injection molded containers. Here is a 1200-ton Engel press at the Delavan plant.
nestable, unlike blow molded containers,” explains Kouba, “so we can get more product on a truck. Also, it has a one-way snap-fit lid with a flip-top cap. It’s almost tamper-evident, and it allows the canister and lid to be molded of the same material for recyclability.” He adds, “We definitely see growth in injection molding.”
For Kouba, “The Delavan plant represents the future for the company.” It’s organized around highly automated systems and longer production runs, while New Berlin specializes in shorter runs and frequent changeovers. At Delavan, five large blow molding machines run with only five people on a shift. “No one touches the bottles until they’re palletized and strapped and moved with a forklift to the stretch-wrapper,” says Kouba. And his team is looking into using Omron automated guided vehicles (AGVs) to shuttle incoming boxes of bottles from the New Berlin plant to labeling operations at Delavan. Radius is already using Omron’s articulated-arm cobots (collaborative robots) in New Berlin to reduce labor in packing bottles. Kouba’s engineers are even thinking of mounting a jointed-arm cobot on an AGV. Kouba notes that automation has proved to be valuable insurance against chronic labor shortages, which were exacerbated by the coronavirus pandemic.
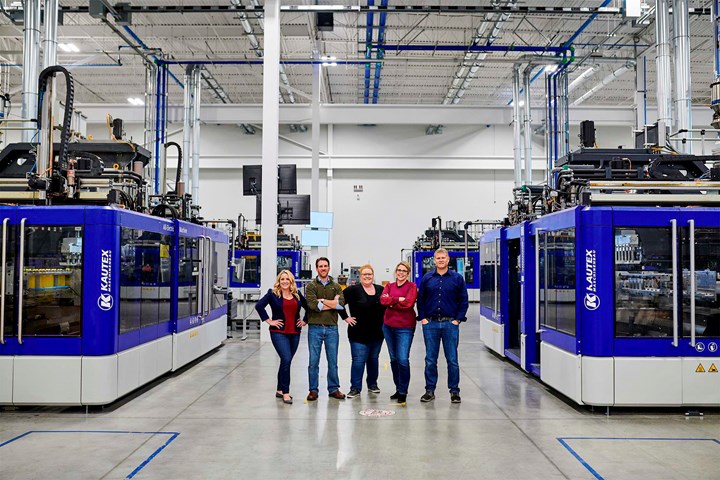
Four new Kautex all-electric machines with multilayer capability at the Delavan plant embody future directions for Radius. L-R: Crystal Humphreys; Zack Fredericks, product development mgr.; April Keller, APQP engineer; Lisa Esser, dir. of quality; Josh Kouba.
Automated bulk material handling also helps combat labor shortages. “Ninety-nine percent of our resin comes in railcars,” says Kouba. “Delavan has room for 10 railcars. Other molders take in 10 to 15 semi-trucks a day to fill their silos.”
Labeling operations at Delavan reflect another future-oriented initiative at Radius. “We’ve added capabilities in value-added services,” Kouba notes. “That includes labeling—both pressure-sensitive and heat-transfer—as well as reshipper cartons and other special packaging. For example, we can send the customer a pallet of bottles in cartons and another pallet of caps. So, the customer can fill the bottles right in their cartons and then apply caps. We also offer custom design services, including 3D printed physical prototypes.”
New machines at Radius will be multilayer-capable and probably all-electric or hybrid.
Delavan also exemplifies the company’s efforts to implement sustainable manufacturing. The plant was constructed with energy-efficient LED lighting and lots of natural light via floor-to-ceiling windows oriented for a Southern exposure. Delavan also has an advanced cooling system using an adiabatic cooler mounted on a slab in back of the plant. This system uses ambient air to provide “free cooling” during the cooler months, which lasted until April 13 last year, Kouba points out. In addition, an air-cooled compressor to serve the molding machines has louvers that open to all the waste heat to warm the plant “for free” during the winter.
What’s more, the manufacturing area at Delavan is climate controlled, which means no shrouding is needed around the machines to prevent mold sweating—and resulting cosmetic defects on products—during the warm, humid months. As Kouba points out, “When we moved the injection machines from New Berlin to Delavan, they performed so much better because the molds could run colder without sweating. It’s also more comfortable for the people working there. Two good reasons why we may do this later in New Berlin.”
New Name, Same Culture
The company today has grown to employ 270 in the two plants, which house 36 continuous-extrusion blow molders, including wheels (both a homegrown Schoeneck design and a new Graham Engineering model), shuttles (including new Kautex long-stroke all-electrics) and reciprocating-screws. The number-one market served is home care in terms of volume, but nutritional and wellness is one of the fastest-growing segments. Other market sectors are professional cleaning, specialty food and beverage, personal care and pet care. Stock and custom containers constitute about equal shares of the business today.
Growth of that business has outpaced the overall market, says Kouba, and the company kept growing throughout the COVID-19 pandemic. In fact, one of the firm’s larger products—disinfectant wipes—actually benefitted from the pandemic, as did bottles for hand sanitizers and the like.
So why replace a successful and long-familiar brand with a new one? Crystal Humphreys, director of marketing, cites two reasons. One is that ownership of the company passed from the Schoeneck family in mid-2020 to Mason Wells, a Milwaukee-based private-equity firm. Second, Humphreys says the new name “Radius” is meant to reflect one constant in the company’s culture: “It’s our promise to keep customers at the center of the business. They are our packaging partners.”
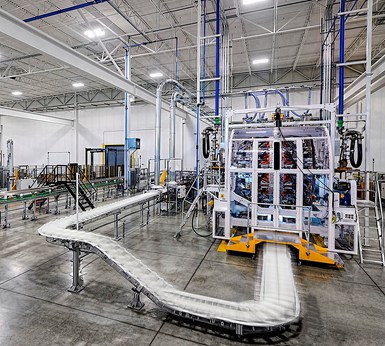
Radius’ latest investment is a high-volume Graham wheel machine, capable of producing 22 containers in a single rotation, with automated takeoff, so that no one touches the bottles until a forklift removes the boxed product.
Kouba adds, “We’re investing in abilities to grow with our customers.” He points to the upgrades in value-added services and automation, as well as the pending entry into PET containers, as examples. He also emphasizes the culture of friendly, open interactions with customers as a legacy of the company’s history of family ownership. “In a word, we’re flexible. The competition wants orders of 20 million to 30 million bottles, all packaged in a certain way—take it or leave it.
“Our approach is, ‘Whatever you need, we’ll figure it out together.’ We like truckload orders, too—our sweet spot is in the 1 million to 10 million range. But if you need just 250,000 of a stock product for which we already have tooling, and perhaps it’s already running for someone else, we’ll extend the run just for you.”
Adds Humphreys, “We’re a ‘high-touch’ organization, not an empty email address. Our CEO Tom Frank is constantly in contact with customers, either on the phone or in meetings.”
Persistance of that culture is ensured by continuity in Radius’ staff. “We have a lot of tenured brainpower here,” says Kouba. “Many of our staff have 10 to 20 years’ service, some even 35+ years.”
Some of that brainpower is devoted to R&D in proprietary products. An example is a monolayer HDPE bottle with a barrier additive. It’s aimed initially at deck cleaners (converted from metal cans) but could also be useful for food containers.
Sustainable Manufacturing Goals
Radius has what it calls a Green Team that’s focused on energy efficiency and achieving “zero landfill.” As noted above, the new Delavan plant employs energy-efficient lighting, heating and cooling systems. It also houses two all-electric and one hybrid (electric/hydraulic) injection machines. In 2016, the company installed its first all-electric blow molders. Kouba sees more electric injection and blow molding machines coming in the future, for energy efficiency, cleanliness and quietness.
The company reuses almost all its own scrap, even large purgings and even PVC. The PET strapping used on shipping containers is all recycled material, and used strapping is sold to waste dealers, along with a small amount of other unusable scrap.
PCR is more expensive than virgin resin: “If you want to be sustainable, you have to be willing to pay for it.”
Two other key sustainability efforts are devoted to lightweighting and increasing use of post-consumer recycled (PCR) plastics. Kouba says lightweighting is a goal in all the firm’s new container designs, which have achieved around 20% weight reduction on some food and household cylinders.
“Our use of HDPE PCR is small but growing,” says Kouba. “Some of our monolayer household containers are as much as 70% PCR.” Radius uses PCR mainly in custom containers, but on request it can add PCR to a stock container—what Kouba calls “tailored stock.”
Radius also can bury PCR in the middle layer of a bottle with virgin skin layers inside and out, so the PCR has no direct contact with the bottle’s contents and is not visible to the consumer. “With multilayer, we can regrind bottles with plastic heat-transfer labels and bury them in the middle layer. Otherwise, highly colored particles of the ground-up label would be visible on the outside of the bottle,” Kouba explains. “We also use multilayer bottles to save color cost by using it only on the outer skin layer.”
Radius already has four shuttle machines with multilayer heads from W. Müller, as well as a high-output Graham wheel with multilayer capability. “We’re seeing more and more demand for this,” notes Kouba. “So we’ve decided that all new machines will have multilayer capability. It means more expense for two additional extruders, but it’s cheaper to do it upfront rather than modify the machine later on.”
Radius buys PCR in the form of precompounded pellets, so it has encountered no processing issues that have faced users of PCR flake. However, Kouba notes that PCR is still more expensive than virgin resin: “If you want to be sustainable, you have to be willing to pay for it.”
Radius is betting that more and more customers will be willing, so it is keeping close tabs on developments in recycling. “We tried some PP PCR just to get experience with it,” Kouba says, acknowledging that availability of recycled PP is in its early stages but is attracting more and more industry interest. “We’re also keeping an eye on suppliers for availability of chemically recycled material. We want to be ready when it comes on the market.”
Related Content
50 Years of Headlines … Almost
I was lucky to get an early look at many of the past half-century’s exciting developments in plastics. Here’s a selection.
Read More50 Years...600 Issues...and Still Counting
Matt Naitove marks his first half-century in plastics reporting, with a few of his favorite headlines.
Read MoreProcessing Megatrends Drive New Product Developments at NPE2024
It’s all about sustainability and the circular economy, and it will be on display in Orlando across all the major processes. But there will be plenty to see in automation, AI and machine learning as well.
Read MoreAutomation Evolution: From Robots to Work Cells, Solo Devices to Integrated Systems
Injection molding automation has progressed from devices to systems, from simplicity to more complex capabilities. The author traces this development through various levels of automation – all still available choices today – and analyzes the costs and capabilities for each level.
Read MoreRead Next
Making the Circular Economy a Reality
Driven by brand owner demands and new worldwide legislation, the entire supply chain is working toward the shift to circularity, with some evidence the circular economy has already begun.
Read MoreRecycling Partners Collaborate to Eliminate Production Scrap Waste at NPE2024
A collaboration between show organizer PLASTICS, recycler CPR and size reduction experts WEIMA and Conair will seek to recover and recycle 100% of the parts produced at the show.
Read More