Understanding Melting in Single-Screw Extruders
You can better visualize the melting process by “flipping” the observation point so that the barrel appears to be turning clockwise around a stationary screw.
Over the years I have talked to many people with lots of experience in extrusion who do not understand how single screws melt polymer, or how the extruder drive supplies that energy. Many think the barrel heaters supply much of the energy entering the polymer, which is mystifying to me … and completely wrong.
In all fairness, it is difficult to visualize melting with the screw turning in the barrel because of the geometry. But if you flip the observation point—imagine the barrel turning around the screw—you can more clearly visualize the forces involved. It’s not any different than imagining the sun turning around the earth when we know the opposite is true. In an actual extruder the screw typically turns counterclockwise, when viewed from the drive end (or clockwise from the discharge end), and the barrel is stationary. But if we flipped the observation point so that we’re “sitting” on the screw, the barrel would appear to be turning clockwise around a stationary screw.
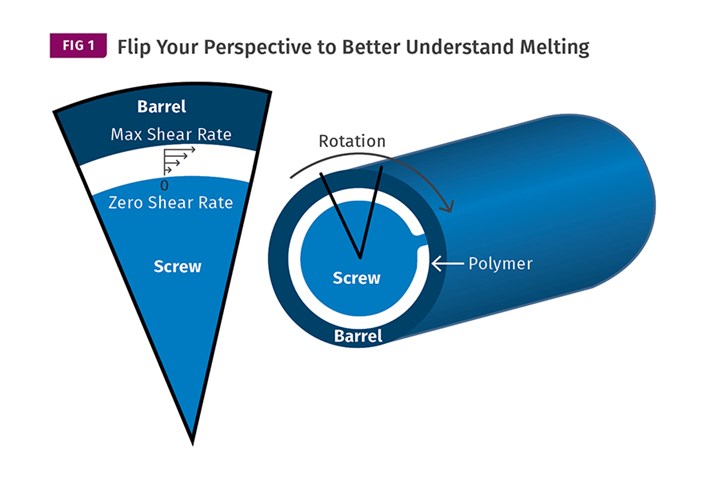
Melting is hard to envision. But if you “flip” the observation point by imagining the barrel turning around the screw you can more clearly visualize the forces involved. (Illustration: J. Frankland)
Barrel heating is initially required before startup to get the screw filled with melted polymer and to obtain a surface temperature where the polymer will stick to the barrel. From then on, almost all the energy entering the polymer comes from the energy required to turn the screw relative to the barrel—or in our “flipped” case, the barrel relative to the screw. Because of the initial heating, the polymer is stuck to the barrel and is pushed forward by the angle of the screw flights. Once screw rotation starts, the polymer is melted almost entirely by shear.
“Shearing” is defined as applying a force that distorts one surface of an object relative to another surface. Shearing an object introduces heat into it. In an extruder the distorting force to shear the polymer requires energy to rotate the screw in the layer of viscous polymer. The rotational energy from the drive is converted from mechanical to thermal energy via shear putting heat into the polymer.
The barrel heaters contribute almost nothing to melting once screw rotation begins.
The shear rate is proportional to the speed of rotation and the thickness of the object, achieving the maximum near the barrel surface and zero at the screw root, as shown in Fig. 1. The amount of shear is then proportional to the viscosity of the polymer at various temperatures during shearing. Using a gradually reducing channel depth in the “compression section” of the screw forces any unmelted polymer closer to the barrel wall, where it gets the maximum shear.
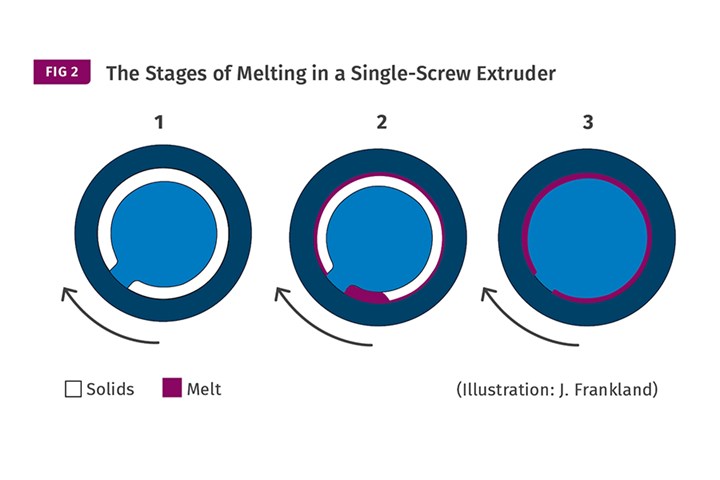
(Illustration: J. Frankland)
In the sequence 1-5 shown in Fig. 2:
- Screw channel is filled with unmelted polymer leaving the feed throat.
- Due to barrel heating, a thin film of melt forms on the barrel wall.
- That thin film gets sheared by the relative rotation of the barrel and screw.
- The process proceeds with the help of the screw design as the channel depth is reduced (compression section), which forces the unmelt up against the barrel, maximizing shear on the unmelt.
- With proper screw design for that polymer, all the unmelt can be converted to melt at the proper processing temperature in a controlled fashion.
Even after reaching the melting or softening point, the shearing continues due to the viscosity of the melt. Most of the drive power in a single-screw extruder is used to rotate the screw in the polymer. Typical distribution of the drive power is 85-90% to melting, with the remainder to mixing, pressurization and forwarding. The barrel heaters contribute almost nothing to melting once screw rotation begins. In fact, for many extrusion operations, the barrel heaters are in cooling mode most of the time.
Each polymer requires a different amount of energy from the drive based on the amount of energy required to raise its temperature to the desired processing temperature. The specific heat of the polymer governs that amount of energy. In screw design, the viscosity of the polymer while being sheared determines the energy introduced by each revolution of the screw. The viscosity decreases as the polymer progresses from solid to melt. The initial polymer temperature governs the total amount of energy required from the screw drive. For example, preheated polymers require less power from the drive.
ABOUT THE AUTHOR: Jim Frankland is a mechanical engineer who has been involved in all types of extrusion processing for more than 50 years. He is now president of Frankland Plastics Consulting, LLC. Contact jim.frankland@comcast.net or (724)651-9196.
Related Content
Luigi Bandera: Pioneer of Plastic Extrusion With Vision
Get to know the life and legacy of Luigi Bandera, the visionary behind Costruzioni Meccaniche Luigi Bandera, who revolutionized plastic extrusion technology and earned a place in the Plastics Hall of Fame in 2024.
Read MoreDr. Chris Rauwendaal: Creator and Inventor in Plastic Extrusion
Dr. Chris Rauwendaal's impact on plastic extrusion is characterized by innovation and creativity, evident in his contributions to both theory and practical applications. Recognized with induction into the Plastics Hall of Fame in 2024, his career encompasses a wide range of achievements, from pioneering revolutionary screw designs to authoring the esteemed "Polymer Extrusion" book.
Read MoreTop 10 Markets for Polyethylene Film Extrusion | #4 Sheet & Tubing
Editorial director Jim Callari continues his conversation with Mastio & Co. President Kevin Huntsman on the largest markets for Polyethylene Film Extrusion. Next on the countdown of the largest markets for polyethylene film extrusion is sheet and tubing.
Read MoreSensing Instrumentation for More Sustainable and Automated Polymer Processing
NPE2024: Dynisco solutions support move to nontoxic materials and adds feedback control capability.
Read MoreRead Next
Extrusion: The Importance of Zone 1 Barrel Temperature
Tweaking the temperature settings of the first barrel zones may not yield the desired result. In fact, they may yield the opposite. Here’s why.
Read MoreUnderstanding the Influence of Screw Geometry on Melting Rate
They are not as closely connected as most processors think. Here’s why.
Read MoreWhy Barrel Temperatures Have a Small Effect on Melt Temperature
Extruders are not like ovens. Tweaking barrel-temperature profiles will not influence melt temperature all that much. Here’s why.
Read More