Understanding the Effect of Pressure Losses on Injection Molded Parts
The compressibility of plastics as a class of materials means the pressure punched into the machine control and the pressure the melt experiences at the end of fill within the mold will be very different. What does this difference mean for process consistency and part quality?
We can simplify the injection molding process by focusing on what the plastic “experiences” as it travels through the machine and into the mold. This perspective can be referred to as “injection molding from the plastic’s point of view” or scientific injection molding. When considering process, tooling, material and/or part design changes, it is useful to consider how the plastic will behave or respond.
There are many parameters that can be adjusted on an injection molding machine, but it is important to acknowledge these adjustments will affect one or more physical plastic conditions, with the four main plastic conditions being:
- Plastic Temperature
- Plastic Flow Rate
- Plastic Pressure
- Plastic Cooling Rate & Time
Because plastics are compressible, we will detect a pressure loss, pressure gradient and pressure differential through the runner system, across the gate and down the cavity. Terms such as pressure loss, pressure gradient and pressure differentials all refer to physically compressing the plastic to a greater or lesser degree.
How is this behavior possible? Plastics are compressible mediums because of the space between the polymer molecules, and their volume is based on the temperature and pressure applied.
One way to illustrate pressure losses in real life is to think about the use of compressed air. If we measure the air pressure at the compressor itself along with the air pressure at the end of the hose, we will observe a drop in that air pressure. For example, suppose an air compressor produces 80 psi, but at the end of a 100-foot hose, the measured air pressure is 75 psi. Because the air can be compressed, we see a 5 psi pressure loss along 100 feet of the hose. For the sake of our discussion, we will neglect the effects of frictional losses, even though they exist.
Let us turn our attention back to plastic and focus on the pressure detected inside the cavity during the packing phase of the injection molding process.
In Figure 1, in-cavity pressure transducers are at position A (post-gate) and position B (at the end of the fill inside the mold cavity). Assume that 15,000 psi pressure is programmed during the packing phase at the front of the screw. From this theoretical example, there is a pressure loss of 6,000 psi from in front of the screw to the cavity pressure sensor at A, and a further pressure loss of 2,000 psi between sensors located at A and B. To conceptualize this phenomenon, envision pushing on a sponge during the packing phase. Due to the application of the pressure, compression of the sponge occurs while the amount of pressure transmitted down the length of the sponge decreases.
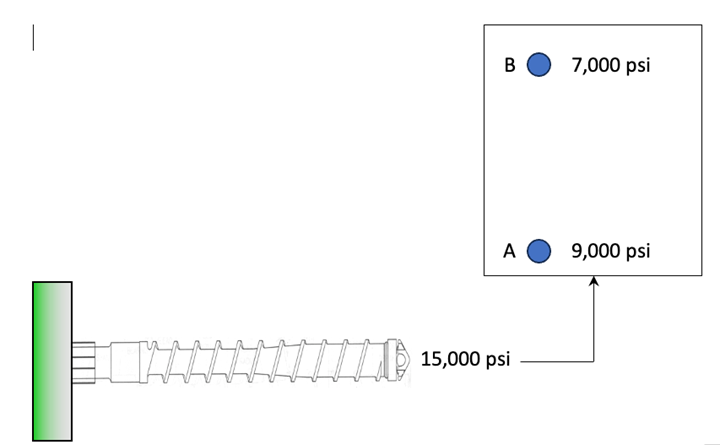
From 15,000 psi in front of the screw during packing to 9,000 psi at the gate and 7,000 psi at the end of fill, pressure is lost throughout the molding process. Source: Umberto Catignani
This pressure loss will cause the plastic to be compressed to a higher degree at location A post-gate versus B at end of fill, which will affect the plastic part such that more packing of the plastic is observed at A with less packing at location B. Furthermore, there will be less shrinkage of plastic at A versus more shrinkage at location B, and larger part dimensions of the plastic component at A, with smaller dimensions, such as part width, at B.
An example of a plastic part that has a greater amount and severity of sink marks is pictured. This variation in sink marks is caused by the pressure loss down the cavity, and greater pressures and less overall shrinkage near the gate. In the future, consider this phenomenon when altering the process settings, or tooling, material and part design.
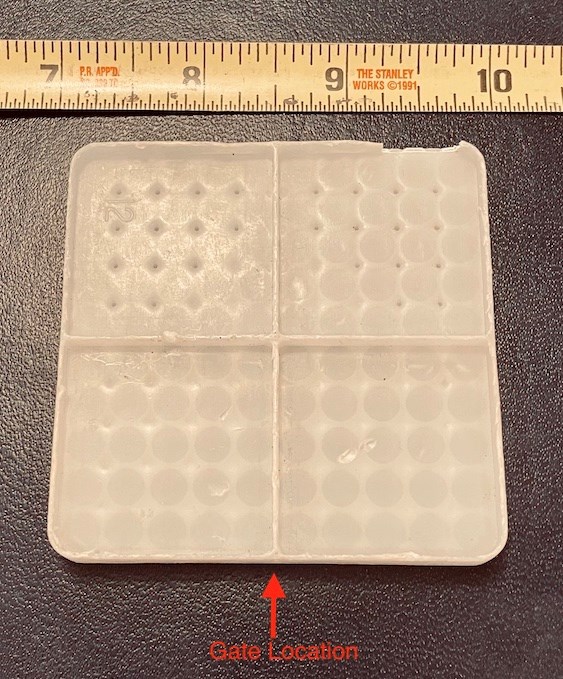
The variation in sink marks in this part is caused by the pressure loss down the cavity and greater pressures and less overall shrinkage near the gate. Source: Umberto Catignani
About the author: Umberto Catignani is president of Orbital Plastics Consulting Inc., a consulting firm that has more than 100 years of combined experience in scientific injection molding, training, material selection, part design review, in-mold instrumentation, project management and equipment selection. Catignani is past president of the Southern Section of SPE and has more than 28 years of hands-on injection molding experience. He has certified and trained hundreds of plastic professionals in the industry and has served as an expert witness. Past employers include IBM, General Motors, Delphi Automotive and Husky Injection Molding Systems. Catignani earned a master’s degree in polymer engineering from The University of Akron and a bachelor’s in materials engineering from the University of Cincinnati. Contact: 404-849-6714; umberto@orbitalplastics.com.
Related Content
The Effects of Temperature
The polymers we work with follow the same principles as the body: the hotter the environment becomes, the less performance we can expect.
Read MoreTunnel Gates for Mold Designers, Part 1
Of all the gate types, tunnel gates are the most misunderstood. Here’s what you need to know to choose the best design for your application.
Read MoreDensity & Molecular Weight in Polyethylene
This so-called 'commodity' material is actually quite complex, making selecting the right type a challenge.
Read MoreHow to Stop Flash
Flashing of a part can occur for several reasons—from variations in the process or material to tooling trouble.
Read MoreRead Next
Troubleshooting: Injection Molding Seven Steps Toward Scientific Troubleshooting
A scientific troubleshooter is not someone who pushes buttons faster or has more tricks up his or her sleeve.
Read MoreInjection Molding: Simulation Factors in Material Compression and Machine Response During Injection
Moldex3D version R17 increases prediction of filling speeds and pressures.
Read MoreHow to Manage Pressure Loss in Injection Molding
Achieving a process window wide enough to ensure consistent part quality depends on achieving sufficient pressure at end of fill.
Read More