Finnish Startup Gets IMSE Lighting Patent
TactoTek’s newly-patented technology available for licensing.
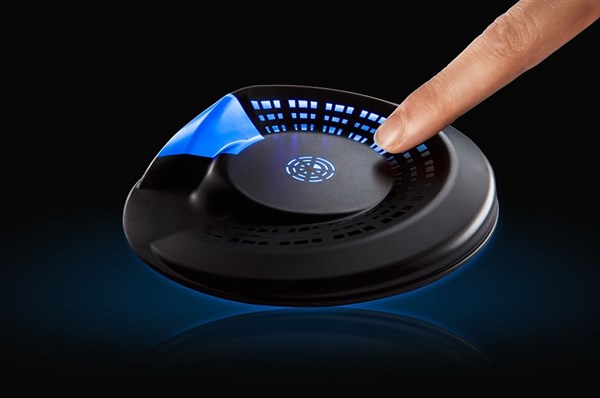
TactoTek’s newly-patented technology available for licensing.
An interesting technology from a Finnish startup that has a unique method for integrating printed electronics such as circuitry, touch controls and antennas, as well as discrete electronic components such as LEDs, into injection molded plastics has been issued a U.S. patent (9297675). Applications for the so-called “illuminated indicator structures for electronic devices” include automotive, home appliances, wearables and health care.
The new technology from TactoTek, based in Oulu, Finland (U.S. office in Cupertino, Calif.) reportedly enables sophisticated lighting in very thin 3D plastic ‘smart surfaces’. “This patent recognizes a key innovation for injection molded structural electronics (IMSE) technology—employing the plastic material that is the structure of a part as a light guide. Using this technique, we can create very bright, evenly distributed illumination within structures as thin as 2-millimeters (0.079 in.),” according to CTO and co-founder Antti Keranen.
For illumination, TactoTek’s IMSE technology consolidates printed electronics and LEDs within the 3D molded plastic part and uses the plastics themselves to conduct light. This, in contrast with traditional electronics designs, which typically include a cosmetic surface structure and use a separate light pipe structure to direct lighting to the surface from a flat, rigid printed circuit board (PCB).
TactoTek’s approach of using the molded cosmetic surface as a light guide removes design constraints that had previously prescribed thick, multi-part assemblies, explains head of product management Hasse Sinivaara. “As we remove parts, we remove design time, weight and minimize electrical and mechanical assembly—very appealing when considering form factor innovation and total cost of ownership.”
TactoTek’s patented and patent-pending technologies integrate a mixture of well-known production technologies into a unique approach that enables mass production of 3D structural electronics. These include flexible circuit printing, surface-mounting electronic components, thermoforming, in-mold labeling (IML), and injection molding.
The approach starts with an IML material. Decoration, if desired, is printed, followed by conductive circuitry, and in some designs, printed touch controls and printed antennas. Electronic components are mounted using standard high-speed pick-and-place machinery. Electronics can be as simple as LEDs or as complex as microprocessors and are affixed to the IML using specialized adhesives able to withstand the temperature and pressure of injection molding. With electronics in place, the IML carrier is used as an insert for injection molding.
According to senior v.p. of marketing Dave Rice, the company uses a range of plastics that are standard for high-pressure, high-temperature injection molding, including: PC, ABS, and acrylic for rigid structures; TPU and hybrids, e.g., TPU/silicone for flexible structures.
Here is Rice’s answer when I asked if the company plans to license its newly-patented technology: “Our core business model is to help customers adapt their traditional electronics designs to TaktoTek IMSE technology and, develop mass production ready prototypes. For mass production, in some cases, we will manufacture parts ourselves; in most cases, we will license our technology and train a third party—typically an established Tier 1 supplier, to mass produce those parts.”
Related Content
A Systematic Approach to Process Development
The path to a no-baby-sitting injection molding process is paved with data and can be found by following certain steps.
Read MoreThree Key Decisions for an Optimal Ejection System
When determining the best ejection option for a tool, molders must consider the ejector’s surface area, location and style.
Read MoreGot Streaks or Black Specs? Here’s How to Find and Fix Them
Determining the source of streaking or contamination in your molded parts is a critical step in perfecting your purging procedures ultimately saving you time and money.
Read MoreBack to Basics on Mold Venting (Part 2: Shape, Dimensions, Details)
Here’s how to get the most out of your stationary mold vents.
Read MoreRead Next
For PLASTICS' CEO Seaholm, NPE to Shine Light on Sustainability Successes
With advocacy, communication and sustainability as three main pillars, Seaholm leads a trade association to NPE that ‘is more active today than we have ever been.’
Read MoreMaking the Circular Economy a Reality
Driven by brand owner demands and new worldwide legislation, the entire supply chain is working toward the shift to circularity, with some evidence the circular economy has already begun.
Read MorePrecision Processing Requires Precision Equipment
Moretto offers plastics processors and micromolders for a broad suite of auxiliary solutions targeted specifically for precision processing.
Read More