Suppliers Team to Run Tubing, 3D Filament at Medical Show
At MD&M/Plastec West show in Anaheim, Conair to run extrusion line with technology partners Davis Standard and Zumbach Electronics.
At MD&M West/Plastec West 2022, Conair Group, together with technology partners Davis Standard and Zumbach Electronics, will be demonstrating production of extruded 0.06-in. (1.5-mm) dual-lumen “Double D” thermoplastic elastomer (TPE) medical catheter.
In addition, the line will be used to produce 1.7 mm filament made of PLA, which will be used in a 3-D-printer operating in Booth 4024 during the tradeshow, which is being held in Anaheim, Calif. April 12-14, 2022.
In operation, PLA will be processed in a Davis Standard 1-in. MEDD Series (Medical Extruder Direct Drive) extruder. Its key features include interchangeable barrel assemblies and replaceable feed-sections liners for multiple materials and applications. Easy-to-clean stainless-steel surfaces, direct drive motor, simplified maintenance, and operator accessibility are other key advantages for medical cleanroom applications.
From the extruder, melt passes through a cross-head filament extrusion die and a non-contact calibrator in the Conair HTMP multi-pass vacuum-sizing/cooling tank. Wafer inserts, sized to the filament, seal the entrance to the tank to allow for vacuum sizing.
From the tank, the filament goes to a Medline Puller and on to a Conair ATC Series coiler set up with multiple small spools on the coiling shaft. System programming will wind one spool after another until all spools are full. Then the coiler indexes to another shaft with empty spools so the operation can unload to get ready for the next cycle.
A floor-mounted ultrasonic loop sensor monitors the incoming product, automatically adjusting coil speed and traverse motion to wind product smoothly, without the friction or tension that can distort delicate extruded products. The unit’s automatic coil-isolation feature locks out access during coil transition, then actuates upper and lower safety gates that isolate the actively winding spindle, enabling users to safely access and remove full coils on the other side of the cabinet.
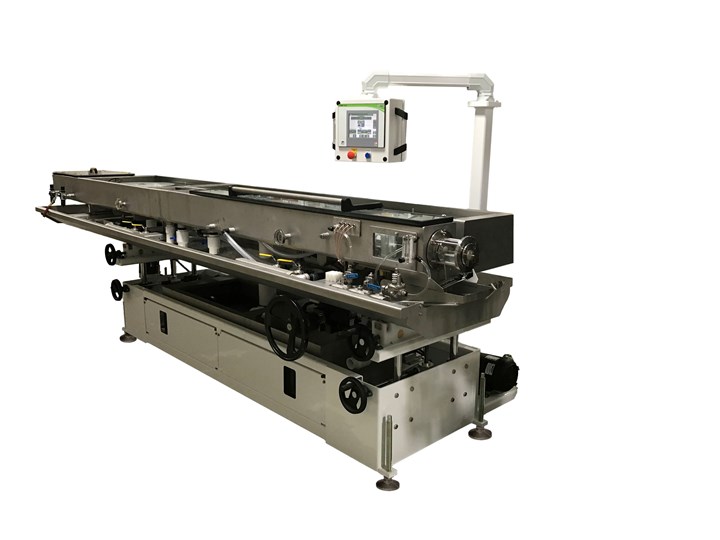
The multi-pass tank is a space-saving Conair innovation. Instead of making a single pass through a long tank, the extrudate follows a Z-shaped path so that the compact, 12-ft-long HTMP tank provides cooling time equivalent to a 30-ft tank while fitting neatly into the 20 x 30-ft Conair tradeshow booth.
“Floor space in any manufacturing plant is costly,” says Ernie Preiato, v.p., extrusion sales, “and even more so in a cleanroom environment. Considering our multi-pass tanks occupy only about a third of the space a full-length, single-pass tank requires, the savings and convenience are considerable.”
Catheter Extrusion
On Thursday, April 14, Conair and its partners will be shifting the extrusion line over to production of the dual-lumen “Double D” TPE medical catheter. In addition to the David Standard extruder and Conair upstream and downstream equipment, the line will also feature an ultrasonic wall-thickness gauge provided by Zumbach Electronics. The extruder control integrates these downstream inputs to ensure consistent quality automatically.
TPE will be dried Conair’s Carousel Plus dX drying system equipped with a DC-B premium control and Drying Monitor. The patented Drying Monitor monitors temperatures at multiple points in the drying hopper, providing early detection of poor drying conditions so corrections can be made to prevent processing of improperly dried material. The Carousel Plus drying system also includes an onboard conveying option to a Conair MedLine Tube Loader on the extruder feed throat. Using a second tube loader on the drying hopper, the Carousel Plus dryer will draw source material to be properly dried before entering the extrusion process. Other Conair medical-grade MedLine auxiliaries include a Thermolator temperature control unit (TCU) and a Conair EP1A-02 (two-ton) portable air-cooled chiller.
After processing through the extruder, tubing leaves the cross-head die and immediately enters the Conair HTMP multi-pass tank. Like all MedLine auxiliaries, it is specially configured, documented, and supported for cleanroom applications.
The HTMP tank uses a series of motorized sheaves to gently pull extrudate through cooling water, starting with a 6-ft vacuum chamber that creates a positive differential in air pressure within the extruded tube. This slight outward pressure, generated by the vacuum in the tank, helps stabilize tube dimensions before additional cooling passes while preventing any “drool” of cooling water out of the tank’s feed opening that could mar the surface finish of the product.
The Zumbach Electronics ultrasonic gauges—one each near the tank entrance and exit—ccontinuously monitor and report changes in tube wall thickness on a control screen as the tubing cools. Further downstream from the tank, a Zumbach 3-axis OD laser gauge provides not only closed-loop dimensional control, but also displays the tube profile for concentricity adjustments. Together, data from the ultrasonic and laser gauges are used to regulate puller speed and cooling-tank vacuum to maintain critical tube dimensions over the production run.
The finished catheter tube then moves through the Conair MedLine Puller/Cutter to produce 6-in. samples that will be given away to attendees. The catheter may also be directed to the ATC Series Coiler, which is set up in this case, to produce a single large coil.
Related Content
Extruder Alignment: Important, but Only Half the Equation
The other half? Aligning and supporting downstream equipment. Here are best practices.
Read MoreSpecialty Purging Compounds Optimize Color and Material Changeovers
Selecting of the correct purging compound can speed up material and color changeover time and reduce scrap. You’ll even save on material.
Read MoreThe Importance of Viscosity in Melting
The calculations required to determine the right melt temperature for each polymer are complicated. Knowing the power-law coefficient and the consistency index of the polymer you run might prove useful.
Read MoreUnderstanding the ‘Science’ of Color
And as with all sciences, there are fundamentals that must be considered to do color right. Here’s a helpful start.
Read MoreRead Next
For PLASTICS' CEO Seaholm, NPE to Shine Light on Sustainability Successes
With advocacy, communication and sustainability as three main pillars, Seaholm leads a trade association to NPE that ‘is more active today than we have ever been.’
Read MoreBeyond Prototypes: 8 Ways the Plastics Industry Is Using 3D Printing
Plastics processors are finding applications for 3D printing around the plant and across the supply chain. Here are 8 examples to look for at NPE 2024.
Read MoreRecycling Partners Collaborate to Eliminate Production Scrap Waste at NPE2024
A collaboration between show organizer PLASTICS, recycler CPR and size reduction experts WEIMA and Conair will seek to recover and recycle 100% of the parts produced at the show.
Read More