Westminster Tool and Mantle Partner on 3D-Printed Mold Technology
The Connecticut mold maker will be one of two beta-testing sites for Mantle’s TrueShape metal 3D printer, with a medical device already borne out of an ongoing collaboration.
Mold maker Westminster Tool (Plainfield, Conn.) released details of a medical device case study utilizing Mantle’s TrueShape metal 3D printer and announced it would be one of just two beta-testing sites for the metal printing technology, with plans to take delivery of a prototype machine this spring. The announcements came at the PTXPO (March 29-31; Donald E. Stephens Convention Center; Rosemont, Ill), where Westminster Tool and Mantle were both exhibiting. The two companies began working together on advancing metal 3D printing of tool cavities in 2019.
At the event, Westminster Tool released details of a collaboration with Mantle Inc., and medical material compounder Foster Corp. The companies worked together to create medical-grade forceps from a highly filled resin as a means to test the design, material, manufacturing and injection molding process with metal 3D printed cavities, applying Mantle’s TrueShape.

Westminster Tool printed the mold cavities, including conformal cooling channels, for a pair of forceps utilizing Mantle’s TrueShape metal 3D printing technology.
Photo Credit: Westminster Tool
The forceps were molded by Westminster Tool from a Foster-supplied Rilsan FKZM 65 O TD MED resin. In a presentation at PTXPO, Scott Kraemer, senior application engineer at Mantle, said the compound was a 65% glass-filled biobased polyamide material. It took 86 hours to print the cavity and the core in tool steel, using Mantle’s technology, and the mold features conformal cooling. The companies were able to laser etch the cavities, which went from the initial design phase to final production in just three weeks.
In addition to allowing conformal cooling, Mantle’s printed cavities also made the use of a subgate possible so that Westminster Tool can mold thousands of parts without worrying about eroding the gate areas with the highly filled and abrasive resin.
Mantle’s TrueShape technology suite entails the printer, which also has 3-axis CNC machining capabilities; software to map out printing and machining; and proprietary materials, including H13 and P20 tool steels. The materials come in sealed cartridges and are composed of metal particles and binders with the consistency of toothpaste. Material is extruded by the printer in layers that are heated and dried. This cooks off the binders and leaves only metal with the consistency of a crayon, which can then be machined.
Printed components are finished in a sintering furnace, which raises their temperature to just below the melting point of the metal. The resulting metal parts can be treated like any other tool steel and be subjected to machining, welding, grinding, polishing and more. TrueShape has a build area of 8 by 8 by 6 in, with a maximum part size of about 5 by 5 in. Paul DiLaura, Mantle’s chief commercial officer, told Plastics Technology that the company’s sweet spot is components measuring 3 by 4 by 1 to 1.5 in.
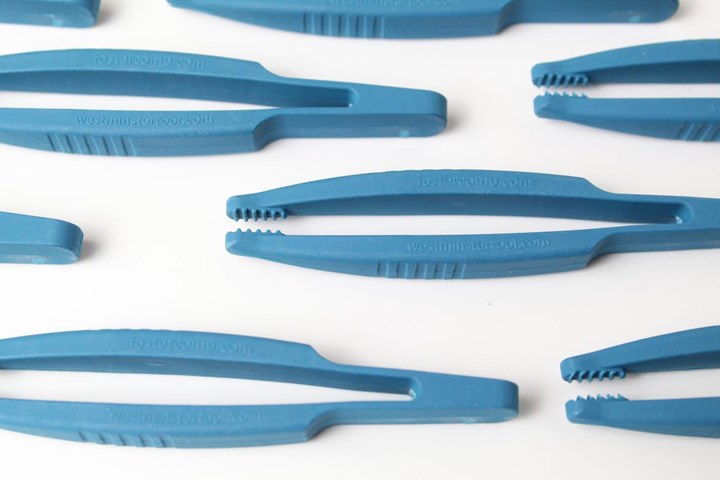
These medical forceps are molded from a 65% glass-filled biobased polyamide compound supplied by Foster in cavities printed using Mantle’s TrueShape technology.
Photo Credit: Westminster Tool
Related Content
-
Back to Basics on Mold Venting (Part 1)
Here’s what you need to know to improve the quality of your parts and to protect your molds.
-
Hot Runners: A View from the Bottom Up
Addressing hot-runner benefits, improvements, and everyday issues from the perspective of decades of experience with probably every brand on the market. Part 1 of 2.
-
How to Select the Right Tool Steel for Mold Cavities
With cavity steel or alloy selection there are many variables that can dictate the best option.