Auxiliaries: Sensor Kits Enable Non-Computer-Controlled Auxiliaries to Connect to Cloud Platform
User-installed sensor kits are now available for use not only with Conair auxiliaries on the SmartServices platform, but with a range of competitive auxiliary equipment.
New SmartServices sensor kits from Conair now make it possible to connect operating, performance, and alarm data from non-computer controlled auxiliary equipment to the SmartServices platform, Conair’s cloud-based Industry 4.0 solution for auxiliary equipment monitoring, management, and analysis.
The user-installed sensor kits are now available for use not only with Conair auxiliaries, but with a range of competitive auxiliary equipment including:
- Temperature control units (TCU);
- Positive-displacement vacuum-conveying pumps;
- Single- and dual-stage regenerative vacuum pumps;
- Portable loading/conveying systems and
- Desiccant dryers
These kits were created by Conair so auxiliary equipment that does not utilize computerized controls could be equipped with digital sensors and communications capabilities and linked to the cloud-based SmartServices platform with the same ease as newer equipment. Each user-installed kit contains common digital hardware, plus fluid-system fittings, sensors, and wiring specific to the equipment type. Digital hardware includes a SmartServices expansion box that receives sensor inputs via wiring and a SmartServices hub that securely exchanges data, via the facility’s local network, with the cloud-based analytics platform.
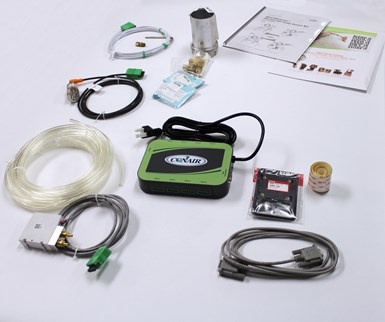
After installation, the new sensors monitor the performance and operating/maintenance status of each auxiliary, collecting data and operating information specific to the auxiliary type. For example, sensors on the TCU can monitor coolant pressure, temperature, and flow rates, while those on vacuum pumps and conveying systems will monitor air flows and speeds, vacuum levels, and the like. At the same time, sensors will also monitor for operating alarms, track maintenance alerts, and observe the vibration and temperature status of motors for anomalies that could signal possible problems.
Related Content
-
How Machine Monitoring Delivers Tangible Results
Much more has been said than done about reaping the benefits of data driven manufacturing among plastics processors. Good technology is essential, but change management is the most difficult part of the process. Here’s how to think about both.
-
Automation in Thermoforming on the Rise
Equipment suppliers’ latest innovations exemplify this trend driven by factors such as labor shortages, higher-speed thermoformers and tighter quality control.
-
How Production Monitoring Can Make You a Better Processor
Real-time information on all your production equipment not only boosts productivity and profitability, but it encourages proactive vs. reactive thinking and sharing of best practices. See how this approach benefited a blow molder with 19 plants.