Odor-Minimization Technology for High-Quality Recycled Plastics
Kreyenborg’s new IR-Fresh modular system safely and efficiently removes interfering odors in plastics.
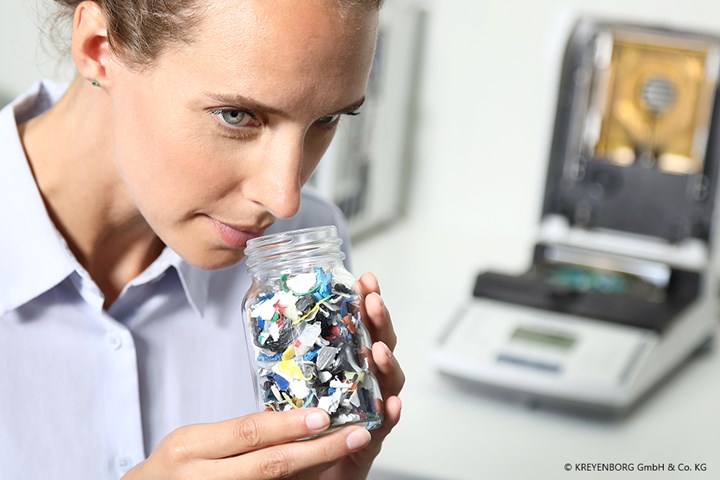
New odor minimization technology for high-quality recycled plastics has been developed by Germany’s Kreyenborg. (Represented in the U.S. by eFactor3, Llc, Charlotte, N.C.) The company has developed sustained, high-level expertise in plastics recycling, with solutions for decontamination of PCR-PET, crystallization, drying, and heating of bulk materials, using infrared technology. Furthering this technology is the new IR-Fresh modular system for the safe and efficient reduction of interfering odors in plastics, according to the company. Here’s how it works:
▪ In the first process step, an infrared module installed above the material bed heats the material quickly and directly to the optimum temperature level for the plastic in question. In this process, the continuous rotation of the drum ensures a homogeneous mass flow with a defined dwell time (applying the first-in/first-out principle). Due to the rotation and mixing elements integrated in the spirals, the material is continuously mixed in the drum with constant surface exchange. Combined with controlled heating, this is said to ensure considerable odor elimination, even within a very short residence time.
▪ In the second process step, the remaining odorous substances in the regrind or granules are removed by a thermal-physical cleaning process in the IR-Fresh Conditioner--an insulated hopper that keeps the material to be decontaminated at a temperature range ideal for the decontamination process by means of a hot purge-gas. Excellent results for deodorization and decontamination reportedly can be achieved through the interaction of the main process parameters of air-flow, temperature, and residence time.
Due to its modular design, the IR-Fresh process can be used continuously in two stages both for regrind - before the extrusion process - and for granules after the extrusion process. It is possible to either integrate the IR-Fresh Conditioner as an individual step in the process chain or to operate it as an independent, stand-alone solution either continuously or discontinuously. The IR-Fresh system is also suitable as a retrofit solution for integration in existing plants.
Related Content
-
Evolving Opportunities for Ambitious Plastics Recycler
St. Joseph Plastics grew from a simple grinding operation and now pursues growing markets in recycled PP, food-grade recycled materials, and customized post-industrial and post-consumer compounds.
-
Reversing Logistics for Plastic Film Recycling
Learn how Mainetti built a circular supply chain for clear film packaging.
-
Scaling Up Sustainable Solutions for Fiber Reinforced Composite Materials
Oak Ridge National Laboratory's Sustainable Manufacturing Technologies Group helps industrial partners tackle the sustainability challenges presented by fiber-reinforced composite materials.