Novel ‘Clamtainer’ Extends Thermoformer's Reach in Packaging
Uniquely secure latching expands applications for Jamestown Plastics’ patented clamshell package design.
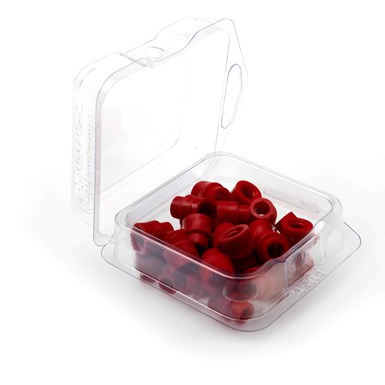
A broad range of products can be packaged in a Clamtainer, with food and produce in the lead but including nuts and bolts, consumer batteries and more. (Photos: Jamestown Plastics)
A unique clamshell-type packaging design first patented seven years ago by thermoformer Jamestown Plastics in Brocton, N.Y., has gained significant ground in a broad range of packaging applications. These range from food products such as baked goods and produce such as berries, to nuts, bolts and screws, consumer batteries and more. “Any product in a conventional clamshell can benefit from our Clamtainer technology and both the producer and the consumer will be happier”, says CEO Jay Baker. Moreover, the company also sells Clamtainer products directly to consumers, such as its Ammo Buddy Line and storage lines.
Founded in Jamestown, N.Y., in 1958 when its initial customer base was primarily in preservation packaging for military bearings, durable commercial products and retail consumer goods, Jamestown Plastics became a Baker-family-owned business in 1976. Jay became the first full-time salesperson in 1984 and succeeded his father as CEO in 1999. In 2021, his son Jessup Baker was named president, becoming the third Baker generation to hold this position. The company has plants in Jamestown and Brownsville, Texas, operating over 10 inline thermoformers; and as of 2022, in Meadville, Pa., with the new acquisition of Tamarack Packaging.
In 2015, Baker patented the Click-It Closure technology and the innovations surrounding it. The company holds patents globally on the geometry of the Clamtainer and more specifically its closure mechanism. “This is the essence of our patents. We utilize a pin that engages into a hole in the vertical sidewall of the Clamtainer. We achieve a very high level of closure strength; unlike clamshells utilizing a friction interference geometry such as a snap button or rim lock, we are the first to utilize shear strength. Think of the Click-It Closure like you would the deadbolt on your front door. Very easy to engage but once closed extremely difficult to open the door unless the deadbolt is turned to the open position.”
Baker explains why a broad array of different products can be packaged in their Clamtainers. Basically, the geometry of the hole is the same, so that you do not have to retool to make different sized Clamtainers. “Which Clamtainer is used is predicated on the size of the product residing in it. We also can and do make custom inserts if the customer desires, which simply sit inside one of our stock Clamtainers, reducing tooling costs for our customer versus a traditional clamshell.” Most of their Clamtainers are made of rPET, though some, like those for consumer batteries, are made of impact-modified PVC. The company does not currently license its technology and has two websites devoted to Clamtainer-- the industrial-sector site clamtainerpackaging.com and clamtainer.com for direct sales to consumers.
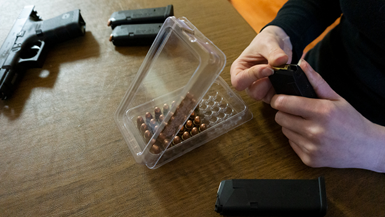
Most of the company’s Clamtainers are made with rPET, though Clamtainers for consumer batteries are made of impact-modified PVC.
The Click-It Closure technology led to expansion into Certified Child-Resistant packaging and additional solutions for the medical and cannabis markets, in addition to the company’s proprietary product lines, including Clamtainer and the DoomBox mousetrap, which encloses the proven , patented SmackDown kill-bar style trap in a clear container that allows you to see trapped mice and keeps pets and kids out. In 2018, the DoomBox was commercialized as the first childproof mouse trap.
This thermoformer also has long served the automotive industry (in 2012, it created the hood liner for the Tesla Model S introduction) as well as electronics, general industrial heavy-gauge thermoforming, and healthcare/medical.
Related Content
Medical Molder, Moldmaker Embraces Continuous Improvement
True to the adjective in its name, Dynamic Group has been characterized by constant change, activity and progress over its nearly five decades as a medical molder and moldmaker.
Read MoreHow to Extrusion Blow Mold PHA/PLA Blends
You need to pay attention to the inherent characteristics of biopolymers PHA/PLA materials when setting process parameters to realize better and more consistent outcomes.
Read More‘Monomaterial’ Trend in Packaging and Beyond Will Only Thrive
In terms of sustainability measures, monomaterial structures are already making good headway and will evolve even further.
Read MoreIn Sustainable Packaging, the Word is ‘Monomaterial’
In both flexible and rigid packaging, the trend is to replace multimaterial laminates, coextrusions and “composites” with single-material structures, usually based on PE or PP. Nonpackaging applications are following suit.
Read MoreRead Next
Beyond Prototypes: 8 Ways the Plastics Industry Is Using 3D Printing
Plastics processors are finding applications for 3D printing around the plant and across the supply chain. Here are 8 examples to look for at NPE2024.
Read MoreMaking the Circular Economy a Reality
Driven by brand owner demands and new worldwide legislation, the entire supply chain is working toward the shift to circularity, with some evidence the circular economy has already begun.
Read More