Large Capacity Recycling Pipe Shredder
ZRS series pipe shredder processes plastic pipes with a diameter of up to seven feet and a length of up to 23 feet.
Zerma’s most recent model of ZRS series pipe shredder can process plastic pipes with a diameter of up to 2.2 meters (7 ft.) and a length of up to 7.0 meters (23 ft.).
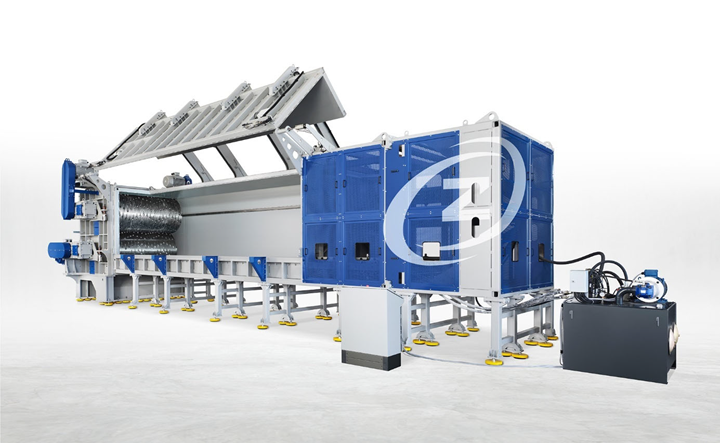
Zerma Pipe Shredder ZRS 2600
Photo Credit: Zerma
Pipes are fed in horizontally via an enclosed feeding trough. To ensure safety, the machine is switched off during loading and the area is secured by a light-grid ensuring the machine cannot be started while people or loading equipment are in the area. As soon as the heavy-duty hydraulically operated cover is closed and locked, the shredding process starts automatically. The pipes are pressed by a strong hydraulic pusher against the two rotors which are arranged vertically and rotate in the same direction. Once the pusher completes the forward stroke, it will retract, the shredder switches off and a new loading cycle can start. The feeding hopper can accept various sizes of pipes, even cascading multiple pipe diameters, optimizing the production process and increasing the overall performance of the pipe shredder.
The rotors have a diameter of 1.3 meters (4.3 ft.) and a width of 2.6 meters (8.5 ft.) and are driven by a powerful gear combination consisting of two gearboxes with 55 kW (73.8 hp) motors each.
The ZRS series pipe shredder can shred pipes with different diameters and wall thicknesses as well as pipes that are nested in one another. The machine has a control panel with separate operator panel that enables the user to monitor and control the operation. This operator panel offers a touchscreen user interface, enabling complete control and monitoring of the process.
Related Content
-
Advanced Recycling: Beyond Pyrolysis
Consumer-product brand owners increasingly see advanced chemical recycling as a necessary complement to mechanical recycling if they are to meet ambitious goals for a circular economy in the next decade. Dozens of technology providers are developing new technologies to overcome the limitations of existing pyrolysis methods and to commercialize various alternative approaches to chemical recycling of plastics.
-
Scaling Up Sustainable Solutions for Fiber Reinforced Composite Materials
Oak Ridge National Laboratory's Sustainable Manufacturing Technologies Group helps industrial partners tackle the sustainability challenges presented by fiber-reinforced composite materials.
-
Recycling: What's Ahead in Advanced Sorting Technology
As the industry tries to ramp up recycling, there are several innovative sorting solutions in the offing—ranging from enhanced optical sorting technologies and chemical tracers to advanced solutions based digital watermarks and artificial intelligence.