Transplants: More Evidence of Processing’s Resurgence in U.S.
Three major firms set up first processing operations in America.
It was the fall of 2013. I was attending the Global Plastics Summit in Chicago, a yearly event cosponsored by the Society of the Plastics Industry and IHS, an international “thought leader” in the area of plastics, chemicals and other industries.
The topic was shale gas, more specifically the opportunity that abundant, inexpensive feedstock materials would present to plastics processors in the U.S. Greg Jozwiak, North America commercial v.p. for Dow Packaging and Specialty Plastics, was one of the speakers that day. Looking into his crystal ball, and referring to PE packaging in particular, he said, “Core growth (due to shale gas) could boost growth by 2.5%, reshoring 1%, substitution (of non-plastics packaging) by 0.75% and export of finished goods another 0.25%,” he explained. “That’s 4.5% of growth, representing 770,000 metric tons/yr.” Perhaps even more intriguing to me, Jozwiak added that Dow customers outside of the U.S. are looking at establishing a manufacturing footprint in America to tap into this potential.
My first thought was “Wow.” Then I wondered, “Maybe a bit optimistic?” Then, as the next speaker was being introduced, I concluded my thought process with “I guess we’ll find out.”
In late April, I found out.
I was part of a tour of worldwide journalists invited by CORE PA Global to visit a group of companies in Pennsylvania. The organization is the centerpiece of a state government initiative to increase the visibility of a 53-county footprint to international and domestic investors and reshoring prospects.
Most of the companies we visited were long established in the region. Companies like sheet processor Sekisui Polymer Innovations, custom molder and foam processor Ralph S. Alberts, rotomolder Playworld, and compounding equipment supplier Technical Process & Engineering. We also heard presentations from the likes of PS foam profile extrusion processor Highwood, and custom molders Viking Plastics and CJ Industries. Central Pennsylvania has been a prime location for plastics processing ever since I got into the industry back in the late 1980, so hearing about the rich histories these companies have in that region was not all that surprising.
What I found even more curious was the arrival of two new transplants to the area: Greiner Packaging Corp., an Austrian packaging powerhouse; and Fuling Plastics USA, a division of Taizhou Fuling Plastics Co. Ltd. of China that makes straws and cutlery for fast-foods. In the June issue of Plastics Technology magazine you can read the full report on these companies in the Close-Up article.
To say these companies selected central Pennsylvania to set up operations because of shale gas would be misleading. (In fact, because of lower oil prices, some fracking operations have reportedly slowed down a bit.) Certainly low energy was a factor, as was proximity to a broad customer base and easy access to transportation services. Not to mention the proximity of Pennsylvania College of Technology in Williamsport, from which Greiner has already recruited a new employee.
I think you need to look at these developments more broadly. In fact, also in the June issue you’ll see yet another “transplant” article on the plans Raumedic of Germany has to build a $27.1 million plant in Mills River, N.C., where it will mold and extrude medical parts. And I’ve heard rumblings of compounding capacity reshoring to the U.S. from Asia.
Manufacturing is returning to the U.S. In plastics, many existing operations are expanding (see On-Site article here) and we get reports of new ones coming on stream on a regular basis. This a pretty good time to be in the business of melting pellets.
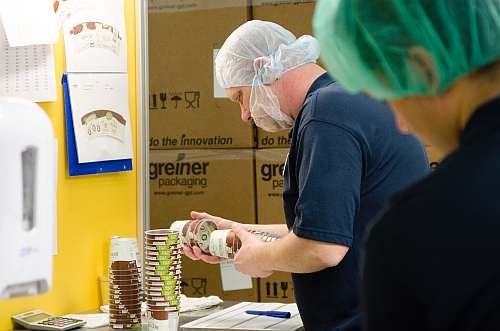
Technician at Greiner inspects combination PP and cardboard cup prior to packaging.
Related Content
How to Effectively Reduce Costs with Smart Auxiliaries Technology
As drying, blending and conveying technologies grow more sophisticated, they offer processors great opportunities to reduce cost through better energy efficiency, smaller equipment footprints, reduced scrap and quicker changeovers. Increased throughput and better utilization of primary processing equipment and manpower are the results.
Read MoreMacro Names Anzini Tech Sales Manages for Southeast
Has worked in technical roles for leading processing companies in his career of 40+ years.
Read MoreRoll Stand is Compact, Flexible
Streamlined stack is joined by high-speed extruder; service cart for maintaining screws, dies and rolls; and other products.
Read MoreHow to Select the Right Cooling Stack for Sheet
First, remember there is no universal cooling-roll stack. And be sure to take into account the specific heat of the polymer you are processing.
Read MoreRead Next
Making the Circular Economy a Reality
Driven by brand owner demands and new worldwide legislation, the entire supply chain is working toward the shift to circularity, with some evidence the circular economy has already begun.
Read MoreSee Recyclers Close the Loop on Trade Show Production Scrap at NPE2024
A collaboration between show organizer PLASTICS, recycler CPR and size reduction experts WEIMA and Conair recovered and recycled all production scrap at NPE2024.
Read More