2021 Hot Shots Finalists
These 10 entrants will be judged by Molding 2021's attendees in Plastics Technology's inaugural injection molded part competition.
Share
Plastics Technology’s Molding 2021 conference (Sept. 21-23; Donald E. Stephens Convention Center; Rosemont, Ill.) will feature the inaugural Hot Shots injection molded part competition. Attendees to Molding and Amerimold will be judging the 10 finalists below and awarding two top prizes—one for Technical Sophistication and one for Achievement in Molding Efficiency and/or Economics.
Criteria for the first prize include use of new technology in molding, molding materials, or tooling; and overcoming challenges in molding—e.g, owing to the material, complexity of part or tool design, and/or very tight tolerances​.
The second prize will consider innovations around part consolidation, thin walling, weight reduction, machine/tool savings, improved quality, increased productivity and application of recycled materials. Check out the entrants below:
Part: Display crowd control barrier
Molder: AAVPD Ltd.
Moldmaker: AAVPD Ltd.
Material: 30% glass-filled nylon 6
Description: This part required the development of a new tooling concept—a “wipe off” layout enabling molding of a long tube with the core lying in the plane of the tool. As the press opens, the core is left between the platens, being held on a carrier system at the top of the tool. The part is then ejected downwards using a stripper plate. For this tool, AAVPD repurposed a hydraulic screw motor to eject the part because its length precluded use of a hydraulic or pneumatic cylinder. AAVPD says the tool layout enabled inclusion of features in the molded part that would have been prohibitively expensive to perform on an extruded tube or created using other secondary operations.

An innovative tool enabled AAVPD’s entry.
Part: “Transport”, structure/skeleton element for ID card printer
Molder: Beacon Manufacturing Group
Moldmaker: Beacon tooling partner in China
Material: PC compound with 10% carbon fiber and 15% Teflon from RTP
Description: This new design consolidated three parts—a base and two vertical sides that were mechanically assembled—into a single molded part, eliminating assembly and multiple molding processes and going from three tools to just one. Quality issues due to misalignment of mechanically assembled parts were eliminated. MoldFlow and warp analysis were used to identify gate type and location, leading to use of a hot manifold with direct sprue drop. Mechanical slides form the entire sidewalls of the part, and these slides pull out with hydraulic cylinders that then push the part off the slides. All critical areas of the mold utilize inserts due to very tight tolerances. If those tolerances are not achieved, the printer won’t function properly and the resolution of the ID badges is compromised.

Beacon’s entry is molded from a PC compound featuring carbon fiber and Teflon.
Part: S- and I-shaped pipes
Molder: Canon Virginia Inc.
Moldmaker: Canon Mold Co. Ltd.
Material: 33% glass-filled Nylon 66
The undercut of the hollow section makes these parts very difficult to mold by normal injection molding. Parts are molded from a 1 x 4 family mold, making 2 parts. Parts are assembled in the mold via over molding in one process cycle. Canon’s MultiMold System makes this possible to perform on a low-tonnage press with a single injection unit. Utilizing cooling time as production time and eliminating changeover downtime leads to a huge increase in productivity. In addition only needing one small machine to perform all operations the technology eliminates excess inventory and secondary operations.

Inmold assembly powered by Canon’s Multi Mold system allowed the creation of these hollow multimaterial pipes via injection molding.
Part: Airplane Name Badge
Molder: Fortify
Moldmaker: Fortify
Material(s): Resmart Ultra ABS, Conventus Polymers DuraTemp1000RP PEI, 30% glass-filled PP
Description: The tool designed for this part utilizes a new 3D printing technology from Fortify. The Flux One 3D printer allows for fibers to be incorporated into the 3D printing resin. These fibers are then aligned in the Z-axis, resulting in a reinforced 3D printed mold with heightened strength, stiffness, and heat deflection.
A swappable insert was used to quickly modify the logo design, eliminating the need for multiple molds while allowing for customization. Two different textures—one on the front, and one on the back—are included. Printing these textures added no extra cost or time, whereas a traditional aluminum tool would have required additional EDM finishing.
The whole process of printing the mold, post processing, and running the tool took only three days, and the material cost of printing the tool was just $365, versus thousands of dollars for a steel tool. The tools were printed with ejection pin holes, eliminating the need for any machining, and the printing took less than 16 hours, compared to a typical lead time from 4-8 weeks for a machined steel mold.
A total of 350 shots were produced from this tool, and more than 100 of those parts were molded from a recycled glass-filled material, highlighting the ability to use this tools with sustainable plastics. Another 50 were molded from Conventus unfilled PEI, and the remaining 200 were an unfilled ABS from Resmart.

Fortify’s Hot Shots entry of airplane badges applied the company’s fiber-oriented 3D-printed tool technology.
Part: Medical diagnostic array
Molder: U.S. based medical molder
Moldmaker: Magor Mold
Material(s): clear and colored Sabic Lexan PC
Description: The part has a thickness of just 0.5mm with very thin webs. The PC must fill a 0.5 mm wall that immediately after the gate becomes even thinner, getting down to 0.3 mm at its thinnest between two holes. The challenge is to keep the melt flow moving while also maintaining enough pressure to get to the end of the part.
Part flatness and hole size are critical to function and scaling up production using standard technology could cause part quality issues.
This array was originally molded in three 2-cavity hot runner molds with a +5% scrap rate. Transitioning to Husky’s UltraShot enabled the molder to scale up to a single 8-cavity mold and provided major improvements in cavity-to-cavity part quality, consistency and repeatability, including achieving flat parts with flush gates. Scrap was reduced to virtually 0%, while piece/part cost savings dropped from $0.019/piece to $0.005. That’s based on reduced capital equipment requirements, including dropping to one cell from four.
With traditional injection molding, 2-cavity tools would require elevated temperatures in the barrel, manifold, and tips, and despite those high temperatures, requisite pressure would be over 40,000 psi. This requires very high melt (360-380°C) and mold temperatures (100°C).

The medical diagnostic array was shifted to a higher production 8-cavity tool thanks to Husky’s UltraShot technology.
Part: Automotive instrument panel component
Molder: AGS Technology
Moldmaker: confidential
Material(s): PC/ABS up to 100% regrind
Description: AGS Technology specializes in molding with recycled resin, which can cause process and finished part quality challenges due to viscosity and melt density differences in the material.
AGS is now applying iMFLUX technology to process its formulated regrind material, which conforms to OEM specifications. With a set velocity profile and transfer position, conventional molding methods wouldn’t accommodate variations seen with recycled material.
iMFLUX’s technology utilizes low constant pressure to absorb viscosity changes and allow the part to profile the velocity of the machine, improving quality and repeatability. Processing at low constant pressure with iMFLUX allows a reduction in machine tonnage required.
The original 2-cavity mold for this part required a 720-ton injection molding machine. With iMFLUX, AGS utilizes the same mold, with no modifications, in a 500-ton press. Lower tonnage and injection pressure means less wear and tear on the machine, mold, and even more importantly, lower energy usage. The part is now molded in a 51 sec cycle vs. the original 55 sec. There has also been a large reduction in scrap. Conventionally this part could produce as much as 20% scrap, but with iMFLUX, AGS has reduced scrap to less than 3%.

AGS used iMFLUX technology to mold this instrument panel component for automotive from up to 100% regrind.
Part: Ball joint rod for Swiffer Mop
Molder: Hayco
Moldmaker: iMFLUX
Material(s): Cosmoplene AV161 PP with Polyone Hayco Green COPP (Liquid) .7% Letdown Ratio
Description: Originally molded in China in a 500-ton press and an 8-cavity tool, this part is now molded in the Dominican Republic in a 400-ton press with 12 cavities in a faster cycle time due to the iMFLUX process and tool design. The parts are placed in a cooling fixture and then an automated process inserts a plastic clip into the ball joint rod.
The Swiffer has more than 50 injection molded parts, all manufactured by Hayco. Until recently, the product was only produced in China. Hayco & P&G wanted to near-shore this operation to the Dominican Republic, however, the capital investment needed made this challenging, especially with the throughput of the existing molds. Through partnership with iMFLUX, using the low constant pressure Green Curve, as well as a specialized mold design, Hayco was able to successfully near shore the project.
Originally, this part was made in a 500-ton Battenfeld machine from an 8-cavity tool in a 52-sec cycle. By utilizing iMFLUX’s processing software and mold design/build, this part now runs in a 400-ton Battenfeld (set to 350 tons), from a 12-cavity tool in a 39-sec cycle. Through the combination of 50% up-cavitation and a 24% cycle-time reduction, Hayco realized over a 90% throughput improvement on this part.

iMFLUX technology’s economic benefits allowed this Swiffer mop component to be near shored from China.
Part: DREAM flying disc
Molder: M.R. Mold & Engineering Corp.
Moldmaker: M.R. Mold & Engineering Corp.
Material(s): Dow SILASTIC Low Temperature Cure 9400 Series Liquid Silicone Rubber & Zytel 101L nylon.
Description: An automated cell overmolds a red pigmented Dow Silastics LSR onto a white low-melt plastic. A 50-duromoter Dow Silastics LTC 9400 SLR was overmolded on the the flying disc at 250F, with a sub 45-second curing time. Normally, overmolding LSR onto a low melting point plastics and other thermally sensitive components, like electronics, hasn’t been possible because of the high curing temperature required, relegating overmolding to substrates like PC.
M.R. Mold built a single cavity mold for the insert, which was molded from nylon in a single-cavity tool with M.R. Mold’s 1-drop cold runner and universal base. Normally the mold temperature for a silicone tool is around 325 to 350F, but the flying disc mold ran at 260F with a 50-sec cycle.

Low-melt-temperature LSR allowed M.R. Mold to create this two-component flying disc with a lower melt temperature substrate.
Part: Showcase component
Molder: Matrix Tool Inc.
Moldmaker: Matrix Tool Inc.
Material(s): Sumitomo Sumika Super LCP
Description: Molded from Sumitomo’s Sumika Super LCP resin in a Sodick Plustech two-stage Hi-Response injection molding machine from Sodick, the showcase part has a wall thickness of just .0048 inch, and is filled in 0.16 second.
Matrix designed this tiny LCP part with intricate geometry to showcase the advantages of small tools and fast clamping presses. With this setup, the company says it can out produce larger machines running high cavity tools. This 4-cavity cold runner tool running at 2.9 seconds on a two-stage Hi-Response Sodick press can easily outproduce similar parts running in a 16-cavity hot runner tool.
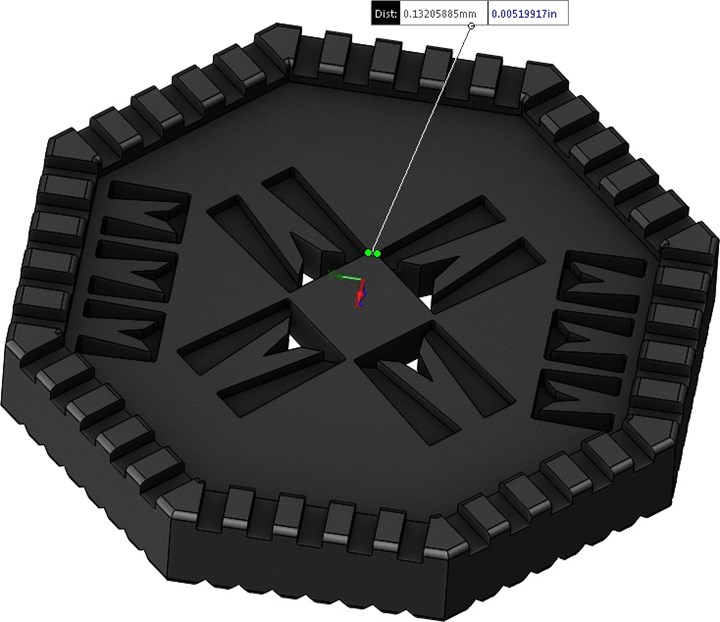
Created to showcase the company’s microtooling capabilities, Matrix Tool created this showcase part with tiny, precise features.
Part: Screen Filter
Molder: Toth Mold/Die Inc.
Moldmaker: Toth Mold/Die Inc.
Material(s): 7.5% glass-filled TPU
Description: Injection molded, very complex part that is laser welded to a injection molded frame and used in oil drilling fields. The part’s openings, which are measured in microns, must be flash free. The component is molded in a 15-sec cycle, from a 2-cavity mold that has interchangeable inserts for different micron meshes. The part has 2880 openings, with the same number of knit lines and ribs. The openings measure .0022 in. (56 microns), with .007-in. thick ribs.

Toth’s entrant features 2880 openings measuring .0022 in. (56 microns) wide and no flash.
Related Content
Optimizing Pack & Hold Times for Hot-Runner & Valve-Gated Molds
Using scientific procedures will help you put an end to all that time-consuming trial and error. Part 1 of 2.
Read MoreA Systematic Approach to Process Development
The path to a no-baby-sitting injection molding process is paved with data and can be found by following certain steps.
Read MoreHow to Select the Right Tool Steel for Mold Cavities
With cavity steel or alloy selection there are many variables that can dictate the best option.
Read MoreProcess Monitoring or Production Monitoring—Why Not Both?
Molders looking to both monitor an injection molding process effectively and manage production can definitely do both with tools available today, but the question is how best to tackle these twin challenges.
Read MoreRead Next
Tiny Part Showcases Big Molding, Moldmaking Capabilities
Grab a magnifying glass and check out this entrant in Molding 2021’s Hot Shots injection molded part competition.
Read MoreMaking the Circular Economy a Reality
Driven by brand owner demands and new worldwide legislation, the entire supply chain is working toward the shift to circularity, with some evidence the circular economy has already begun.
Read More