Matrix Tool Sweeps 'Hot Shots' Competition
Working together with injection machine builder Sodick Plustech, this Pennsylvania molder and moldmaker won both prizes in Plastics Technology’s first-ever Hot Shots injection molded parts competition, held at Molding 2021.
Share
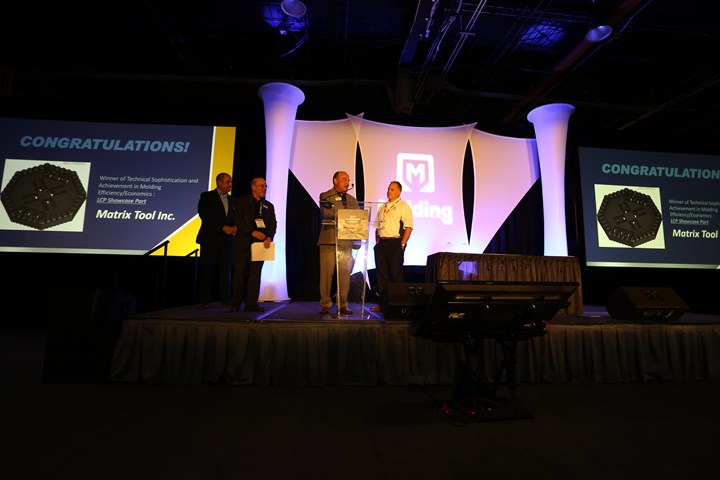
Sodick Plustech’s national sales manager Len Hampton (at podium) and Matrix Tool’s general manager Dave Moyak accept both Hot Shots awards at Molding 2021.
When injection molding machine supplier Sodick Plustech and molder and moldmaker Matrix Tool, Fairview, Pa., first conceived of a showcase liquid-crystal polymer (LCP) part with microfeatures, it was intended to drive traffic at a trade show and promote business. Specifically it would highlight Matrix’s special moldmaking capabilities and philosophy, in partnership with the precise process control made possible by Sodick Plustech’s two-stage machines.
Knowing how difficult it can be to get a customer to approve showing a commercial part at a show was initially what set Matrix (matrixtoolinc.com) on this path, which would eventually lead to an award-winning component, which attendees at Plastics Technology’s Molding 2021 Conference and MoldMaking Technology’s Amerimold trade show voted the winner of both the Hot Shots awards—for Technical Sophistication and for Achievement in Molding Efficiency and/or Economics prizes.
“We decided we would develop our own part,” says Matrix’s Tom Moyak, director of business and engineering development. “It’s not a commercial product; it’s just something we did for a trade show, but we wanted to make something that you couldn’t mold with normal injection molding machines in typical materials in a typical mold.”
The result was a part that weighs 0.106 g—requiring just 5 pellets of LCP (SumikaSuper E6807T from Sumitomo Chemical). Featuring more than 60 knife-edge tooling features, each opening on the part is formed by mating cores from both mold halves, with numerous features as thin as 0.0048 in., or slightly thicker than a human hair.
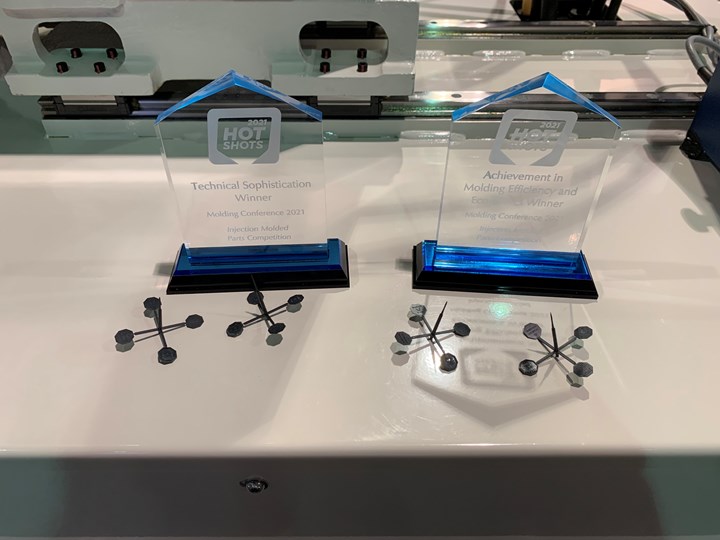
Molding 2021 and Amerimold attendees voted the Matrix Tool parts as the winner of both the Technical Sophistication and Achievement in Molding Efficiency and Economics prizes.
The parts are molded in a four-cavity cold-runner tool designed and built by Matrix. Measuring just 4.5 × 5.0 × 5.9 in., the mold has both front- and back-half ejection and utilizes multi-directional alignment interlocks and linear ball-bearing guided ejection. In addition to ensuring that both mold halves meet with precision alignment, the design allows Matrix to eliminate traditional leader pins. Matrix says this results in more efficient, balanced cooling and a much smaller overall footprint.
To produce the parts, Matrix runs this mold on Sodick Plustech’s 20-ton, two-stage, Hi-Response micro injection molding machines. The tool filled in 0.16 sec, and Matrix says it can “easily” out-produce a 16-cavity tool running similar parts in a conventional injection machine. The tool was running at the Sodick Plustech exhibit during the three-day 2021 Molding Conference, which was held Sept. 21-23 at the Donald E. Stephens Convention Center in Rosemont, Ill.
10 Finalists
The inaugural Hot Shots parts competition set out to recognize an injection molded component for two criteria, as voted by attendees at Molding 2021 and Amerimold 2021. Technical Sophistication was judged on the basis of using new molding, materials, or tooling technology; as well as overcoming molding challenges related to the material, part complexity, tool design, and/or very tight tolerances. Achievement in Molding Efficiency and/or Economics considered parts consolidation, thin walling, weight reduction, machine/tool savings, improved quality, increased productivity and application of recycled materials.
The 10 finalists came from three countries (U.S., UK and Dominican Republic) and seven states, serving markets as diverse as industrial, consumer goods, automotive, medical, aerospace and electronics. They were molded in TPU, nylon, LSR, PEI, PP, PC/ABS and PC, among other resins.
Though surprised by Matrix Tool’s Hot Shots sweep, Sodick Plustech national sales manager Len Hampton knew beforehand that the LCP part was a winner. “When you have a customer holding up the part and a magnifying loop, putting it to the light, then they really see that it uses 0.0400-in. core pins,” Hampton says. “That really sets both the tooling and the machine apart. Other people from other booths see what’s happening, and next thing you know, we’re four deep with loops out and people holding parts up to the lights in the ceiling.”
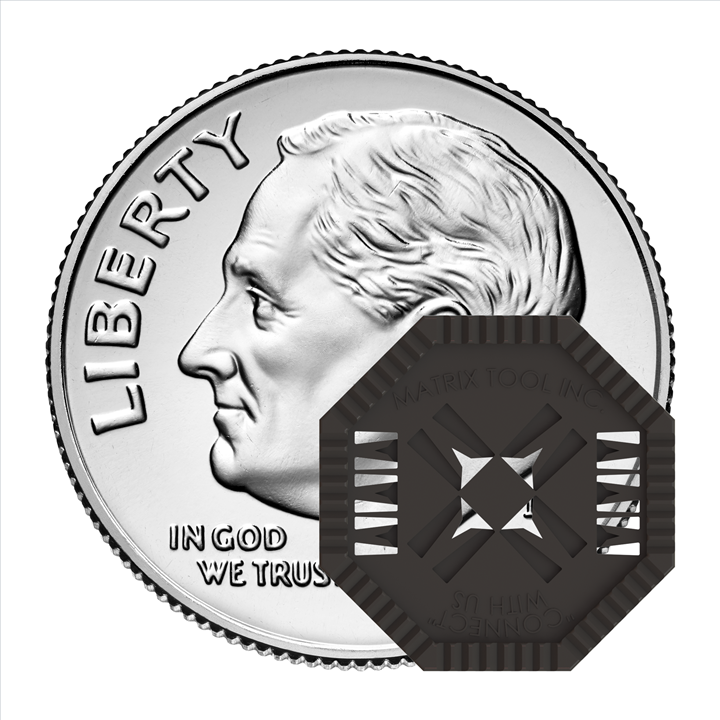
Microfeatures molded precisely from LCP made Matrix’s Hot Shots entry stand out to attendees judges at Molding 2021.
Related Content
System Offers 'Lights Out' Mold-Channel Cleaning & Diagnostics
New system automatically cleans mold-cooling lines—including conformal channels—removing rust and calcium, among other deposits, while simultaneously testing for leaks, measuring flow rate and applying rust inhibitor.
Read MoreImpacts of Auto’s Switch to Sustainability
Of all the trends you can see at NPE2024, this one is BIG. Not only is the auto industry transitioning to electrification but there are concerted efforts to modify the materials used, especially polymers, for interior applications.
Read MoreNew Blown-Film Cooling Technologies Set to Debut at NPE2024
Cooling specialist Addex to roll out new auto-profiling air ring for rotating dies, and new single-plenum air ring.
Read MoreAutomotive Awards Highlight ‘Firsts,’ Emerging Technologies
Annual SPE event recognizes sustainability as a major theme.
Read MoreRead Next
2021 Hot Shots Finalists
These 10 entrants will be judged by Molding 2021's attendees in Plastics Technology's inaugural injection molded part competition.
Read MoreMatrix Tool Wins Inaugural Hot Shots Competition
The Pennsylvania-based injection molder and moldmaker applied its tooling know how and Sodick injection technology to take home both Hot Shots prizes.
Read MoreLead the Conversation, Change the Conversation
Coverage of single-use plastics can be both misleading and demoralizing. Here are 10 tips for changing the perception of the plastics industry at your company and in your community.
Read More