Rotating Tubing Dies Increase Wall Strength
New design of rotary inline or crosshead dies feature speeds to 1000 rpm.
Guill Tool has developed a new design for its high-production rotary models, both inline and crosshead style. The die offers a two-time increase in speed, with models running to 1000 rpm depending on the application. According to Guill, rotating the tooling in relation to the material flow increases the wall strength of an extrusion, thereby allowing a thinner wall with less material and the corresponding cost savings for the user. Typical applications for rotary heads include medical and multi-lumen tubing plus various high-end extrusions with interlocking layer or multiple striping requirements.
Features offered on these new rotating extrusion dies include counter-rotating tip and die, co-rotating tip and die, rotating die with conventional tip, rotating tip with conventional die, crosshead or inline, multi-layer, striping, certain profiles and optional quick-change cartridges that minimize cleaning downtime.
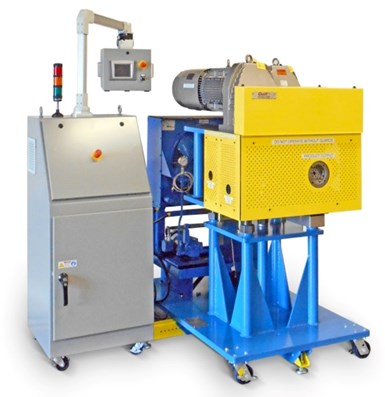
Guill maintains that using rotary dies also lets extrusion processors cut costs by making secondary processes unnecessary, improves the cosmetics of the end product by eliminating weld or parting lines, and reduces if not eliminates ovality.
Guill Tool offers its new high-speed rotary models as turnkey packages, complete with die cart, tools and all accessories for installation and maintenance.
Related Content
-
Part 2 Medical Tubing: Use Simulation to Troubleshoot, Optimize Processing & Dies
Simulation can determine whether a die has regions of low shear rate and shear stress on the metal surface where the polymer would ultimately degrade, and can help processors design dies better suited for their projects.
-
Tight-Tolerance Molder Dips Toe in Extrusion Waters
Midwest Precision Molding brings extrusion capacity in-house to assist a customer that was having a sourcing issue with its existing overseas suppliers.
-
How to Effectively Reduce Costs with Smart Auxiliaries Technology
As drying, blending and conveying technologies grow more sophisticated, they offer processors great opportunities to reduce cost through better energy efficiency, smaller equipment footprints, reduced scrap and quicker changeovers. Increased throughput and better utilization of primary processing equipment and manpower are the results.