Additive Fusion Technology Optimizes Composite Structures for Demanding Applications
9T Labs continues to enhance the efficiency of its technology, which produces composite parts with intentionally oriented fibers.
Additive Fusion Technology combines high-resolution material deposition with compression molding to create composite materials that make the best use of continuous carbon fibers by placing them exactly where they are needed. The technology has been pioneered by Swiss-based supplier 9T Labs, which was founded in 2018.
9T Labs’ process optimizes the layup for a given application, both in terms of product performance and build efficiency. The process begins with a customer supplying a desired geometry and loading requirements. 9T Labs uses its own software, called fibrify, to analyze the model. Using finite element analysis, fibrify determines the areas of stress concentration. The design is optimized both for handling the strength requirements and for manufacturability.
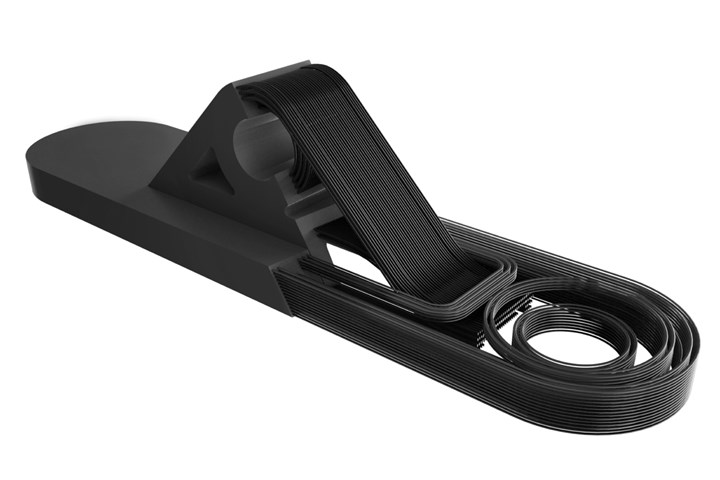
Build design cutaway showing the strategic placement of continuous fibers. Photo Credits: 9T Labs
The Build Module uses the final design to create a preform, with continuous fibers precisely placed exactly where they need to be. Material is deposited through two guides that place fiber-reinforced composite tape next to thermoplastic-only tape. By laying down the material in this intentional manner, the process leads to a product that is strongest just where it needs to be and nowhere else, using the material efficiently and limiting build time. Volumes where the peak load is lower are filled with plastic alone or plastic reinforced with short fibers.
Finally, the part is finished in the Fusion Module, which compression molds the final shape of the part. The printed preforms are flat, but can be reshaped while being consolidated in the Fusion Module, enabling the production of much more complex parts.
Optimizing the Build Path: It’s About the Journey
Recently, 9T Labs added several improvements to its Build Module, increasing part output to 10 times the rate of the previous generation. New actuators, additional sensors and advanced firmware controls are expected to enable greater repeatability and throughput. The new deposition head is modular, facilitating future upgrades, and new bed-leveling and tape-cutting components are expected to extend wear life.
But the process improvements go beyond hardware, as Yannick Willemin, 9T Labs’s director of business development describes. “There is a lot of software optimization to consider, it’s kind of a navigation system to shorten the total movements required to deposit the same amount of material. If you can win a second here, a second there, it adds up to minutes or more,” Willemin says.
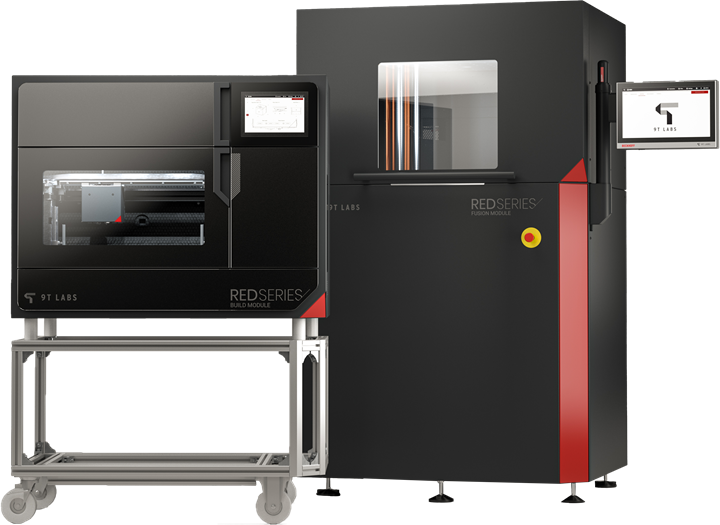
9T Labs Red Series Build Module (left) and Fusion Module (right).
After evaluating hundreds of applications, 9T Labs developed an understanding of ways to reduce the paths taken by the Build Module, and also reducing maintenance time by optimizing cutting points. Whenever a cut is made, the build module needs to be stopped, the cutting initiated and then the fiber re-anchored so the lay up can continue. “It is not only the physical optimizations like better hardware and so on, it is optimizing the software code,” Willemin says.
High Durability for Demanding Applications
Materials used by 9T Labs include PEKK and PA12, with other thermoplastics to follow, combined with carbon, glass or basalt fibers. 9T Labs has taken an open approach to materials, enabling customers to choose without being bound to an exclusive supplier.
The technology for producing lightweight, strong and durable parts has found applications in aerospace and in ground mobility. Because the process does involve a metal mold, it is more suited for serial production than a one-off situation. As a replacement for aluminum parts, such as motorcycle rocker arms, the composite parts produced can be 30-40% lighter. As a replacement for traditionally manufactured composites, benefits come in terms of cost and waste reduction because the preform is near-end shape. This contrasts with subtractive machining of composite parts, which may waste half or more of the starting material.
Strength and material efficiency are not the only motivations for using additive fusion. Anisotropic fiber orientation can also provide flexibility in textures, imbuing high-end products with aesthetic differentiation. In 2022, Oris chose the platform for producing the outer casing of 1,000 limited edition watches. Fibers were laid in specific directions to give the product’s surface an ordered pattern, distinguishing it from the familiar rough pattern associated with composites with random fiber orientation. A higher volume watch, using the same technology, was launched in 2023.
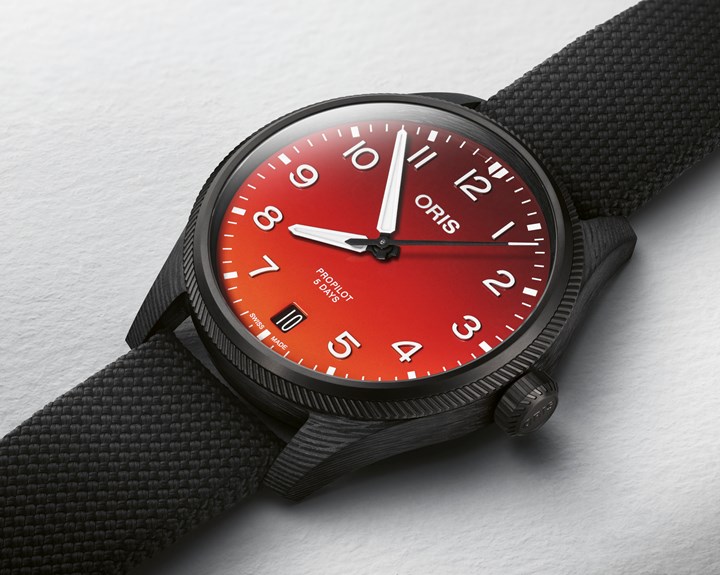
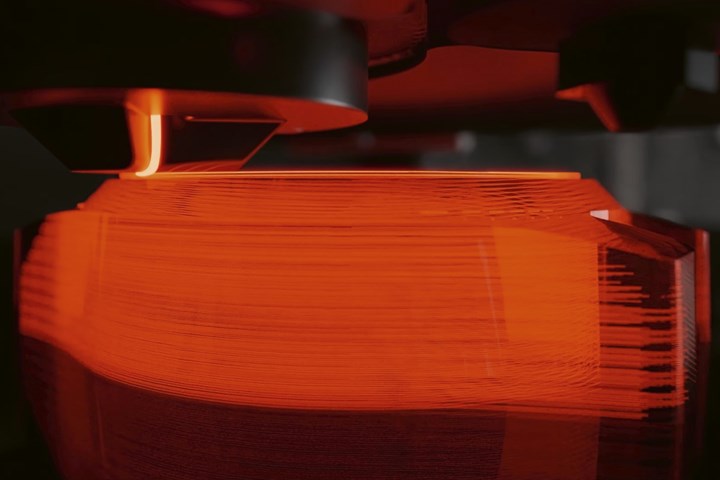
9T Labs operates the Build and Fusion modules for its customers at its own facilities, located in Zurich, Switzerland, and Lowell, Massachusetts.
Related Content
Automotive Awards Highlight ‘Firsts,’ Emerging Technologies
Annual SPE event recognizes sustainability as a major theme.
Read MoreSystem Offers 'Lights Out' Mold-Channel Cleaning & Diagnostics
New system automatically cleans mold-cooling lines—including conformal channels—removing rust and calcium, among other deposits, while simultaneously testing for leaks, measuring flow rate and applying rust inhibitor.
Read MoreScaling Up Sustainable Solutions for Fiber Reinforced Composite Materials
Oak Ridge National Laboratory's Sustainable Manufacturing Technologies Group helps industrial partners tackle the sustainability challenges presented by fiber-reinforced composite materials.
Read MoreNew Facility Refreshes Post-Consumer PP by Washing Out Additives, Contaminants
PureCycle prepares to scale up its novel solvent recycling approach as new facility nears completion.
Read MoreRead Next
Recycling Partners Collaborate to Eliminate Production Scrap Waste at NPE2024
A collaboration between show organizer PLASTICS, recycler CPR and size reduction experts WEIMA and Conair will seek to recover and recycle 100% of the parts produced at the show.
Read MorePeople 4.0 – How to Get Buy-In from Your Staff for Industry 4.0 Systems
Implementing a production monitoring system as the foundation of a ‘smart factory’ is about integrating people with new technology as much as it is about integrating machines and computers. Here are tips from a company that has gone through the process.
Read More