OPINION: Stepping into the Minefield – Again
A major packaging producer defends “mono-material” claims as being “functionally” accurate and true “in spirit” when minute amounts of other materials do not affect recyclability.
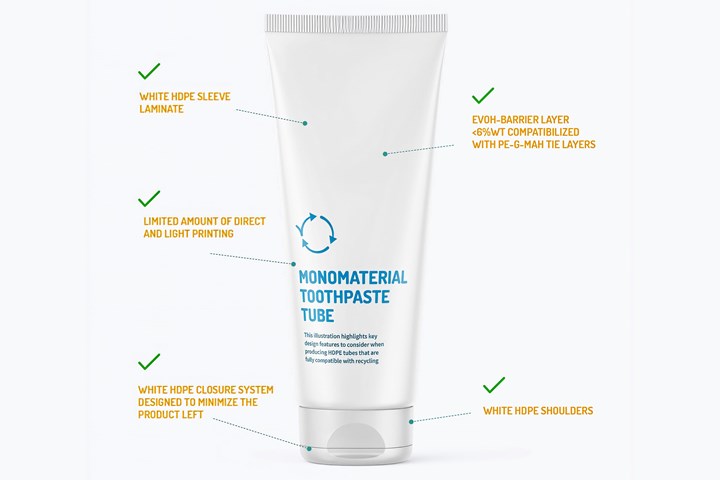
“Functionally mono-material … as far as recycling is concerned,” Hoffmann Neopac’s new Polyfoil EcoPro tube is certified by RecyClass as fully recyclable in the HDPE stream. (Photo: RecyClass Designbook)
Last month, I wrote an opinion piece titled, “Recycling Terminology Can Be a Minefield, So We Should Tread Lightly.” My essay was apparently too heavy-footed, according to a major global packaging firm – whose rebuttal you can read in full below. But before we get to that, a few points need clarification:
I specifically questioned the use of terms such as “mono-material” and “all-polyolefin” to describe packaging that is, in absolute fact, neither of those things, but whose level of “other” materials is so minute (less than 3%) as to allow the packaging to be recycled in PE or PP streams as if those claims were true, as certified by appropriate authorities.
As you’ll see below, Hoffmann Neopac said my nitpicking overlooked critical facts and was “unworkably absolutist and anathema to progress” at a time when such advances in recyclability are “desperately needed”and “should be embraced rather than purity tested.” I plead innocent to both charges. If you re-read my essay, you’ll see none of the critical facts cited by Neopac below are omitted, and my cautions about use of potentially misleading language are presented “without diminishing the importance of this evolution in packaging toward greater recyclability.”
Neopac states, “While we agree that recycling terminology can indeed be a minefield, it is equally important to consider the spirit of these terms.” Without disputing that Neopac’s newest tube packaging is “functionally mono-material … as far as recyclability is concerned,” and that it is certified as such by “the most influential authorities,” my point is not how people associated with the packaging and plastics industry, such as myself, view the matter, but how it appears to the rest of society, which has been bombarded with accusations that industry has misrepresented and exaggerated its efforts and achievements in plastics recycling.
I’m not the “language police,” but some government regulators are happy to play that role. Consider the dim view they have taken of industry’s “reasonable” and presumably “good-faith” assertions that certain plastics packaging is “recyclable” or “compostable” – all true in theory, but not necessarily in practice.
Hoffmann Neopac is based in Switzerland; perhaps Europeans are more reasonable than Americans and less prone to a reflexive mistrust of industry whenever environmental, health or safety concerns are raised.
Perhaps I’m making too much of all this – perhaps the American public, environmental activists, and legislators and regulators at all levels from city to Federal will appreciate industry’s advances in recyclability; will recognize the “spirit” of its recycling-related terminology, which will be “embraced rather than purity tested”; and will accept the recyclability certifications of industry groups as being “the most influential authorities” in the public interest. Or not.
Anyway, you be the judge. Here is Hoffmann Neopac’s reply to my article, in full:
Neopac Article for Plastics Technology
In a May 22 piece on Plastics Technology’s website, titled Recycling Terminology Can Be a Minefield, So We Should Tread Lightly, Executive Editor Matthew Naitove expressed his viewpoint that the terminology used in materials science and packaging must be carefully selected, particularly as it pertains to sustainability and recyclability. As an example, he pointed to Neopac’s recently introduced Polyfoil® EcoPro Tube, which is described by us at Neopac as “mono-material” despite containing a minute amount of foreign materials that – and this is crucial – do not disrupt the tube’s ability to be processed in its designated recycling stream.
We always appreciate dialogue, and commend Mr. Naitove for tackling such a complex subject. However, we feel his article dismisses progress for the sake of perfection.
The article’s criticism of Polyfoil EcoPro as not being truly "mono-material" due to its thin EVOH barrier layers, in our view, overlooks a critical fact: the product is more than 97% HDPE, and therefore fully recyclable in the HDPE stream, which is, in essence, what "mono-material" implies in this context. In other words, as far as recyclability is concerned, the tube is functionally mono-material.
We understand Mr. Naitove’s concern, but find his argument unworkably absolutist and anathema to progress at a time when such advancements like new recyclable barrier technologies are desperately needed to combat climate change. The term "mono-material" is not intended to greenwash, but rather facilitates the understanding of the product's recyclability. It conveys that the product can be processed in a single recycling stream, unlike composite materials that must be separated before recycling.
While we agree that recycling terminology can indeed be a minefield, it is equally important to consider the spirit of these terms. Sustainability is a journey, and every incremental innovation that brings us closer to a more sustainable future should, we believe, be embraced rather than purity tested for, per Mr. Naitove’s words, “verbal potholes.”
Another reason for not narrowing down the definition of "mono-material" is that even adding coloration for white or any other masterbatch color, or using direct printing, introduces foreign material to tubes made of PE or PP. This is why the guidelines for determining what qualifies as "mono-material” design and recyclability are established by the most influential authorities: the Plastic Recyclers in Europe, through RecyClass, and the Association of Plastic Recyclers.
Our goal is increased sustainability and, to that end, Polyfoil EcoPro tubes have managed to significantly cut down on CO2 footprint and material usage while maintaining enhanced product protection and using post-consumer recycled HDPE, which complies with the draft paper of the upcoming revision of EU legislation on Packaging and Packaging Waste.
In this context, terms such as “mono-material” and “all-polyolefin” by packaging manufacturers are neither imprudent nor misleading. These terms are used to highlight the tangible advances toward a more recyclable product line, even if they are not comprised 100% of a single material.
Here are the sustainability facts surrounding Polyfoil EcoPro:
- Traditional Polyfoil® Tubes consist of multi-materials with PE/Aluminium/PE and PP closures, whereas the innovative Polyfoil® EcoPro contains PE/EVOH/rPE with PE or rPE closures with less than 5% foreign (but compatible) materials such as EVOH, adhesives and colors/printing.
- 30% weight reduced compared to standard Polyfoil Tubes due to reduced wall thickness
- Reduced CO2 footprint of 57% compared to standard Polyfoil Tubes (Ø30x110 mm)
- Our Polyfoil® MMB tubes received full compatibility product approval by RecyClass, Grade A and passed APR’s HDPE Critical Guidance requirements. The only change with EcoPro is the overextrusion of the laminate – which now contains 70% rHDPE instead of virgin HDPE compared to the tested Polyfoil® MMB tubes.
- The tube utilizes standard PU laminating adhesives approved by RecyClass Flexible Technical Committee.
- Neopac’s Polyfoil® Mono-Material-Barrier Tubes have been designated “mono-material” by RecyClass, per page 35 of this document.
In sum, we must strike a balance in our language between the ideal and the practical, and understand that progress in sustainability may often come in increments rather than leaps. As we move toward greater recyclability, let's also evolve our perspective, focusing on the spirit of progress rather than narrow terminological definitions.
Related Content
How to Optimize Injection Molding of PHA and PHA/PLA Blends
Here are processing guidelines aimed at both getting the PHA resin into the process without degrading it, and reducing residence time at melt temperatures.
Read MoreA Recycling Plant, Renewed
Reinvention is essential at Capital Polymers, a toll recycler that has completely transformed its operation in a short period of time.
Read MoreFilm Extrusion: Boost Mechanical Properties and Rate of Composting by Blending Amorphous PHA into PLA
A unique amorphous PHA has been shown to enhance the mechanical performance and accelerate the biodegradation of other compostable polymers PLA in blown film.
Read MoreBreaking News From NPE2024
Here is a firsthand report of news in injection molding, extrusion, blow molding and recycling not previously covered.
Read MoreRead Next
Recycling Terminology Can Be a Minefield, So We Should Tread Lightly
Loose propagation of terms like “recyclable” and “compostable” has already brought down government regulations on labeling. The plastics and packaging industries should take that to heart with other recycle-related language. Like “monomaterial” for example.
Read MoreSee Recyclers Close the Loop on Trade Show Production Scrap at NPE2024
A collaboration between show organizer PLASTICS, recycler CPR and size reduction experts WEIMA and Conair recovered and recycled all production scrap at NPE2024.
Read More