Revisited: A Processor's Checklist for When Business Is Slow
Business slowdowns may provide you with more time for introspection. If you want to take a deeper dive into your operation, here are some things to consider.
In this space in June, I ventured that because business had slowed, processors could use the extra time to dig deep into their operations and reevaluate what they can do to improve it. My point was that when business is running on all cylinders, many manufacturers tend to rightfully focus on getting quality product out the door to their customers on time, and push aside bigger-picture items.
So back in June, I talked about things such as reengaging with the outside world, revisiting your strategic plan, investigating new technologies, investigating training and do some housekeeping. Since writing that, I have done some reengaging myself, visiting a few processing plants and talking to numerous others, and thought I’d add to that list:
Develop a Sustainability Plan: Disabuse yourself of the notion that the only processing companies that need to worry about sustainability are those that make products for the single-serve packaging market. Brand owners/OEMs and big-box retailers are looking to do business with companies across the supply chain that are committed to sustainability … not just through words but actions. We report on one such company in this month’s Processor’s Edge article on p. 48. In the months ahead, we’ll continue to shine a light on companies that have put sustainability plans in action.
I for one was surprised to learn from my various contacts how many processors are still selling production scrap to recyclers rather than reutilizing it themselves. I recognize that for some applications reintroducing scrap to the process is either impractical or impermissible. But if it’s neither of those, that might be a place to start a sustainability initiative.
“All this data is great, but someone needs to tell me how it’s going to make me more money.”
Simplify: This piece of unsolicited advice applies primarily to flexible film and sheet producers. One thing I have noticed over the past few years — mostly from press materials I receive regularly from suppliers — is the move away from complicated, multimaterial structures that are not recycling friendly to single-material solutions, usually based on PE. Is your product overengineered for the application? Are you making it in the same way you have been for the last 20 year because, well, you’re still using the same equipment you had 20 years ago? Have you looked into technologies like orientation to perhaps give you a wee bit more barrier? When was the last time you sat down with your material supplier to investigate whether you can fortify your base material with additives that can perhaps approximate the properties of your structure without adding complexity.
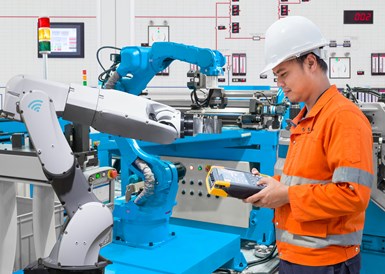
Photo Credit: Getty Images
Think Like a Realtor: You know what that say about real estate: the three most important things about it are location, location and location. In processing, it’s automate, automate, automate. Many molders have not embraced even robot technology to the extent they should have. Many molders still are of the mindset that they are “too small” to appreciate its value. Maybe that mindset needs to be changed. My advice is to bring in an automation specialist to your plant — either a supplier or a trusted consultant — and have he or she evaluate what steps in your process are ripe for automation.
And this advice isn’t just for molders ... and “automation” isn’t just about robots. In all processing, time is money, and anything that can facilitate product changeovers should be explored. You might be surprised at the payback.
Investigate Big Data: There have been a number of obstacles that have stood in the way of widespread acceptance of Industry 4.0. Network security has been one. One molder I have a tremendous amount of respect for had a more practical concern, telling me, “All this data is great, but someone needs to tell me how it’s going to make me more money.”
Related Content
Be Our Guest
The Plastics Technology Expo (PTXPO) returns March 18-20 at the Donald E. Stephens Convention Center in Rosemont, Illinois, with elements old and new.
Read MoreBidding So Long — But Not Goodbye — To Plastics Icon Matt Naitove
After 51 years of contributing content, plastics industry stalwart will take a step back.
Read MoreChanges Afoot for Plastics Technology
Jeff Sloan named brand manager of PT. Tony Deligio to head PT’s editorial efforts beginning in September.
Read MoreNot Your Grandpa’s Plastics Processing Operation
New materials and machinery offer processors the means to run their businesses more efficiently and more inline with the circular economy. But you have to say yes.
Read MoreRead Next
Making the Circular Economy a Reality
Driven by brand owner demands and new worldwide legislation, the entire supply chain is working toward the shift to circularity, with some evidence the circular economy has already begun.
Read MoreBeyond Prototypes: 8 Ways the Plastics Industry Is Using 3D Printing
Plastics processors are finding applications for 3D printing around the plant and across the supply chain. Here are 8 examples to look for at NPE2024.
Read MoreLead the Conversation, Change the Conversation
Coverage of single-use plastics can be both misleading and demoralizing. Here are 10 tips for changing the perception of the plastics industry at your company and in your community.
Read More