Thermoformer Maximizes Productivity with 3D Printing
Productive Plastics has created an extensive collection of 3D printed manufacturing aids that sharply reduce lead times.
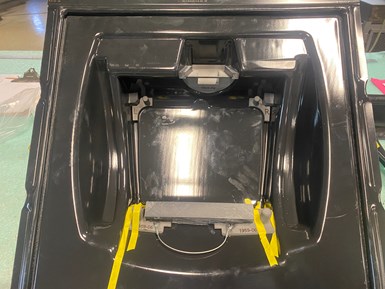
This type of 3D-printed locating fixture helps Productive Plastics meet their tight secondary tolerancing of 0.020 in. (Photos: Productive Plastics)
Until recently, Productive Plastics machined jigs out of wood, purchased fixtures from injection molders, or estimated clamp spacing without such manufacturing aids. But in the past year, the 68-year-old custom industrial thermoformer in Mount Laurel Township, N.J., has found innumerable uses for 3D printing of jigs, fixtures, and other manufacturing aids that have boosted its productivity and helped reduce costs, downtime and lead times. Specializing in A Fuse 1 With a specialty in heavy-gauge thermoforming, the company manufactures products ranging from large medical shrouds to armrest components for railway cars and enclosures for kiosks and vending machines. Productive’s services include design and product development, multi-part projects and assembly, painting and finishing.
Productive operates six manufacturing cells, each equipped with an industrial thermoformer (two of them rotary machines), a CNC milling machine, assembly area, and a computer system to organize and monitor operations. Productive also has an area for paint preparation, as well as a paint booth and curing oven. The company often uses thick sheets of PVC/acrylic alloy such as Kydex (a product of Sekisui Kydex), as well as ABS, PC , TPO and others. Avoiding waste by proper sizing and placement of clamps can save Productive and its customers thousands of dollars — and this was key in bringing 3D printing in-house.
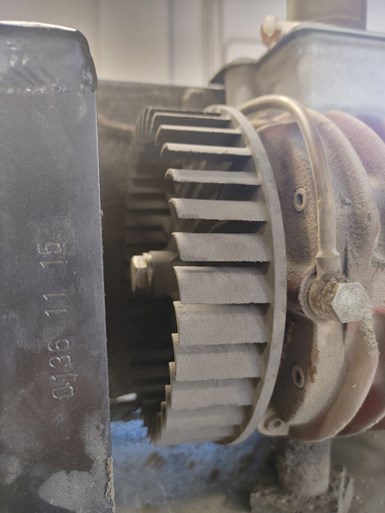
This 3D printed nylon 12 impeller enabled continued operation of a vacuum pump, instead of waiting weeks for a replacement part.
In January 2022, Productive Plastics installed a Fuse 1 SLS (selective laser sintering) 3D printer from Boston-based Formlabs. Using nylon 12 powder, the firm not only produces jigs and fixtures, but tooling engineer Dustin Johnson says his team has started to design and use 3D-printed supporting parts for customers’ assemblies and replacement parts for some of its own equipment. According to sales & marketing director Kyle Davidson, this in-house capability allows the firm to control production timing much better, as it’s easier to “push a print than to request a part from the customer or an outsourced provider.”
Examples include printing of 200 supporting parts for a bowling-alley components. During last year’s supply-chain delays, Johnson was also able to perfectly recreate in printed nylon 12 a small injection molded component that fits into a medical machine used in point-of-care facilities.
In one case, the team was able to replace a broken vacuum-pump impeller with a printed part instead of waiting weeks for the back-ordered replacement part to arrive. Using the Fuse 1 and nylon 12 powder allows Johnson to not only fix issues, but preemptively improve processes before they cause a problem. According to Johnson and Davidson, the major uses of Fuse I in order of priority have been:
▪ Locating jigs for the blocks — Johnson was able to design a locating jig that precisely maps out where to attach the blocks on the thermoformed piece, allowing operators to correctly attach the blocks in seconds.
▪ Secondary operations and painting — 3D printed stencil guides allow operators to cut quickly and efficiently.
▪ Visual aids for suppliers — When they need an outsourced part, they can print a sample as the benchmark to avoid confusion, as some suppliers prefer to work with 2D detailed drawings.
▪ Part reinforcements — The team can print thin-wall parts to support key areas of a formed part, which helps them produce deep-drawn parts without compromising material strength.
▪ Block sets for structural integrity or functional assembly attachments — These must fit perfectly into the thermoformed sheet, and because they are needed in the hundreds or thousands, mistakes are costly.
Other additive-manufacturing processes being considered by Productive Plastics include Large Format Additive Manufacturing (LFAM) for tooling and fused deposition modeling (FDM) where appropriate, according to Davidson, who was previously sales manager of Cincinnati Inc.’s Additive Manufacturing Div., and pioneered the adoption of innovative processes such as LFAM.
Related Content
Sheet Extrusion, Thermoforming Tips for PLA/aPHA Blends
Biopolymers like PLA and PHA are able to meet sustainability goals while also delivering the performance attributes needed in rigid food packaging. Here’s what testing has shown.
Read MoreAmcor, Berry Merge in All-Stock Deal
Move unites two complementary businesses to create a global leader in consumer packaging.
Read MoreMaking Gains in the Drain Game
AWD blends extrusion and thermoforming technologies with plenty of home-brewed equipment and processes to keep water away from where it isn’t supposed to be.
Read MoreThermoformed Container Keeps Battery Cells Safe
Despite last-minute design changes and other unexpected roadblocks, thermoformer TriEnda works with a key supplier on innovative reusable shipping container.
Read MoreRead Next
Beyond Prototypes: 8 Ways the Plastics Industry Is Using 3D Printing
Plastics processors are finding applications for 3D printing around the plant and across the supply chain. Here are 8 examples to look for at NPE2024.
Read MoreFor PLASTICS' CEO Seaholm, NPE to Shine Light on Sustainability Successes
With advocacy, communication and sustainability as three main pillars, Seaholm leads a trade association to NPE that ‘is more active today than we have ever been.’
Read MoreMaking the Circular Economy a Reality
Driven by brand owner demands and new worldwide legislation, the entire supply chain is working toward the shift to circularity, with some evidence the circular economy has already begun.
Read More