PE Film Market Snapshot 2020: Consumer/Industrial Product Liners
Monolayer structures still dominate this market.
This is the second in a series of blogs based on 2019-2020 research conducted by market-research firm Mastio & Co., St. Joseph, Mo. on key markets for processors of polyethylene film. There will be 10 articles in all, two a week. The first five will offer Mastio’s analysis—based on interviews with processors conducted direct by the Missouri firm—with film processors representing the five largest PE film markets. The second batch of five will be focused on the five fast-growing PE film markets.
The first of these blogs analyzed the stretch film market. Here we turn our attention to consumer/industrial product liners.
Check out the video that accompanies each of these articles in which Kevin Huntsman, Mastio’s senior vice president, and I discuss the takeaways of each market highlighted.
The Numbers
Polyethylene consumer and industrial product liners, defined by Mastio, are bags utilized as removable inner linings for boxes, cans, consumer product packaging, gaylord plastic shipping containers, plastic and steel drums, tote bins, and truck beds. Liners are also utilized as inner protective packaging for items that are packaged in additional outer packaging. As outer packaging surrounds most liners, issues such as clarity and printing are typically of lesser importance. In some applications, puncture resistance, tear strength, and barrier properties are of much greater importance for liners.
Rack and counter bags are also included in this market. They are mostly open-ended, perforated PE bags on a roll used to package non-food consumer and industrial products. Rack and counter bags are designed to be filled and sealed with automated filling machines. Other common trade terms for this type of packaging include the following: open-ended bags, pre-opened bags, easy-open bags, and Autobag. The most typical bag construction is a lay-flat bag on a perforated roll with an open bottom for easy filling. Automatic filling equipment opens, fills (by weight or count), seals, imprints or labels, separates, conveys the finished package, and is available in both fully automatic and semi-automatic designs.
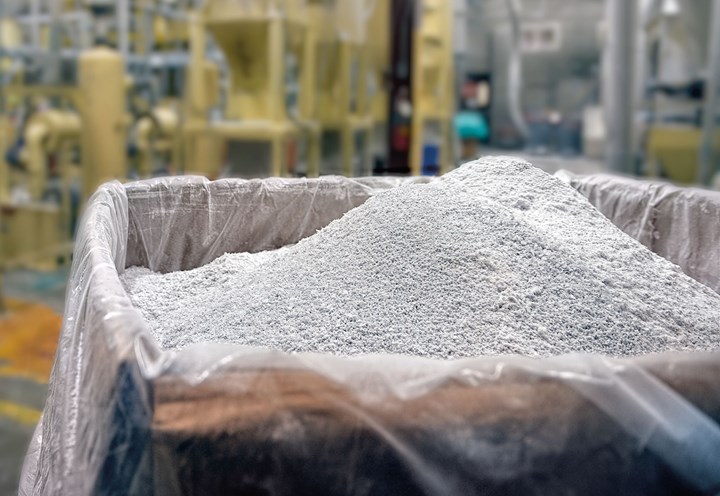
Liners (when used as an inner or outer product overwrap) help protect products from moisture, dust, contamination, spoilage, damage, and from becoming lost during shipping and storage. Liners used as inner packaging for boxes, cans, bins, drums, totes and truck beds, offer added protection for the products and facilitate greater ease of removing, cleaning, and reuse of the outer containers.
In 2019, approximately 815 million lb of PE was consumed in the production of liner film and bags, making it North America’s fifth largest film market for PE. With an average annual growth rate of 3.6%, PE resin consumption to produce liner film is anticipated to reach 906.5 million by 2022.
The Players
During 2019, Mastio reports the top five contributors to this market were Sigma Plastics Group; Berry Global Group; Novolex; API Industries; and Profile Films. Collectively, these companies processed a total of 401.1 million lb, representing 49.3% of the market.
The Resins
During 2019, LLDPE resin grades of butene, hexene, super hexene, octene, and metallocene outpaced LDPE resin consumption in this market. LLDPE resin offers greater film strength and improved puncture and tear resistance versus LDPE resins, Mastio’s research found. A few high-clarity grades of LLDPE resin are offered for applications where film clarity and increased film strength are equally important. Greater use of LLDPE resins, which are produced using the metallocene single-site catalyst process (mLLDPE), has been incorporated in the liner market. The mLLDPE resin grades (when utilized in blends or multilayer coextrusion) greatly improves film clarity, puncture resistance, and has good stretch characteristics in thinner gauges versus conventionally produced PE resins.
LDPE-homopolymer resin is still considered a resin of choice in the production of liners as it is easier to process, has high clarity, and is compatible with other PE resins when used in blends or multi-layer coextrusion. LDPE-homopolymer and LDPE-ethylene-vinyl acetate copolymer (LDPE-EVA copolymer) resin grades are extruded individually, in blends, or coextruded with other PE resins for liner production. LDPE-EVA copolymer resins are often used to increase the liner’s film clarity, low-temperature flexibility, impact resistance, and heat seal properties. LDPE-EVA copolymer resins are well-suited for use in liner film and bags that require printing. As the EVA copolymer percentage content increases, so does the impact strength (especially at lower temperatures), optical clarity, gas permeability, environmental stress crack resistance (ESCR), and COF. Conversely, as the EVA copolymer percentage increases, the stiffness modulus, surface hardness, tensile yield strength, and chemical resistance (generally) decreases.
Most liner film manufacturers produce monolayer PE films for liner applications—nearly 82%, according to Mastio.
HMW-HDPE and MMW-HDPE resins are also utilized in the liner market. HDPE resin is used alone, blended with other PE resins, or in multi-layer coextrusions. Increased film strength at lower gauges, barrier properties, increased bubble stability, and increased film stiffness, helps to improve the film’s ability to process smoothly during the converting process, are all additional benefits of using HDPE resin.
The Processing Trends
During 2019, blown film extrusion was the only reported film process utilized in the manufacturing of PE liner film. Furthermore, most liner film manufacturers produce monolayer PE films for liner applications—nearly 82%, according to Mastio.
Multi-layer coextruded films are utilized for an application where the end user may specify that the finished bags have different levels of coefficients of friction (COF) on the inside versus the outside of the bags. Producing bags with a high slip level on the inside facilitates greater ease of filling, allowing the components or parts to slide into the bag more easily. Coextruded film for this market also allows film processors the ability to downgauge the film by incorporating the use of a LLDPE resin as a center layer in a three-layer construction.
The Future
Approximately half of the processors surveyed by Mastio acknowledge that the liner market will remain flat or experience slow growth over the next few years. This market may not be a primary market for some companies, such as only supplying legacy customers, and liners can be described as a low profit margin market where manufacturers use their post-industrial scrap or waste to produce liners. Competition, both domestic and overseas, has also hindered some growth for a few participants. Furthermore, the most-mentioned reason for slow growth in the plastics liner market is the negative perception that single-use plastic films and bags are enduring, especially if they are not being recycled.
On the contrary, a few companies are experiencing an accelerated growth due to selling through distributors versus direct sales, lower resin prices, the improving economy, the increasing population, the restriction on Chinese imports, their internal expansion, new capital investment, and the fast-growing building and construction market.
Nearly all film and liner manufacturers have been implementing sustainable practices for years and even decades. They do this through reducing the amount of material used in production, using most internally generated waste, producing film from recycled material, and reclaiming film through collection programs for post- consumer and post-industrial recycling.
Furthermore, sustainability has resulted in discussion around biodegradability. The term “biodegradable” refers to the degradation process of plastic waste. However, consumers like the idea of biodegradable products until they learn about the higher price of the material used to produce biodegradable products.
With the big shift to plant based and biodegradable packaging, new bio-based materials are coming online. While starch-based and corn-based materials have been around longer, pea-based and soy-based materials are now being developed. One industry source says that by the year 2023, biodegradable packaging may be the only topic that is discussed in the industry.
Related Content
The Importance of Barrel Heat and Melt Temperature
Barrel temperature may impact melting in the case of very small extruders running very slowly. Otherwise, melting is mainly the result of shear heating of the polymer.
Read MoreReduce Downtime and Scrap in the Blown Film Industry
The blown film sector now benefits from a tailored solution developed by Chem-Trend to preserve integrity of the bubble.
Read MoreHow to Select the Right Cooling Stack for Sheet
First, remember there is no universal cooling-roll stack. And be sure to take into account the specific heat of the polymer you are processing.
Read MoreUse Interactive Production Scheduling to Improve Your Plant's Efficiencies
When evaluating ERP solutions, consider the power of interactive production scheduling to effectively plan and allocate primary and secondary equipment, materials and resources on the overall production capacity of the business and conclude that this is a key area that cannot be overlooked.
Read MoreRead Next
For PLASTICS' CEO Seaholm, NPE to Shine Light on Sustainability Successes
With advocacy, communication and sustainability as three main pillars, Seaholm leads a trade association to NPE that ‘is more active today than we have ever been.’
Read MorePeople 4.0 – How to Get Buy-In from Your Staff for Industry 4.0 Systems
Implementing a production monitoring system as the foundation of a ‘smart factory’ is about integrating people with new technology as much as it is about integrating machines and computers. Here are tips from a company that has gone through the process.
Read MoreLead the Conversation, Change the Conversation
Coverage of single-use plastics can be both misleading and demoralizing. Here are 10 tips for changing the perception of the plastics industry at your company and in your community.
Read More