BASF’s Ultradur PBT Replaces Steel in Structural Bracket of Sunroof Headliner
Automotive sunroof frame made with BASF’s Ultradur High Speed is 60% lighter than traditional solutions.
A new automotive panorama roof has been developed by BASF and Spain’s Tier I automotive supplier Grupo Antolin that meet both the increasing demand for panoramic roofs and the need to reduce the weight of all automotive components to minimize CO2 emissions.
The newly developed panorama roof is integrated into the ceiling trim (called the headliner) of the car which is made from the very light BASF’s light polyurethane Elastoflex E 3943/134. The actual sunroof opening in the headliner is supported by a structural bracket. Traditionally this is made of heavy steel. With BASF’s new rheologically modified Ultradur High Speed PBT, a metal replacement solution is now used.
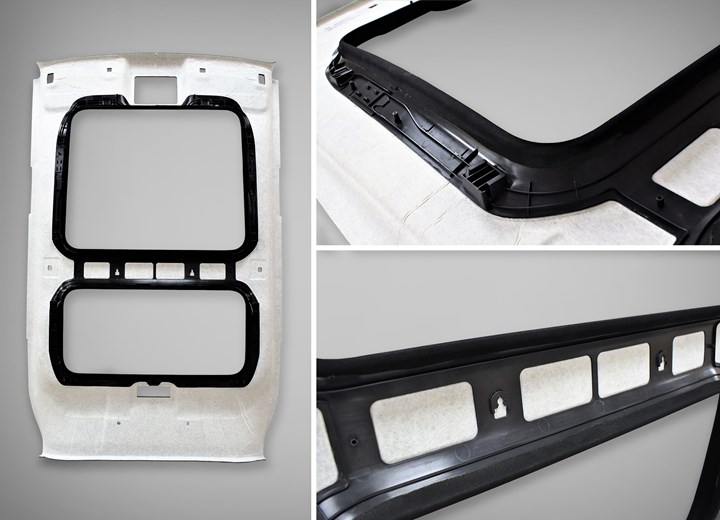
In close cooperation, both companies have successfully validated the Ultradur High Speed PBT in plastic frames for open panorama headliners. The novel and new design of these parts is said to allow for a 60% weight reduction compared to other traditional solutions. This PBT has been shown to allow the injection of large parts with unique performance such as excellent dimensional stability, low warpage at short cycle times, high stiffness, high temperature resistance and an outstanding flowability.
Explained Grupo Antolin’s project engineer Enrique Fernandez, “One of the main advantages of the newly designed plastic parts is the change in the process. We attach the frame to the headliner. During the production process the panorama reinforcement frame is fixed to the interior trim part while at the same time the part is formed in the mold. That leads to the elimination of additional process steps and moreover it improves tolerances during assembly and the quality of the final part is increasing. In addition, the new process does not involve the use of any solvents and does not generate hazardous emissions.”
Said Dirk Salzmann, key account manager in BASF’s Performance Materials division, “The new rheological modified Ultradur High Speed has an outstanding flowability that is crucial to obtain large and slim interior trim parts. Moreover, considering its unprecedented processing advantages, we have been able to reduce weight without losing stiffness and dimensional stability at high temperatures.”
Following the predevelopment with a German customer, the first pilot project was launched for a best-seller vehicle with outstanding results. More opportunities with this solution have been identified for several OEMs at global scale.
Related Content
-
Atop the Plastics Pyramid
Allegheny Performance Plastics specializes in molding parts from high-temperature resins for demanding applications as part of its mission to take on jobs ‘no one else does.’
-
Industrial Resin Recycling Diversifies by Looking Beyond Automotive
Recycler equips for new business in medical, housewares and carpeting.
-
Injection Molded Enclosures Plug into Potential Electric Vehicle Battery Applications
In partnership with material suppliers, Engel is proving out injection molded thermoplastic-based concepts for electric vehicle battery housings, utilizing production tools and dedicated machines at its large press factory in St. Valentin, Austria.