Comar Cuts Ribbon on New Plant
The supplier of packaging and custom medical devices marked the completion of its nine-month effort to shift operations to its largest Wisconsin facility to date.
Comar (Voorhees, N.J.) completed its West Bend 2.0 project, shifting operations from its existing facility in West Bend, Wisc. to its largest facility in the state to date. Located less than five miles from the old site, the new ISO 9001 certified facility triples Comar’s local footprint to 160,000 ft2 and features high-tonnage molding machines, high-cavitation molds, and press-side automation.
The site will provide specialty packaging, including stock extrusion blow-molded containers, injection-molded lids and closures, and a wide variety of engineered custom products and assemblies.
In a release, Comar CEO Mike Ruggieri said the dedication of the new West Bend plant caps a year of capability growth for Comar, over which time the company enhanced its East Coast presence with a new Vineland, N.J. location and combined two plants into one state-of-the-art facility in Rancho Cucamonga, Calif. Staying in West Bend allowed the company to retain and invest in its existing teams, according to Comar, as well as the community. The new facility includes improved floor layouts, break rooms, and dedicated training areas.
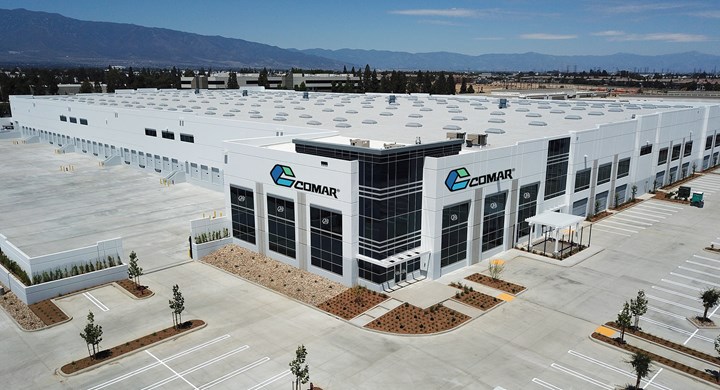
Earlier this year, Comar combined two California sites into a new facility in Rancho Cucamonga (pictured here).
Photo Credit: Comar
Related Content
-
Allegheny Performance Plastics to Enter Health Care Sector
The custom molder has secured multiple projects in health care and will be adding cleanroom and white-room spaces, as well as injection molding machines, in support.
-
What to Look for in High-Speed Automation for Pipette Production
Automation is a must-have for molders of pipettes. Make sure your supplier provides assurances of throughput and output, manpower utilization, floor space consumption and payback period.
-
Compact Solution for Two-Component Molding
Zahoransky’s new internal mold handling technology foregoes the time, space and money required for core-back, rotary table or index plate technologies for 2K molding.