Conair to Market Blenders, Gauge Controls for Film and Fiber under Conair by Doteco Brand
New brand under which the products are being sold reflects the complementary nature of two sister companies.
Conair Group it is now selling and servicing three market-leading product lines developed by Doteco SPA of Italy to film and fiber producers in North America. Doteco and Conair are both Piovan Group companies and the new brand reflects Piovan’s desire to deliver Doteco technology to the North American market.
The three product lines — Blendo Adroit and Grado Adroit blenders and the Vento air ring — are the vanguard of a new Conair by Doteco brand that is being marketed through Conair Group’s extensive North American sales and service organization. The move follows Piovan Group’s 2019 acquisition of Doteco and its 2021 acquisition of IPEG — including Conair, Thermal Care, Pelletron, and Republic Machine — which helped make Piovan Group a global leader in systems for the automation of plastics processing.
For Conair, the move is a golden opportunity, bringing new technology that will advance its prospects in North America’s huge fiber and blown film market, explains Alan Landers, Conair’s general manager for Doteco Inc. (the U.S. arm for Doteco), who is spearheading the Conair by Doteco introduction.
“From its beginning in 1994, Doteco has focused on extrusion processing, and the design and precision of their blenders have made them the envy of the industry,” said Landers. “In the fiber segment, where thread color, texture, and consistency are critically important, Doteco’s continuous loss-in-weight blenders, including the Blendo Adroit, rank high in a very competitive field for auxiliary equipment due to their reliability, dosing and mixing accuracy, and ease of use.”
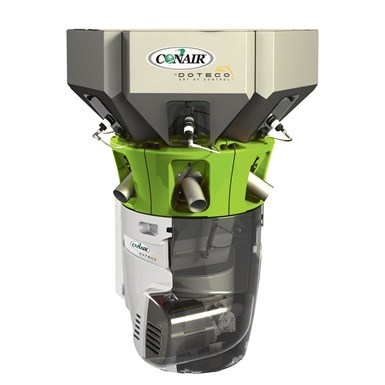
Conair says the Grado Adroit batch blender was the first that could mix and weigh in a single hopper, with a compact design preferred by film extruder OEMs.Photo: Conair
Landers added that Doteco’s innovative blenders have enjoyed even greater success in the blown film market: “Doteco was the first company to develop a batch blender that could mix and weigh in a single hopper. Combining that compact hopper with an extremely precise, reliable dosing valve created a loss-in-weight batch blender — now the Grado Adroit — that is much shorter and easier to mount in the confines of a film extruder and tower. That innovation enabled Doteco to develop strong relationships with extruder manufacturers that have helped make it the top blender for blown film, especially multi-layer films.”
The new brand offering also includes the new Vento profile gauge-control system for film extrusion. With several models sized for film dies from 5.9 in. to 35.4 in. (150-900 mm), the Vento combines film cooling and gauge control. A single air inlet provides a consistent inflow of air, divided into three radial flows that shape the molten film bubble. A servo-controlled motor uses real-time gauge measurements to direct small, but precise changes in airflow around the circumference of the film bubble to ensure thickness consistency.
The new blenders and air ring complement existing Conair product lines, greatly strengthening its product offering in the film and fiber market and opening new sales opportunities. And, that’s where Conair’s sales and service force, the largest in North America, comes in.
The new brand under which the products are being sold reflects the complementary nature of the sister companies, explains Landers. “We want people to know that there are two strong organizations delivering these products: Conair, which is leveraging its North American sales and service organization, and Doteco, which is providing specialty products respected for great design and a strong reputation in key specialty markets.”
Related Content
Reduce Downtime and Scrap in the Blown Film Industry
The blown film sector now benefits from a tailored solution developed by Chem-Trend to preserve integrity of the bubble.
Read MoreMedical Tubing: Use Simulation to Troubleshoot, Optimize Processing & Dies
Extrusion simulations can be useful in anticipating issues and running “what-if” scenarios to size extruders and design dies for extrusion projects. It should be used at early stages of any project to avoid trial and error and remaking tooling.
Read MoreThe Importance of Barrel Heat and Melt Temperature
Barrel temperature may impact melting in the case of very small extruders running very slowly. Otherwise, melting is mainly the result of shear heating of the polymer.
Read MoreHow to Select the Right Tooling for Pipe Extrusion
In pipe extrusion, selecting or building a complementary set of tooling often poses challenges due to a range of qualitative factors. Here’s some guidance to help you out.
Read MoreRead Next
For PLASTICS' CEO Seaholm, NPE to Shine Light on Sustainability Successes
With advocacy, communication and sustainability as three main pillars, Seaholm leads a trade association to NPE that ‘is more active today than we have ever been.’
Read MoreSee Recyclers Close the Loop on Trade Show Production Scrap at NPE2024
A collaboration between show organizer PLASTICS, recycler CPR and size reduction experts WEIMA and Conair recovered and recycled all production scrap at NPE2024.
Read MoreLead the Conversation, Change the Conversation
Coverage of single-use plastics can be both misleading and demoralizing. Here are 10 tips for changing the perception of the plastics industry at your company and in your community.
Read More