Crosslinking Process Promises Thinner, Higher-Performance PE Films
Technology combines UV curing system with photo initiator promoter masterbatch.
Kafrit, a well-known Israeli masterbatch and additives manufacturer, has collaborated with start-up Israeli additives company N3Cure to create what they call a breakthrough in crosslinking technology for PE films. The system combines a proprietary masterbatch called Crossitol with UV curing radiation to enable processors to produce PE films that will crosslink to improve sustainability and cut costs.
Under the arrangement between the two companies, N3Cure, specialists in polymers, UV curing and sustainability, provides the raw material for the crosslinking additive to Kafrit, which compounds it into a masterbatch. The UV technology is furnished by an undisclosed curing system provider.
Crosslinking is the process of forming covalent bonds to join two polymer chains. With the Crossitol masterbatch, the process is triggered by UV radiation, applied by a UV curing system and integrated on an existing blown film line, resulting in a polymer web-like structure that is stronger than a regular, non-crosslinked polymer chain structure.
“UV crosslinking was designed to be a more cost-effective alternative to electronic-beam technology as it has a higher speed process, and lower maintenance and equipment costs. Unlike electronic-beam technology, selective crosslinking can be applied, and the finished product is easier to recycle,” said Kafrit’s Nadav Goldstein, v.p. of new business development.
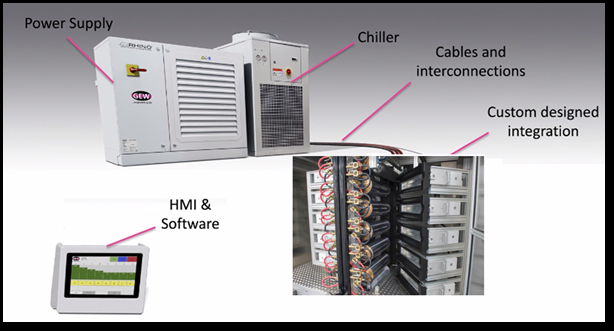
FIG 1 Components of UV curing system. Photos: N3Cure
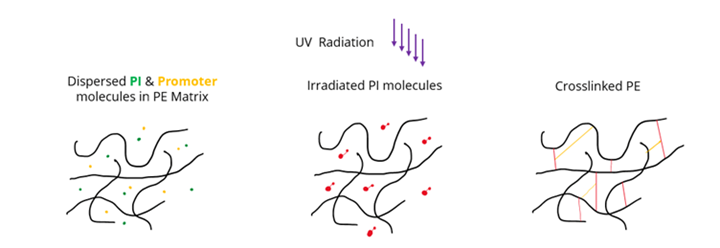
FIG 2 Crosslinking PE generates a polymer web-like structure that is stronger than a non-crosslinked polymer chain structure.
The UV curing system is comprised of several units: lamps system (including rollers); chillers (air/water); power supply unit; and an HMI (Fig 1). It can be tailored for specific processing lines. This tailor-made process ensures quick and seamless installation, with minimal downtime to the production line. The masterbatch and UV curing system can be used in valid range of blown and cast-film applications.
To improve the crosslinking process even further, a promoter is dispersed in the PE matrix in addition to the photo initiator. A reaction between them occurs and improves the web formation as shown in Fig. 2.
As the companies explain, there are three main reasons to crosslink PE films:
- Sustainability: Crosslinking enables the production of recyclable packaging with a single-polymer structure, which facilitates post-consumer recyclability. A stronger web permits downgauging to reduce material usage. Because it’s crosslinked, the thinner film has the same mechanical properties as thicker film with a reduced carbon footprint.
- Economics: Compared to other radiation methods, UV crosslinking has a relatively low entry barrier. In double- or even triple-bubble film applications, it is said to increases bubble stability and production line output. It can also replace high-end polymers and increase savings on energy, labor, maintenance, and logistics costs.
- More Design Freedom: Crosslinking enables innovative product design with a focus on recyclability. Selective crosslinking (area specific) products allow flexible solutions to fit any customer needs and achieve superior packaging properties such as a wider sealing operating window; improved tensile and tear properties; stronger, faster, and higher percentage of shrinkage.
Kafrit and N3Cure says the UV curing systems and Crossitol masterbatch combination results in an entirely homogenous film and can target specific layers without affecting the other film layers. Non-crosslinked edges can be trimmed and recycled online or offline.
Additives supplier Polyfil, Rockaway, N.J. is a subsidiary of Karafit.
Related Content
How to Select the Right Tooling for Pipe Extrusion
In pipe extrusion, selecting or building a complementary set of tooling often poses challenges due to a range of qualitative factors. Here’s some guidance to help you out.
Read MoreWhy Are There No 'Universal' Screws for All Polymers?
There’s a simple answer: Because all plastics are not the same.
Read MoreReduce Downtime and Scrap in the Blown Film Industry
The blown film sector now benefits from a tailored solution developed by Chem-Trend to preserve integrity of the bubble.
Read MoreUnderstanding Melting in Single-Screw Extruders
You can better visualize the melting process by “flipping” the observation point so the barrel appears to be turning clockwise around a stationary screw.
Read MoreRead Next
Making the Circular Economy a Reality
Driven by brand owner demands and new worldwide legislation, the entire supply chain is working toward the shift to circularity, with some evidence the circular economy has already begun.
Read MorePeople 4.0 – How to Get Buy-In from Your Staff for Industry 4.0 Systems
Implementing a production monitoring system as the foundation of a ‘smart factory’ is about integrating people with new technology as much as it is about integrating machines and computers. Here are tips from a company that has gone through the process.
Read MoreSee Recyclers Close the Loop on Trade Show Production Scrap at NPE2024
A collaboration between show organizer PLASTICS, recycler CPR and size reduction experts WEIMA and Conair recovered and recycled all production scrap at NPE2024.
Read More