First Stretch Film Approved for Use in Potentially Explosive Areas
Film maker DuoPlast and BASF collaborate on production of new film that avoids the ignition source electrostatics.
BASF collaborated with Germany-based film manufacturer DuoPlast to commercially launch what is said to be the world’s first stretch PE blown film approved for use in potentially explosive areas. The newly developed Duo Ex-Tra multilayer LDPE film avoids the ignition source of electrostatics. As such, stretched pallet units no longer pose an explosion hazard. Conventional stretch films are not approved for explosive areas due to the static charge and pallets must be repacked before entering.
DuoPlast’s film is made with BASF’s Elastostat, a dissipative polymer-based TPU additive. Available as a pellet masterbatch, this additive’s antistatic effect is permanent and does not require any specific ambient conditions. It is said to have high compatibility with PE, PP, PS, and ABS at typical use levels of 7.5-15% and, as such, stretch films with Elastostat are particularly suitable for companies in the chemical industry and their suppliers, who can be supplied directly to hazardous areas in the future. The film is color-coded with red flashes. Hence, wrapped pallets can be clearly identified visually and their suitability for the relevant areas can be ensured.
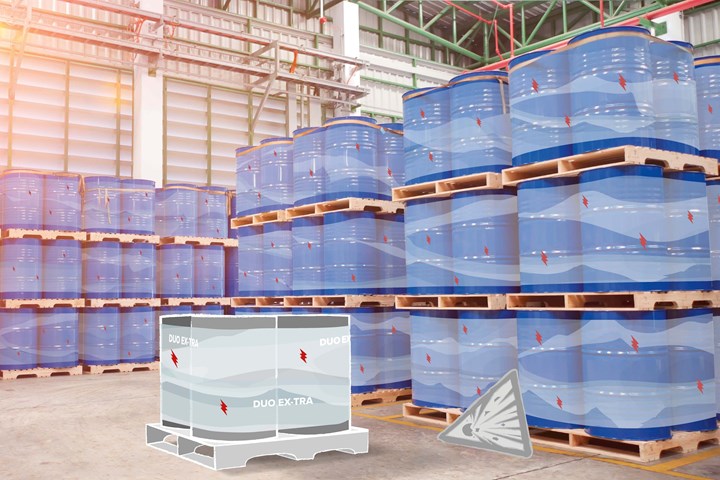
Said Anja Oltmanns, TPU sales, BASF, "Combining our additive with the film to increase conductivity was not feasible straight away. We had to both achieve the required surface resistance and maintain stretchability while at the same time considering the thinness of the film.”
Noted DuoPlast’s key account manager Nina Schnitzler, "The blown film produced in cooperation with BASF is unique worldwide as there has been no stretch film on the market before that was approved for hazardous areas. Thus, the film can be used for packaging conductive containers in contact with earth in potentially explosive atmospheres (zones 1 and 2). Removal of the foil is also permitted in the aforementioned zones.” In addition, the Duo Ex-Tra film is equipped with the patented Duo Double Edge which has enormous holding forces. The net structure created during processing enables optimum load unit stability with minimal material consumption, according to Schnitzler.
Related Content
-
Polyethylene Fundamentals – Part 4: Failed HDPE Case Study
Injection molders of small fuel tanks learned the hard way that a very small difference in density — 0.6% — could make a large difference in PE stress-crack resistance.
-
The Fundamentals of Polyethylene – Part 2: Density and Molecular Weight
PE properties can be adjusted either by changing the molecular weight or by altering the density. While this increases the possible combinations of properties, it also requires that the specification for the material be precise.
-
Fundamentals of Polyethylene – Part 5: Metallocenes
How the development of new catalysts—notably metallocenes—paved the way for the development of material grades never before possible.