Moldworx Consolidates Into Single facility
The injection molder and moldmaker has combined those functionalities into a single operation in Chandler, Ariz.
Founded in 1995, Moldworx LLC began as a mold repair and mold building business, before expanding into injection molding and adding a second facility. Earlier this year, it combined those operations into a single 24,000-ft2 stand-alone facility in Chandler, Ariz. A company spokesperson told Plastics Technology that the former facilities covered a total of 15,100-ft2.
Presses, including 2-shot capabilities, range in size from 55 to 400 tons with machines from Nissei, Wittmann Battenfeld, Van Dorn, Sandretto, Cincinnati and Demag. Multiple machines are equipped with robotics including 3-axis systems from Sepro and Yushin, as well as a Conair sprue picker.
The company plans to begin offering White Room molding services for the medical industry in addition to its contract manufacturing services that include overmolding, heat staking and automation development for product assembly and work-flow process design and engineering.
Recently, the company began making FDA approved face masks to help fill the demand for these items due to the coronavirus pandemic. The masks are made from a pliable thermoplastic polyurethane material, with reusable, replaceable FDA approved N95 filter elements. To date, Moldworx has produced 2,000 masks to be donated to healthcare professionals in Arizona.
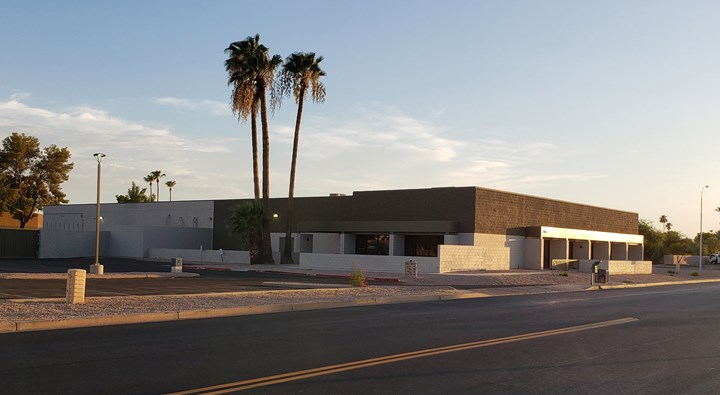
Related Content
-
Got Streaks or Black Specs? Here’s How to Find and Fix Them
Determining the source of streaking or contamination in your molded parts is a critical step in perfecting your purging procedures ultimately saving you time and money.
-
Is There a More Accurate Means to Calculate Tonnage?
Molders have long used the projected area of the parts and runner to guesstimate how much tonnage is required to mold a part without flash, but there’s a more precise methodology.
-
What to Look for in High-Speed Automation for Pipette Production
Automation is a must-have for molders of pipettes. Make sure your supplier provides assurances of throughput and output, manpower utilization, floor space consumption and payback period.