Natech Adds Injection Molding, Automation Equipment
Two new Arburg presses and four filling and sealing lines have been installed in the molder’s Class 8 cleanroom in support of medical diagnostics, including COVID-19 testing.
Natech Plastics (Ronkonkoma, N.Y.) has installed six new pieces of equipment in the fourth quarter of 2021, including two Arburg injection molding machines and four custom-made filling and sealing machines. A Natech spokesperson said the latest machines come with clamp forces of 110 and 165 tons, respectively. Natech’s machine fleet of 16 presses ranges in size from 40 to 400 tons.
Natech’s facility includes an ISO Class 8 Cleanroom and engineering and design services, as well as secondary operations. The two new injection molding machines, alongside the cleanroom, will be used to manufacture medical and diagnostics products, including molded plastic components and finished devices. In particular, the spokesperson said Natech is expanding its support of diagnostics industry, including a program focused on COVID-19 testing, with these machines supplying filled tubes and bottles for rapid antigen tests.
The four new filling and sealing machines added to the cleanroom space were custom-designed and built for Natech. Featuring a modular, interchangeable design that allows for a variety of processes (filling, capping, heat sealing) to run on a single machine, they also have a built-in shuttle so filled product can be transferred to the sealing station. The rapid COVID-19 antigen tests require filling and and sealing of containers that house extraction buffers. Natech noted that the new Arburg machines allow the machine, conveyor and robot to all be integrated.
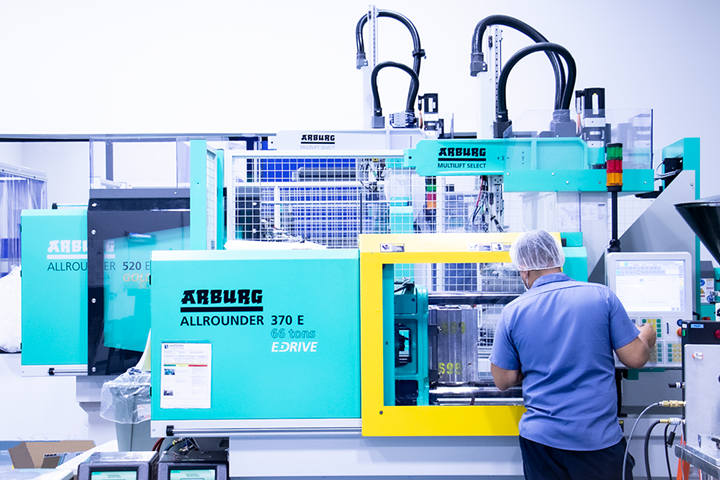
Natech has added two Arburg injection molding machines to its fleet in support of medical diagnostics products, including COVID-19 rapid antigen tests. (Photo: Natech)
Related Content
-
How to Optimize Injection Molding of PHA and PHA/PLA Blends
Here are processing guidelines aimed at both getting the PHA resin into the process without degrading it, and reducing residence time at melt temperatures.
-
PHA Compound Molded into “World’s First” Biodegradable Bottle Closures
Beyond Plastic and partners have created a certified biodegradable PHA compound that can be injection molded into 38-mm closures in a sub 6-second cycle from a multicavity hot runner tool.
-
Get Color Changes Right In Extrusion Blow Molding
Follow these best practices to minimize loss of time, material and labor during color changes in molding containers from bottles to jerrycans. The authors explore what this means for each step of the process, from raw-material infeed to handling and reprocessing tails and trim.