New Form of 3D-Printed Material Aimed at Lighter, Safer Car Designs and More
Team of researchers led by University of Glasgow combined polyolefins with multiwall carbon nanotubes to come up with a new plate-lattice cellular ‘metamaterial’ with impressive impact resistance.
A new form of 3D-printed composite material made by combining polyolefin resins with multiwall carbon nanotubes was developed by a research team led by University of Glasgow engineers that is tougher and lighter than similar forms of aluminum. The team anticipates that this could lead to the development of safer, lighter and more durable structures for use in the automotive, aerospace, renewables and marine industries. In a new paper, Impact Behaviour of Nanoengineered, 3D Printed Plate-Lattices, published in the journal Materials & Design, the team describe how they have developed a new plate-lattice cellular ‘metamaterial’ capable of impressive resistance to impacts.
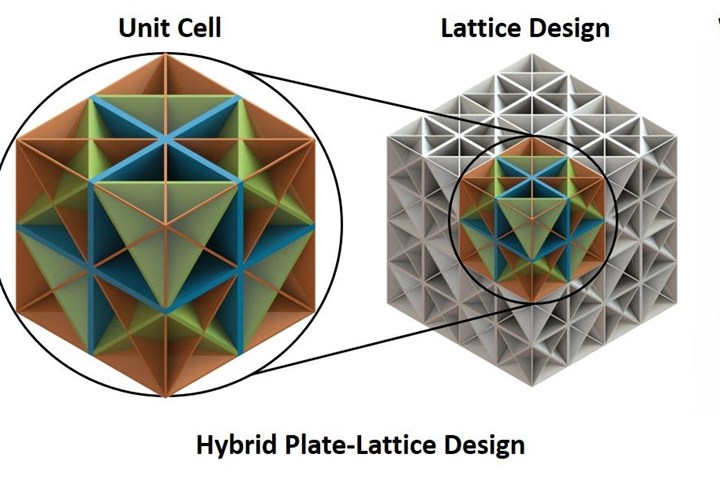
Metamaterials are a class of artificially-created cellular solids, designed and engineered to manifest properties which do not occur in the natural world. One form of metamaterials, known as plate-lattices, are cubic structures made from intersecting layers of plates that exhibit unusually high stiffness and strength, despite featuring a significant amount of space between the plates. Those spaces, which are a property engineers call porosity, also makes plate-lattices unusually lightweight.
The researchers set out to investigate whether new forms of plate-lattice design, manufactured from a plastic-nanotube composite they developed, could make a metamaterial with even more advanced properties of stiffness, strength and toughness. They used their nanoengineered filament composite as the feedstock in a 3D printer which fused the filaments together to build a series of plate-lattice designs. Those designs were then subjected to a series of impact tests by dropping a 16.7kg mass from a range of heights to determine their ability to withstand physical shocks.
First, the team tested three types of typical plate-lattices they designed and built: a simple cube formed from the intersection of three plates; a more complex cube with additional intersecting plates; and, a more multifaceted design. Those typical plate-lattices were made in two batches--one from polypropylene and one from polyethylene.
Then, they tested three more ‘hybrid’ plate-lattices which incorporated features from the simpler designs in the first experiments: a simple cube/complex cube hybrid; a simple cube/multifacet hybrid; and, one which amalgamated all three. Again, batches made from PP and PE were made.
The hybrid design which amalgamated elements of all three typical plate-lattice designs proved to be the most effective in absorbing impacts, with the PP version showing the greatest impact resistance. Using a measure known as specific energy absorption, which scientists use to determine a material’s ability to absorb energy relative to its mass, the team found that the PP hybrid plate-lattice could withstand 19.9 joules per gram—reportedly, a superior performance over similarly-designed microarchitected metamaterials based on aluminium.

Dr Shanmugam Kumar, Leader in Composites and Additive Manufacturing in the University of Glasgow’s James Watt School of Engineering, led the research project. The research team also involved mechanical and chemical engineers from Khalifa University in Abu Dhabi and Texas A&M University at College Station in the USA.
Said Kumar, “This work sits right at the intersection of mechanics and materials. The balance between the carbon nanostructure-engineered filaments we’ve developed as a feedstock for 3D printing, and the hybrid composite plate-lattice designs we’ve created, has produced a really exciting result. In the pursuit of lightweight engineering, there is a constant hunt for ultra-lightweight materials featuring high performance. Our nanoengineered hybrid plate-lattices achieve extraordinary stiffness and strength properties and exhibit superior energy absorption characteristics over similar lattices built with aluminum. Advances in 3D printing are making it easier and cheaper than ever to fabricate the kinds of complicated geometries with tailored porosity that underpin our plate-lattice design. Manufacture of this kind of design at industrial scales is becoming a real possibility.”
According to Kumar and the team, a key application for this new kind of plate-lattice could well be in automotive manufacturing, where there is a perpetual strive to build more lightweight bodies without sacrificing safety during crashes. “Aluminum is used in many modern car designs, but our plate-lattice offers greater impact resistance, which could make it useful in those kinds of applications in the future…The recyclability of the plastics we’re using in these plate-lattices also makes them attractive as we move towards a net-zero world, where circular economic models will be central to making the planet more sustainable,” noted Kumar.
Related Content
3D Printing of Injection Molds Flows in a New Direction
Hybrids of additive manufacturing and CNC machining can shorten tooling turnaround times.
Read MoreAdditive Technologies for Injection Mold Tooling Ride Tailwinds
NPE2024: Lowering barriers to additive manufacturing adoption in toolmaking.
Read MoreMake Every Shot Count: Mold Simulation Maximizes Functional Parts From Printed Tooling
If a printed tool only has a finite number of shots in it, why waste any of them on process development?
Read MoreProduction Tool, Prototype Time
Mantle's metal 3D printing technology targeted toolmaking and injection molders and moldmakers are taking notice.
Read MoreRead Next
For PLASTICS' CEO Seaholm, NPE to Shine Light on Sustainability Successes
With advocacy, communication and sustainability as three main pillars, Seaholm leads a trade association to NPE that ‘is more active today than we have ever been.’
Read MoreLead the Conversation, Change the Conversation
Coverage of single-use plastics can be both misleading and demoralizing. Here are 10 tips for changing the perception of the plastics industry at your company and in your community.
Read More