Novoloop and Aether Break Ground on Pilot Plant for PE Upcycling
India facility will test Novoloop's Lifecycling chemical recycling technology.
Novoloop announced groundbreaking on its pilot plant in India, a collaboration with Aether Industries, a specialty chemical manufacturer and chemical process development provider. The plant is intended to demonstrate the scalability of Novoloop’s Lifecycle technology, an oxidation process for converting postconsumer polyethylene into monomers for the synthesis of high-performance materials such as thermoplastic polyurethane (TPU).
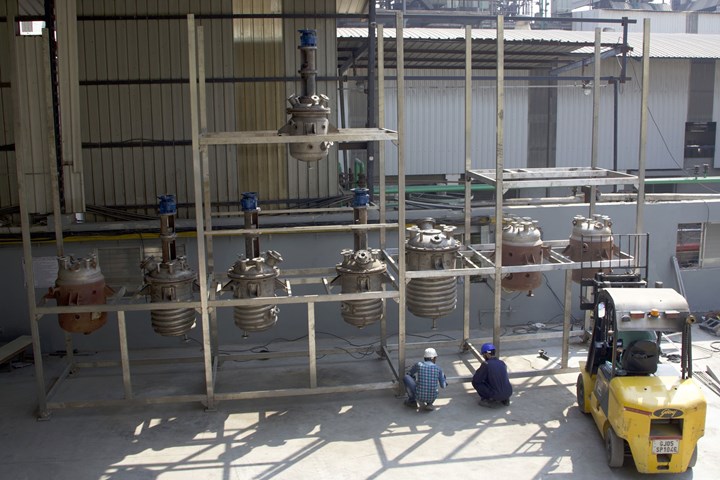
Novoloop pilot plant under construction in India. Photo Credit: Aether Industries
Novoloop expects to provide durable material products at prices competitive with fossil-based products. According to the company, an ISO-compliant life cycle assessment has shown that Novoloop monomers can realize a carbon footprint reduction of up to 91% when compared to the conventional process of producing adipic acid.
“The integrated pilot plant, mirroring our full-scale commercial process design, marks a pivotal advancement in technology readiness,” says Nedim Hasanbegovic, vice president of Engineering at Novoloop
Equipped with the applicable instrumentation, process controls and safety systems, the pilot plant is expected to demonstrate the technology in a real-world operating environment, thus paving the way for full-scale production.
“This pilot plant is a testament to the commitment of the Novoloop team and our partners at Aether Industries to tackle the global plastic crisis,” says Miranda Wang, co-founder and CEO at Novoloop. “By scaling this technology, we are creating a pathway toward a truly circular world, where plastic waste becomes a valuable resource.”
The project will unfold in phases, with the startup of initial operations commencing in Q1 of 2024 and ramping up by the end of 2024, when plastic intake capacity is expected to ultimately reach 70 metric ton/yr. The phased approach was chosen to allow for data collection and optimization at each step, to ensure a robust and scalable operation. Products generated from the pilot plant will be made available to customers for trial and commercial release.
Related Content
-
Latest Data on Bottled Water Shows Continued Strong Growth
Bottled water’s volume surpassed soft drinks for the first time in 2016 and has done so every year since.
-
Evolving Opportunities for Ambitious Plastics Recycler
St. Joseph Plastics grew from a simple grinding operation and now pursues growing markets in recycled PP, food-grade recycled materials, and customized post-industrial and post-consumer compounds.
-
At NPE2024, Follow These Megatrends in Materials and Additives
Offerings range from recycled, biobased, biodegradable and monomaterial structures that enhance recyclability to additives that are more efficient, sustainable and safer to use.