Thermoplastics Structures the Focus of Engel’s China Composites Expo Presence
At the China Composites Expo 2020 (Sept. 2-4; Shanghai), Engel will highlight its thermoplastic based organomelt composite technology saying it represents the “answer to sustainable transport.”
An Engel spokesperson told Plastics Technology that the Austrian supplier of injection molding and automation technology’s China Composites Expo (Sept. 2-4) booth will present previously launched technologies using parts and video presentations, with an emphasis on thermoplastic based structures.
Engel notes that organomelt has already been adopted in high-volume jobs, including fully automated production of front-end carriers for Daimler, and it’s drawing growing interest in Asia, a major hub of automotive manufacture globally. Markus Fuchs, director business unit automotive Asia, said interest is coming from OEMs and Tier One suppliers for applications including seat shells, consoles and interior structural components.
In the organomelt process, thermoplastic fiber composite prepregs based on thermoplastic fabrics and unidirectional (UD) fiberglass or carbon fiber reinforced tapes are heated in specially developed infrared ovens. That composite component is then placed into the injection mold by a robot, where it is formed and functionalized in a single step. By using injection molding, Engel notes that reinforcing ribs or assembly elements can be overmolded directly. Since the structure consists entirely of thermoplastics, its end-of-life options do not preclude recycling.

Engel’s production cells integrate all processing steps for composite parts, starting with individual tapes all the way through to “functionalization” via injection molding.
Engel says the process is continuously under development, and at present, the company is investigating the combination of several different prepregs—thermoplastic fabrics of different thicknesses or UD tapes—in a single component to create areas with varying levels of rigidity based on the mechanical load they’ll see in the field.
To demonstrate this at the expo, Engel is showing a door structure developed in partnership with automotive supplier Brose. In this application, three thermoplastic fabrics with thicknesses between 0.6 and 2.5 mm are processed. The different loads on the individual component areas are optimized for their role in the part so that the door structure is more rigid around the window frame than on the inside of the door, for instance.
On the more traditional thermoset side, Engel will demonstrate how production efficiency can still be improved even for long-established technologies. On display will be the rear seat panel of the Audi A8, which has a complex carbon fiber structure and local reinforcements. Series production is by a supplier from Germany using an Engel v-duo 1700 machine with the fully automated HP-RTM (resin transfer molding) process.
Early U.S. Adopter
The spokesperson said there are several organomelt applications running in high volume currently, with more projects in evaluation. The very first large-scale production project was launched in Tennessee to create front-end carriers with integrated air ducts.
Introduced at Composites Europe 2018, that fully automated, large-scale production cell consists of a duo 1700 injection molding machine with 1900 tons of clamping force; three easix articulated robots for handling metal inserts and organosheet; a viper 90 linear robot for finished part manipulation; and a size 5 IR oven for producing two half-shells in the same mold in a one-shot process. Tepex dynalite type organic sheets from Bond Laminates are used with glass loaded into a polypropylene matrix. Glass-fiber-reinforced polypropylene is also used for overmolding.
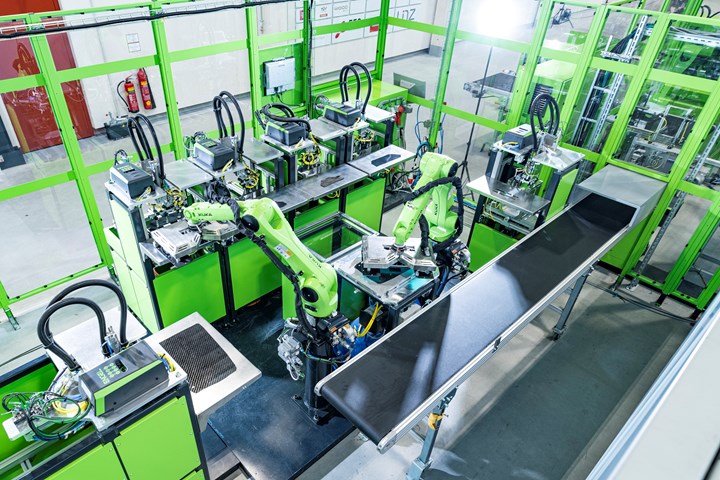
The tape laying unit developed by Engel can deliver tailor-made prepregs for its organomelt process in a one-minute cycle time.
Related Content
Advanced Biobased Materials Company PlantSwitch Gets Support for Commercialization
With participation from venture investment firm NexPoint Capital, PlantSwitch closes it $8M bridge financing round.
Read MoreLanxess and DSM Engineering Materials Venture Launched as ‘Envalior’
This new global engineering materials contender combines Lanxess’ high-performance materials business with DSM’s engineering materials business.
Read MorePrices Up for All Volume Resins
First quarter was ending up with upward pricing, primarily due to higher feedstock costs and not supply/demand fundamentals.
Read MorePrices Up for PE, ABS, PC, Nylons 6 and 66; Down for PP, PET and Flat for PS and PVC
Second quarter started with price hikes in PE and the four volume engineering resins, but relatively stable pricing was largely expected by the quarter’s end.
Read MoreRead Next
Trio of Headlines in Lightweight Composites for Automotive & More
Injection overmolding in automotive; HP-RTM of hollow composite parts; and development of specialized equipment for UD tape stacking and consolidation.
Read More‘Organic Hybrid’ Composites Highlighted at K Show
One of the materials trends hailed at this month’s K 2010 show in Dusseldorf was the replacement of plastic-metal “hybrid” composites with all-plastic “organic hybrids” in structural parts for automotive and other markets.
Read MoreSee Recyclers Close the Loop on Trade Show Production Scrap at NPE2024
A collaboration between show organizer PLASTICS, recycler CPR and size reduction experts WEIMA and Conair recovered and recycled all production scrap at NPE2024.
Read More