Advances in Dry-Cut Strand Pelletizing, Centrifugal Drying
At K 2022 in October, MAAG debuted three products for dry cut strand pelletizing and a new centrigual dryer for underwater pelletizing.
At K 2022 in October, MAAG debuted three products for dry cut strand pelletizing and a new centrigual dryer for underwater pelletizing. Compared to its PRIMO S iteration, MAAG’s Primo SI has a new base frame that reportedly simplifies the integration of downstream equipment and machine handling. With the open design, the area under the machine is completely visible and accessible from all sides. The cutting head — as a unit with the base plate, drive and sound insulation hood now — now sits directly on four custom-made vibration dampers. As a result, the entire cutting head (including attachments) is completely decoupled from the base frame. In addition to the base frame, the acoustic hood has also been revised: narrower and with a slope in the front section. As a result, the entire machine looks slimmer and the noise level is further reduced.
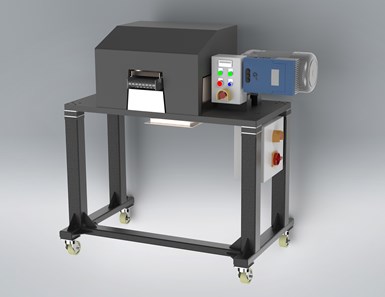
Photos: MAAG
The granulator is driven by an intelligent gear motor with integrated frequency converter and mini-PLC. This combination achieves optimum performance with extended technical features. In addition to various transfer signals and country-specific certificates, the drive comes with a Bluetooth interface that allows the operating parameters of the machine to be read live at any time.
Second, MAAG showed a strand pelletizing system for highly filled, hydroscopic and water-sensitive compounds. The EBG model reportedly offers a high degree of automation, gentle material processing and excellent product quality. From the die head to the granulator, the pelletizing system forms a unit that, despite its compact design, has features of a large compounding system. Automatic feeding in case of strand breaks, removal of melt residues on the die plate by the patented hot-air-knife and synchronization between conveyor belt and strand granulator to name a few.
Finall in strand-cut pelletizing, MAAG showed an AR model of a jet-stream JSG900 pelletizing system.
For pellet drying in underwater applications, MAAG’s eXso centrifugal dryer now includes additional features that were developed to increase reliability, reduce changeover time and improve product quality. A defining feature is its three-door housing, which allows greater access and visibility to the interior of the unit. This allows for faster and more effective cleaning and lowers the risk of cross-contamination. In addition, eXso required 23% less floor space compared to centrifugal dryers of similar capacity.
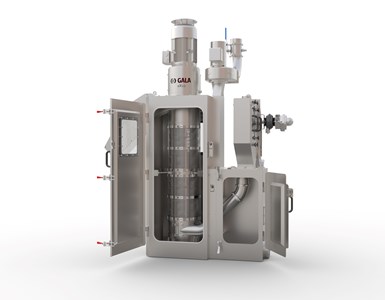
eXso centrifugal dryers are billed as ideal for compounders and recyclers that require a reliable pellet drying step prior to packaging. eXso dryers have been tested and validated for rates up to 8200 kg/hr. For a given throughput rate, the electric motors are optimized to provide the most efficient use of power.
Related Content
-
More Than a Compounder: They Have the Science to Create New Custom Materials
Insight Polymers & Compounders leverages its expertise in polymer chemistry to develop next-generation materials.
-
Configuring the Twin Screw Extruder: Part 4
For many compounding operations, material is fed to the extruder at the feed throat. This is the case when feeding a single polymer or a blend of polymers mixed with solid additives. Some ingredients, however, present a challenge in feeding. Here’s how to solve to them.
-
Improving Twin-Screw Compounding of Reinforced Polyolefins
Compounders face a number of processing challenges when incorporating a high loading of low-bulk-density mineral filler into polyolefins. Here are some possible solutions.