Blender Built for Hard-to-Handle Materials
NPE2024: New series targets application using recycled materials. Quick-change feeder also debuts.
Movacolor has added the 20-recycling series to its MBS blender range, specifically targeting plastics processors working with recycled material in their production processes. This blender is capable of processing hard-to-handle materials such as PCR, flakes and certain regrinds.
The material hopper oscillators ensure optimal flow of the material while the isolated upper body filters vibrations to ensure high dosing accuracy. Optionally, the material hoppers can be equipped with bridge-breakers to prevent material blocking or bridging. Like the regular Movacolor 20-series, this blender is characterized by its intuitive controller, robust design, and absence of mechanical parts and cables in the material hoppers. This enables easy accessibility for cleaning, material changes and other routine tasks.
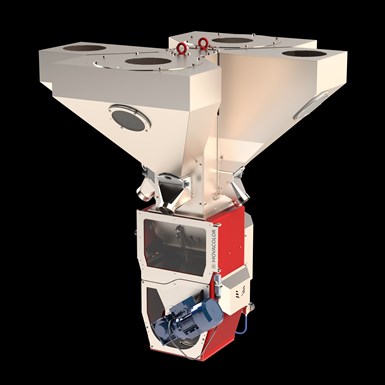
The MBS Blender 20-recycling series (photo) can be upgraded to a MHBS Hybrid blending system for optimal control over critical or expensive additives. This hybrid system combines gravimetric blending and dosing in one integrated system.
Movacolor is also taking the wraps off the MDS Volumetric Feeder, developed for plastics manufacturers that require a high-performing dosing unit at a cost-effective price. The unit has a new intuitive touchscreen in combination with the latest control software technology, which Movacolor says make it unique.
Thanks to an intuitive design, this dosing solution enables a swift 60-second cleaning and material change through a discharge valve and easy motor, hopper and dosing tool release. As a result, downtime and changeover time can be minimized.
The MDS Volumetric Feeder is part of Movacolor's modular dosing concept and can be combined with other units, as well as specifically tailored to fit the requirements of different production processes.
Related Content
-
How to Effectively Reduce Costs with Smart Auxiliaries Technology
As drying, blending and conveying technologies grow more sophisticated, they offer processors great opportunities to reduce cost through better energy efficiency, smaller equipment footprints, reduced scrap and quicker changeovers. Increased throughput and better utilization of primary processing equipment and manpower are the results.
-
Safety, Recycling, and Compounding Trends Bring New Opportunity to 70-Year-Old Company
NPE2024: Vac-U-Max presents pneumatic conveying solutions for powdered materials.
-
Processors: Gear Up to Handle More Regrind
Plastics auxiliary and primary processing equipment was optimized for running pellets; here’s how you can adjust to the bulk density differences of flake and regrind in drying, conveying, mixing, feeding and processing.