Fakuma: Engel to Debut New Hybrid Machine
Building out its e-speed range of high-speed injection molding machines with a fully electric clamp, Engel will debut the e-speed 420/90 at Fakuma.
Engel will introduce the latest addition to its e-speed line of hybrid injection molding machines at Fakuma 2021 (Oct. 12-16; Friedrichshafen, Germany; Hall A5, stand 5204), debuting the e-speed 420/90. Featuring all-electric clamping and an energy recovery system, the e-speed line ranges in clamp force from 380 to 650 tons, with Engel billing the presses as the company fastest injection molding machines with injection speeds of up to 1200 mm/sec. The energy recovery system works by absorbing braking energy from the platen movements and returning that stored energy to the motor.
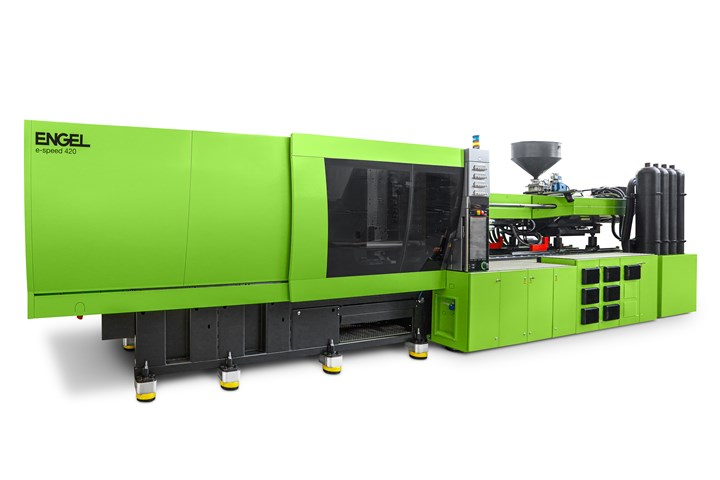
At Fakuma 2021, Engel will be unveiling the e-speed 420
At Fakuma, the newest e-speed will pair the company’s coinmelt injection compression molding with a stack mold to produce a thinwall, in-mold labelled (IML) margarine tub. The containers, which have a wall thickness of 0.4 mm (including the label), will be removed from the 4+4-cavity stack mould via high-speed, side-entry automation and stacked on a discharge conveyor following camera-based quality control. Corporate partners at the trade show will be MCC Verstraete, Plastisud, Campetella, Mevisco and Borealis. An Engel spokesperson told Plastics Technology that the polypropylene (PP) supplied for the tubs from Borealis, features a melt flow index of 70.
In a release, Engel stated the continuing push to reduce wall thicknesses is leading to more and more extreme flow path/wall thickness ratios, which can now range to 1:400. Engel notes that anything from 1:300 and above, requires injection compression molding to satisfy quality demands. Injection compression can lower required clamping forces and injection pressures, compared to conventional molding, while allowing high-viscosity materials to be processed in a repeatable fashion.
Engel says the e-speed’s electrically driven clamping unit and the toggle lever design facilitate fast, short compression strokes, making use of a stack mold possible. For the tubs, the compression stroke is only 4 mm.
MCC Verstraete supplied the interactive labels for the tubs, which utilize Digimarc technology. Like a QR code, Digimarc codes can be scanned with any smartphone camera, and they extend invisibly over the entire label surface. Camera can scan any point, and the codes do not interfere with the packaging design. Also made from PP, the labels and the tubs can be recycled together at end of life.
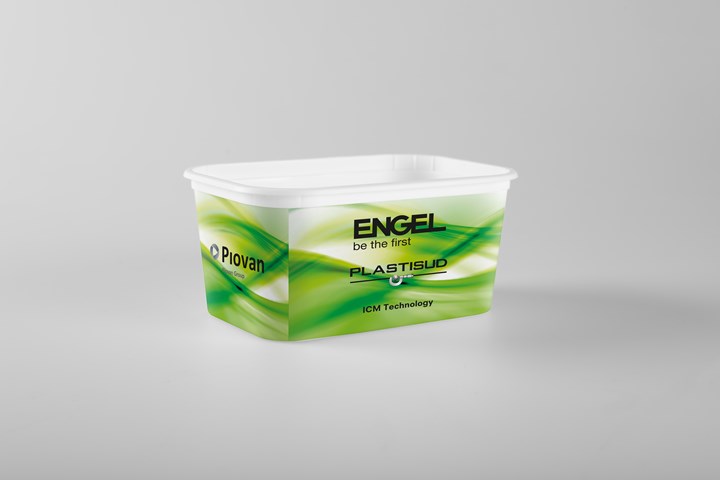
The food containers have a wall thickness of 0.4 mm including the label.
Labels Second Life as a Closure
Also at its stand, Engel will showcase how such labels can get new life by molding reground waste label offcuts from production into new tapered closures from an 8-cavity tool. An Engel victory 460/80 will be used to mold the closures for Pöppelmann, a German-based company working to establish a circular economy for the plastics industry. Pöppelmann’s KAPSTO product range are made from 100% recycled material.
Related Content
-
US Merchants Makes its Mark in Injection Molding
In less than a decade in injection molding, US Merchants has acquired hundreds of machines spread across facilities in California, Texas, Virginia and Arizona, with even more growth coming.
-
‘Monomaterial’ Trend in Packaging and Beyond Will Only Thrive
In terms of sustainability measures, monomaterial structures are already making good headway and will evolve even further.
-
For Extrusion and Injection-Blow Molders, Numerous Upgrades in Machines and Services
Uniloy is revising its machinery lines across the board and strengthening after-sales services in tooling maintenance, spare parts and tech service.