High-Temperature-Resistant Plastic Targets Electric Vehicle Applications
Freudenberg Sealing Technologies says its injection-moldable thermoplastic withstood an applied flame with a temperature of 1,200°C for more than 25 minutes.
Share
Read Next
As it seeks to improve fire protection in electric vehicle drives, Freudenberg Sealing Technologies has developed a material called Quantix Ultra, which can resist melting even at temperatures of up to 1,200°C. The company says the thermoplastic based on grades of polyketone (PK) and polyetheretherketone (PEEK) can be processed via injection molding, and it has a lower density compared to metallic materials. Freudenberg further notes that the first series application — a flame protection barrier for cooling system parts in an electric car’s lithium-ion battery — will be used for the first time by a car manufacturer in series production vehicles in February 2024.
Freudenberg says Quantix Ultra represents a new material class that can withstand very high temperatures without melting or igniting. In laboratory tests, a 2-mm-thick material sample resisted an applied flame with a temperature of 1,200°C for more than 25 minutes.
Additional tests simulating the emission of hot particles under high pressure were also conducted, with Quantix Ultra withstanding the stress test for 20 seconds. Comparatively, a 2-mm-thick aluminum sample only took two or three seconds to be destroyed.
Freudenberg notes that once the glass transition temperature is reached for a thermoplastic, its rigidity decreases and then collapses when the melting point is exceeded. Quantix Ultra, however, doesn’t melt at high temperatures; instead, it exhibits elastic behavior comparable to elastomers, with a glass transition temperature that is 53 Kelvin higher than other PEEK-based grades. In terms of processing, a Freudenberg spokesperson told Plastics Technology that PK’s melting temperature is about 220°C with a barrel temperature of 230-240°C; while PEEK molds with a barrel temperature of 350-400°C.
Additional crosslinking of the plastic molecular chains — brought about by introducing a special crosslinking agent during injection molding — ensures that the component maintains its shape even under extreme conditions. Freudenberg says material properties can be adjusted with a focus on the specific application, which is part of its patented technology.
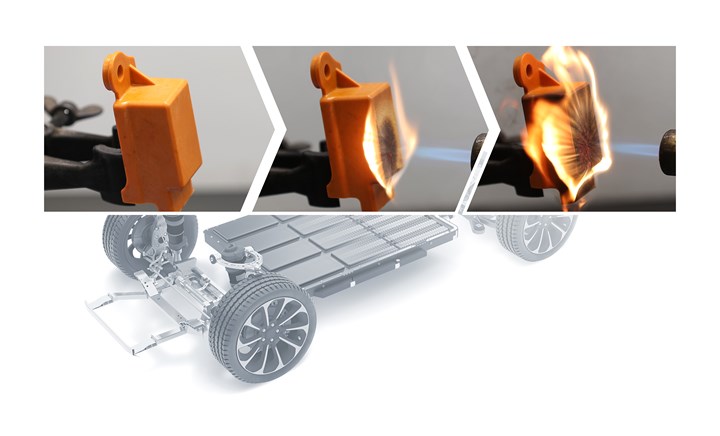
Freudenberg Sealing Technologies says its Quantix Ultra material has withstood extreme temperature testing. Photo Credit: Freudenberg
Related Content
-
Medical Tubing: Use Simulation to Troubleshoot, Optimize Processing & Dies
Extrusion simulations can be useful in anticipating issues and running “what-if” scenarios to size extruders and design dies for extrusion projects. It should be used at early stages of any project to avoid trial and error and remaking tooling.
-
Impacts of Auto’s Switch to Sustainability
Of all the trends you can see at NPE2024, this one is BIG. Not only is the auto industry transitioning to electrification but there are concerted efforts to modify the materials used, especially polymers, for interior applications.
-
Medical Molder, Moldmaker Embraces Continuous Improvement
True to the adjective in its name, Dynamic Group has been characterized by constant change, activity and progress over its nearly five decades as a medical molder and moldmaker.