Pine Tree Plant-Based Titanate Cuts Through Supply-Chain Concerns
New product from Kenrich relies on pine tree as an oleic acid raw material source because it is widely available and eliminates any supply logistics concerns.
Kenrich Petrochemicals has announced that Ken-React KR PTOA, a plant-based pine tree oleic acid titanate, is available for R&D sampling.
The material was originally conceived as a dispersant for zinc oxide (ZnO) in naphthenic oil and mineral fillers in polyolefins. Kenrich says applications for this coupling agent have expanded to thermoplastic color concentrates; increased strain energy of golf balls; dispersion of TiO2 and ZnO in cosmetics; finer and more uniform cell structure of exothermic and endothermic foaming agents; comonomer for inks; -17ºC cold temperature PVC flexibilizer; increased adhesion of acrylic to slate; carbon black dispersant for photocopy toner; PE and PET resin catalyst; and more.
“There is market pressure to use domestic plant derived from sustainable materials,” says Sal Monte, Kenrich owner and president who invented the product. “We chose the American pine tree as an oleic acid raw material source for our new titanate as it is widely available and eliminates any supply logistics concerns. For example, there has been an increase in U.S. lumber supply throughout the first five months of 2023 that has caused lumber prices to drop closer to pre-pandemic levels.”
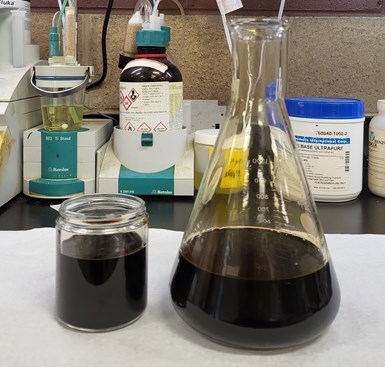
Monte is hopeful the new coupling agent with a 95% “bio-content” will gain commercial traction: “Typical PMN (premanufacturing notice) evaluation times for a final determination are taking about 12-14 months. Now that we have cleared the initial U.S. EPA TSCA submission acceptance hurdle, we are free to sample the trade for ‘R&D purposes only’ to test for commercial efficacy.”
As Monte explains, titanates “are the secret sauce that functionalize inorganics and organics at the atomic nano-interface to create new and novel compositions such as longer lasting lipstick or more powerful explosives, and thousands of other patented applications enabling more efficient use of raw materials.”
When used in polymers, Monte says titanates increase adhesion; improve impact strength and mechanical properties; reduce embrittlement; enable higher filler loadings; optimize particulate dispersion; increase flow of filled and unfilled polymers at lower process temperatures; prevent phase separation; and may have other effects.
Related Content
-
Masterbatches Reduce Gloss in PLA and PETG 3D Printed Products
Insight Polymers & Compounding’s two low-gloss additive masterbatches shown to boost appearance of 3D printed objects.
-
PFAS-Free Processing Aid for Blown Film Extrusion
Ampacet’s new processing aid said to perform as well as fluoro-based PPAs in blown film.
-
At NPE2024, Follow These Megatrends in Materials and Additives
Offerings range from recycled, biobased, biodegradable and monomaterial structures that enhance recyclability to additives that are more efficient, sustainable and safer to use.