PVA Removal Station Reportedly Enables Post-Processing of Parts Four Times Faster
The PVA Removal Station is universal in use and will be available in the first half of 2022.
Ultimaker announced during its inaugural bi-annual Showcase event that it will be adding a professional PVA Removal Station to its Ultimaker Platform. The company claims that the PVA Removal Station means that 3D printers can develop prototypes faster, and users will be able to bring their products to market more quickly, speeding up the overall product development process.
3D printers that use PVA, or PolyVinyl Alcohol, as a support material require post-processing to remove it. This is generally achieved by dissolving the PVA for a long period of time in water. Depending on the size, complexity of the design and density of the support structure, this process can take more than a day to complete. Ultimaker’s PVA Removal Station reduces this time by up to 75%. It also reduces the operating time, as operators no longer have to remove PVA manually or need to check the dissolving process.
The Ultimaker PVA Removal Station is said to be easy to use, clean, and maintain. Filled with 13.5 liters of water to dissolve PVA, its circulation direction will change automatically and the speed can be adjusted as needed. It comes with a basket and divider to fix prints and to keep them submerged. The saturation indicator shows if water needs changing, and the transparent container allows for a quick view on the dissolving process. The PVA Removal Station is universal in use and will be available in the first half of 2022.
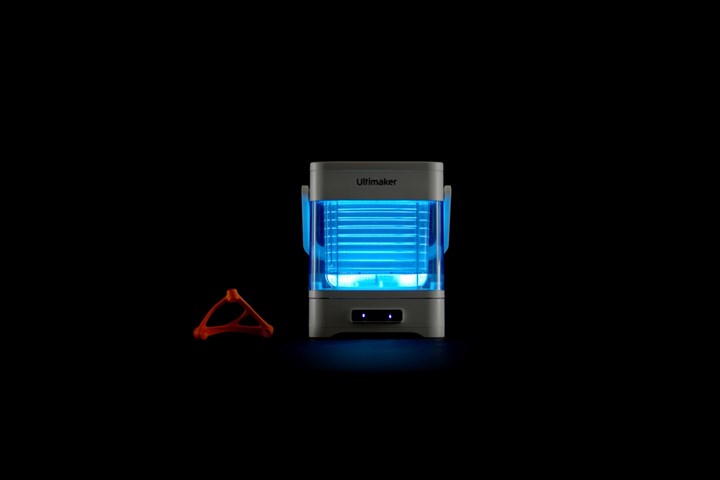
The PVA Removal Station enables 3D printer users to develop products faster by allowing quick and effective elimination of support material.
Related Content
-
DuPont Buys Medical Product Manufacturer Spectrum Plastics
Purchase price of $1.75 billion for leading supplier of extruded, molded, and 3D printed medical components.
-
3D Printed Spine Implants Made From PEEK Now in Production
Medical device manufacturer Curiteva is producing two families of spinal implants using a proprietary process for 3D printing porous polyether ether ketone (PEEK).
-
NPE 2024: Additive Manufacturing Assisting, Advancing Plastics Processing
Exhibitors and presenters at the plastics show emphasized 3D printing as a complement and aid to more traditional production processes.