Custom Injection Molder Plugs into All Electric Machines
Formerly a showroom for early-aughts-era Van Dorn hydraulics, the newest additions to Drummond Industries’ transforming fleet are all-electric Niigata injection molding machines.
The rebuilt Evel Knievel motorcycle that greets visitors to custom injection molder Drummond Industries’ facility is far from the only piece of machinery salvaged and resurrected by the father son team — both named Matt Gieser — who own and operate the company along with co-founder Steve Loerop — known as Uncle Steve by Matt Jr. who rebuilds juke boxes in his spare time.
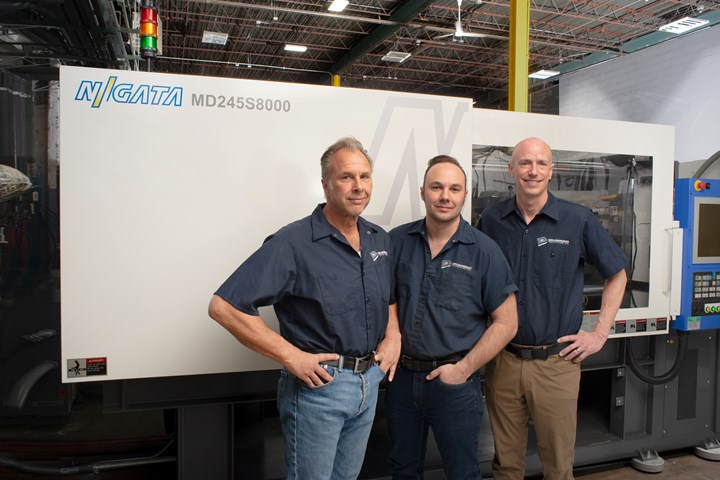
Matt Gieser Sr., Matt Gieser Jr., and Steve Loerop (left to right) stand in front of Drummond Industries' first all-electric injection molding machine, a 245-ton MD245S8000 from Niigata.
Photo Credit: Niigata
As the saying goes, if it ain’t broke don’t fix it, or historically in the case of Drummond, if it’s a Van Dorn HT that just needs some TLC, give us a call. “Molders just call me,” the Matt Sr. says, “ and ask ‘Want a Van Dorn?’”. Started on the northwest side of Chicago at Cicero and Fullerton in 1968, Drummond moved to Bensenville and a stone’s throw from O’Hare in 2015.
For years, Drummond had relied on traditional hydraulic machines ranging in clamp force from 35 to 500 tons to produce a diverse array of parts for the transportation, packaging, POP and other markets. This changed about three years ago, when Matt Jr. realized that investing in all-electric machines would enable the company to pursue new business opportunities molding much smaller components. The company investigated multiple all electric machine platforms, but it was a visit to a local molder the Gieser’s knew with Niigata’s that turned Drummond on to the the Japanese-made machines.
After meeting with Greg Lewis, Niigata Regional Sales Manager, and Steve Cunningham, general manager for Niigata USA’s injection molding division, Drummond made its first order for a 245-ton Niigata MD245S8000 press.
Synchronized Movements
Among the features of Niigata’s MDS8 all-electric that stood out to Matt Jr. were its simultaneous motion capabilities that allow the machine to perform several actions in tandem, such as part ejection during clamp opening; melt metering during mold movement; and clamp relaxing during mold cooling. These synchronous functions ultimately reduce overall cycle time without impacting injection or cooling speeds. With this key feature, Drummond could mold more parts in less time, enabling them to complete one job and then move on to the next, quickly and easily.
As a custom molder, Drummond changes jobs and molds multiple times per day, so the speedier changeovers are a major selling point. While the same process settings could have different outcomes on their hydraulic machines, their repeatability with the electric machines was much higher.
“With the servo technology, the molds are going to run the same,” Matt Jr. says. “The machine is telling us exactly how much voltage to inject at, etc. etc. and that’s been huge. Literally, it’s plug and play once we get a mold in.” In addition, the Niigata machines offer automatic mold height adjustment and lock up, as well as low-pressure safety. Drummond recently purchased a second 245-ton machine and will be adding a smaller all-electric from Niigata later this year.
“I’d be hard pressed to buy another hydraulic machine unless they were literally blowing the dust off of it and it’s got zero hours,” Matt Sr. says. Father and son both stressed that as nice as new technology is, it is Drummond’s team, many of which moved with them from the old Cicero location and now includes Matt Jr.’s cousin, that have kept the company growing over five decades.
“We have a very old phone number and a very good name in the industry,” Matt Sr. says. “We’ll be here for people. We sit across this table and it’s like, ‘Thank god somebody’s listening to us.’ If you call you’re going to talk to one of three people: Steven, my partner; my son; or myself.”
Related Content
Online X-Ray Inspection Boosts Extrusion Quality
Höhle uses Sikora’s x-ray measuring systems for inline quality control of extruded microducts.
Read MoreNew CRM Streamlines Quoting for Automotive Molder
Eliminating the need to contact each supplier for every individual quote, a new CRM for automotive supplier Axiom Group tracks past quotes as well as industry history to generate fast, reliable RFQs and more.
Read MoreNovel ‘Clamtainer’ Extends Thermoformer's Reach in Packaging
Uniquely secure latching expands applications for Jamestown Plastics’ patented clamshell package design.
Read MoreSecondary Injection Unit Provides Primary Benefits for Molder
Core Technology Molding turned to Mold-Masters E-Multi auxiliary injection unit to help it win a job and dramatically change its process.
Read MoreRead Next
Niigata Fills New Regional Sales Manager Role
Gregory Lewis will occupy the new position created after the injection molding machine supplier began direct sales in the U.S. in 2019.
Read MoreQuick-Change Shot Sizes for Injection Molding
Niigata will debut the patented Shot Maker technology at the PTXPO (March 28-30; Chicago), allowing molders to quickly change a press’s shot size by swapping out the barrel’s stroke section.
Read MoreLead the Conversation, Change the Conversation
Coverage of single-use plastics can be both misleading and demoralizing. Here are 10 tips for changing the perception of the plastics industry at your company and in your community.
Read More