Injection Molder Sees Huge Growth in Recycling
Wittmann Battenfeld's material-handling systems and engineering support helped Monoflo International reprocess more than 60 million lb of plastics over 10 years.
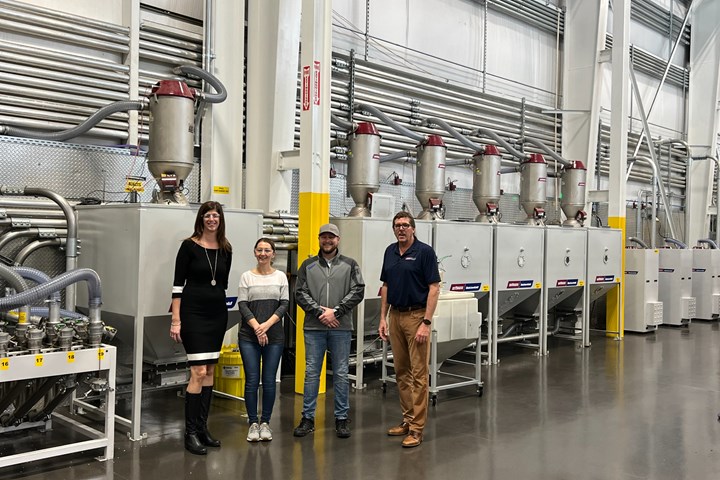
Left to right, Wittmann Battenfeld's Crystal Gagnon; Monoflo's Ashly Hawkins and Calvin Wetzel; and Wittmann Battenfeld's Brent Strawbridge. (Photo: Wittmann Battenfeld)
Injection molder Monoflo International, Winchester, Va., which makes totes, bins, pallets and other packaging for the likes of CVS, General Motors and Amazon, continues to up its game in reprocessing.
The company’s first foray into recycling was in 2010, and since then Monoflo has worked to perfect the process. Today, Monoflo’s reprocessing business is booming; the molder runs two highly automated lines with a total of 5000 lb/hr capacity (plus another 1000 lb/hr capacity at a plant in Ottawa, Kan.). To keep up with demand growth, Monoflo has added new buildings, new equipment and new technology. And the company says it is just getting started.
“It took several years to perfect the most efficient way to run this repro operation,” says Ashly Hawkins, operations manager at Monoflo. “Now we have a proven system in place that can reprocess 12 million to 15 million lb of material per year.” The company has reprocessed over 60 million lb of plastics in the past 10 years.
When Monoflo first got into reprocessing, it called on a familiar name for support: Wittmann Battenfeld, which for years had supplied robots and material-handling systems to the molder.
“Monoflo reached out to us back in 2011 asking for our advice,” recalls Steve Mussman, division manager—material handling & auxiliaries at Wittmann Battenfeld. “They told us they wanted to develop a recycling system that could shred used tote bins, reprocess the materials and reuse the material in new molded bins.”
“We have a proven system in place that can reprocess 12 million to 15 million lb of material per year.”
Wittmann Battenfeld worked with Monoflo to design a system that shreds and conveys the reprocessed material to the designated silo or building. It is furnished with a pressure-conveying system to continuously batch, weigh, record and convey reprocessed material from the reprocessing line to any designation silo within the system, which was dubbed the “Totalizer.” The system has a series of diverter/isolation valves, sensors, weigh hoppers, surge-capacity bin, pressure pump, silos, and silo level confirmation—all supplied by Wittmann.
Since 2012, with Wittmann’s help, Monoflo has made continuous improvements to the line and now runs two Totalizer lines in Winchester. A line that began with 1000 lb/hr capacity at startup in 2012 now processes over 3000 lb/hour of HDPE, PP, and structural-foam parts.
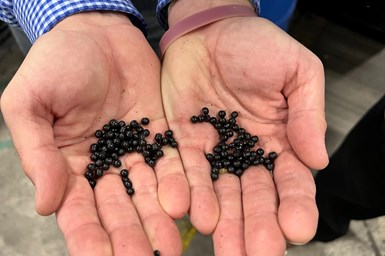
Reprocessed pellets made from ground-up totes and bins.
Systems in Place
Monoflo also has three Wittmann M7 control systems managing material handling in its main building; a fourth system is being installed this year, and another one is being added to a new building in 2022.
“Over the years Monoflo has asked us to work with them to continually improve the material handling aspect of their injection molding and reprocessing operations,” Mussman says. “We’ve helped with adding silos to replace storage bins, moving the repro material from the buildings to the silos, and implementing a railcar unloading system to move material from the silos to other parts of the facility. We’ve provided the know-how and advice to help Monoflo lay out it’s reprocessing operations for the highest efficiency.”
In addition to the Wittmann equipment, Monoflo uses Weima and Vecoplan shredders, a Herbold float/sink tank, and four Erema pelletizing systems to clean and repelletize the reclaimed plastic.
“Lately, the high cost of virgin resin has led to increased customer demand for more repro.”
Recycling Market
Monoflo’s reprocessing operation involves buying back used or end-of-life containers from its customers, regrinding and reprocessing the material, and reintroducing the materials into newly molded containers. “The market for recycled and reprocessed resin continues to grow,” states Hawkins. “The demand for these materials comes from our customers, but we also have made it part of our mission to encourage the industry to increase its recycling. Lately, the high cost of virgin resin has led to increased customer demand for more repro,” she said.
A major challenge for the business is to keep a steady stream of scrap products coming in, notes Calvin Wetzel, extrusion supervisor at Monoflo. “We get most of our scrap from our customers, but we also source it from other suppliers,” he says. “We need to vet the scrap that we receive to make sure it doesn’t include products or materials we can’t use.”
The importance of controlling the entire reprocessing in-house at Monoflo is critical, according to Wetzel. “We know the source of our materials and can maintain control over, and ensure the quality of, the reprocessed resin.”
Related Content
Automotive Awards Highlight ‘Firsts,’ Emerging Technologies
Annual SPE event recognizes sustainability as a major theme.
Read MoreScaling Up Sustainable Solutions for Fiber Reinforced Composite Materials
Oak Ridge National Laboratory's Sustainable Manufacturing Technologies Group helps industrial partners tackle the sustainability challenges presented by fiber-reinforced composite materials.
Read MoreExtrusion Technology Extended to Injection, Enabling Up to 100% Regrind Usage
Twin-barrel (shot-pot) press can handle more regrind, offers other benefits to molders.
Read MorePurpose-Built System Enhances Capacity and Flexibility for Recycler
A Boston recycler invested in a turnkey shredding, granulation and elutriation system to expand its plastics reclaim business.
Read MoreRead Next
For PLASTICS' CEO Seaholm, NPE to Shine Light on Sustainability Successes
With advocacy, communication and sustainability as three main pillars, Seaholm leads a trade association to NPE that ‘is more active today than we have ever been.’
Read MoreLead the Conversation, Change the Conversation
Coverage of single-use plastics can be both misleading and demoralizing. Here are 10 tips for changing the perception of the plastics industry at your company and in your community.
Read More