Italian Machine Builders Bandera, Macchi Running Film Lines
Five layer lines running all polyethylene as part of sustainability push.
Italian machine builders Luigi Bandera and Macchi are bucking the trend among suppliers of blown film machinery by running production lines during NPE2024.
In the case of Macchi, NPE2024 marks the first time ever it will run a line at a show outside Europe. The machine builder, which recently opened a new office in the U.S. in Charlotte, N.C., will operate its 5-layer TechnoFlex line in Orlando May 6-10, running a variety of polyolefin-based structures for shrink film, lamination, printing and gusseted film.
At the show, Bandera will be running a thickness from 20 to 200 μm at output rates of 880 lbs/hr. The line was shipped to the show after it debuted at an open house in January at Bandera’s headquarters in Busto Arsizio, Italy (near Milan). It will be available for sale right from the show floor, says Mattia Gambarotto, general manager of Bandera’s North American operation.
While builders of injection molding and blow molding machinery conventionally operate machines at trade shows, many manufacturers of extrusion lines have trended toward static displays — in particular at NPE, but of late at the K Show as well — due to cost, line size and complexity, more restrictive ceiling heights, potential processing complications and numerous other factors.
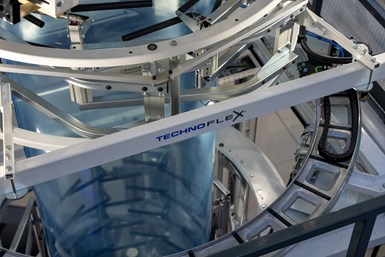
Bandera, however, decided to invest in running an actual blown film line at the show as a means to demonstrate its commitment to the North American market, Gambarotto notes. “Compared to other European suppliers of blown film technology, our decision to invest in the North American market came a little later, so we feel that demonstrating our capabilities at a show like NPE is important given our new organization in North America and our plan to increase brand awareness,” he says.
The line features a 20-component gravimetric dosing system with an automatic cleaning system; 5 extruders (one 85 mm; the other four 65 mm); a 5-layer 300-mm coextrusion die head with IBC; a high-efficiency dual-lip air ring; automatic film thickness control; flattening and gusseting devices; calibration cages; an oscillating haul-off, 1,800-mm roller width; the company’s Trim Flex edge-reclaim system; a two-station face-to-face winder featuring contact/axial winding modes with automatic reel extraction; and a complete tower frame. The line is designed and supplied on 480-volt components.
Says Gambarotto, “Nowadays when someone purchases a blown film line and invests millions, they want to be sure not only about the technology but also about the company they are buying from, how strong it is, how committed they are to the market. We’re confident that what we will be demonstrating will be interesting to the audience and also be positive for Bandera.”
Meantime, Bandera’s new 6,000-square-foot facility in Charlotte will house sales, spare parts and service support.
Macchi has run lines at the last several NPEs. This week, it’s running a 5-layer polyolefin-dedicated line featuring 5 extruders; a continuous flow hydraulic screen changers to better accommodate the introduction of reclaim; a triple-flow air ring with and integrated automatic profile control system; a wax drainage system for the air ring; a frost line scanner; a smoke suction system on bubble guide; a Centro Freeze supporting basket with cooling function; a double station automatic winder; and an inline system for side trim recovery.
What’s more, the line is furnished with Macchi I.o.T., a digital solution that performs OEE monitoring, breakdown analytics and predictive maintenance to verify production efficiency in real time. Also in action is the Macchi W.i.S. (Web Inspection System), an innovative solution for film defects mapping.
Related Content
Inside the Florida Recycler Taking on NPE’s 100% Scrap Reuse Goal
Hundreds of tons of demonstration products will be created this week. Commercial Plastics Recycling is striving to recycle ALL of it.
Read MoreProcessing Megatrends Drive New Product Developments at NPE2024
It’s all about sustainability and the circular economy, and it will be on display in Orlando across all the major processes. But there will be plenty to see in automation, AI and machine learning as well.
Read MoreThe Importance of Mass Balance in Chemical Recycling
Approaches to mass balance can dramatically impact calculations of recycled content.
Read MoreScaling Up Sustainable Solutions for Fiber Reinforced Composite Materials
Oak Ridge National Laboratory's Sustainable Manufacturing Technologies Group helps industrial partners tackle the sustainability challenges presented by fiber-reinforced composite materials.
Read MoreRead Next
People 4.0 – How to Get Buy-In from Your Staff for Industry 4.0 Systems
Implementing a production monitoring system as the foundation of a ‘smart factory’ is about integrating people with new technology as much as it is about integrating machines and computers. Here are tips from a company that has gone through the process.
Read MoreFor PLASTICS' CEO Seaholm, NPE to Shine Light on Sustainability Successes
With advocacy, communication and sustainability as three main pillars, Seaholm leads a trade association to NPE that ‘is more active today than we have ever been.’
Read MoreSee Recyclers Close the Loop on Trade Show Production Scrap at NPE2024
A collaboration between show organizer PLASTICS, recycler CPR and size reduction experts WEIMA and Conair recovered and recycled all production scrap at NPE2024.
Read More