Molder Eliminates Line Blowouts with Deflection Elbow
Parker Chomerics eliminated chronic elbow failures since switching to Hammertek conveying elbow more than two-and-a-half years ago.
Parker Chomerics, a division of Parker Hannifin’s Engineered Materials Group, based in Fairport, N.Y., injection molds electrically conductive components for automotive, electronics and telecommunications. These components provide electromagnetic interference (EMI) shielding and replace metal assemblies to save weight and cost. However, glass fibers that contribute to the exceptional physical properties of one new resin also caused it to repeatedly wear through sweep elbows of the company’s pneumatic conveying system.
The resins used in the molding process—both electrically conductive and nonconductive—are formulated with additives such as carbon fiber, glass fiber, nickel or stainless steel. Some are produced on-site, while others arrive in bulk trucks and are conveyed pneumatically to 25-ft-tall outdoor silos. Each line requires two 90° elbows; a 4-in.-diam pneumatic line is routed vertically up the side of each silo, horizontally for 6 ft, and then down to a silo top inlet connection.
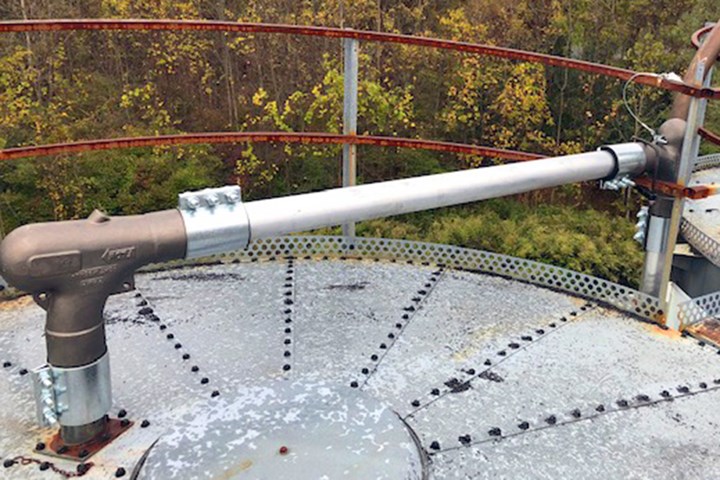
At Parker Chomerics, two 90° deflection elbows from HammerTek eliminated elbow wear previously experienced with stainless-steel sweep elbows, ceramic-lined elbows, ceramic-backed elbows, and elbows fabricated in-house using flexible stainless-steel pipe and quick-connect fittings.
In 2015, a new pelletized mineral/glass-filled nylon wore holes through the elbows of the silo fill line. “After a certain number of fill-ups, resin would shoot out the top of the line and scatter all over,” says Mark Withey, maintenance supervisor. “It was a lot to clean up.”
Withey and his maintenance crew first attempted to solve the problem by switching to other types of elbows. “We started with stainless-steel sweeps, then went to ceramic-lined sweeps, and then to one with a replaceable ceramic back,” Withey recalls, describing earlier efforts to maintain the line. His crew even fashioned elbows in-house using flexible stainless-steel pipe and quick-connect fittings.
The stainless-steel sweeps, having a 12-ft-long arc, are impossible to look into or manually probe to inspect, Withey maintains. “All we could do was guesstimate.” To be safe, Withey’s maintenance team swapped them out every few months.
The ceramic-lined sweeps, which were more expensive, lasted only six months. The elbows with a replaceable back didn’t actually wear at the back, but at the corners. “We had to take them down to the shop, weld up the hole and then bring them back to the top of the silo,” Withey states.
His crew even fashioned elbows in-house using flexible stainless steel-pipe and quick-connect fittings. “They lasted four to five months and were less expensive and quicker to change out, but still time consuming,” Withey says. “Regardless, all of the elbows we tried added a great expense in terms of parts, labor and downtime.”
Deflection Elbows Prevent Impact, Wear
Withey then learned of a deflection-type elbow from HammerTek Corp. Unlike sweeps that require pellets to impact the elbow wall to change direction, the company’s Smart Elbow design features a spherical vortex chamber protruding partially beyond the material flow path, causing a loosely packed sphere of pellets, suspended in air, to slowly rotate in the direction of flow. Material entering the elbow is gently deflected around the bend by the ball of rotating material without impacting or abrading the elbow wall. Because some material is continuously replenishing the rotating ball of pellets, the process is continuous, and the chamber evacuates fully along with the final portion of material being conveyed.

The short-radius vortex design of Hammertek’s Smart Elbow features a protruding spherical chamber that causes a ball of material suspended in air to rotate, gently deflecting incoming material around the bend without impacting the elbow wall or generating heat.
In October 2018, Withey installed two deflection elbows on the line conveying the abrasive pellets, eliminating elbow failure as of this writing. “At first, we went up once a month to unbolt and inspect them,” Withey says. “Now, as we’ve become confident in them we go up quarterly.” He reports a routine inspection takes 45 min and is easier than before. “The other elbows were a lot bigger, a lot heavier and more cumbersome,” Withey says. The Smart Elbow is compact, with a radius of just 10.6 in. “One person can pick it up and hold it with no problem. It works really well for us.”
Related Content
Cut Loading Time Through Direct Charge Blending
Direct charge blender loading, a vacuum-powered automation process, can dramatically improve loading time and reduce material costs. In this article, we address ten common questions to help you determine if the systems are right for your facility.
Read MoreTechnology Aims to Smarten Up Resin Conveying
At NPE2024, Novatec moves to rewrite the rules for material conveying with patent-pending smart-pump technology.
Read MoreSafety, Recycling, and Compounding Trends Bring New Opportunity to 70-Year-Old Company
NPE2024: Vac-U-Max presents pneumatic conveying solutions for powdered materials.
Read MoreConair: Going All In on AI
Conveying with Optimizer, Conair’s new AI-based conveying technology stands to be a true game changer for plastics processors.
Read MoreRead Next
Clean Conveying Cuts Costs and Enables Efficiency
Focus on three key areas when moving material for better-quality parts and less downtime.
Read MorePP Compounder Elbows Out Production Snafus
The Plastics Group of America eliminates monthly production stoppages, improves quality, and slashes maintenance expenses by installing new elbows on a pneumatic conveying line.
Read MoreFollow These Steps to More Efficient Central Pneumatic Conveying
Depending on when you bought and installed it, there are ways to tweak your central pneumatic conveying system to improve its performance and save you some money.
Read More