Sensing Instrumentation for More Sustainable and Automated Polymer Processing
NPE2024: Dynisco solutions support move to nontoxic materials and adds feedback control capability.
Plastics processors looking for sustainability and process stability may find their way to Dynisco’s exhibition booth at NPE. The company focuses on measurement of temperature, measurement and pressure. Its customers are looking for more sustainable ways to get that data and to do more with that data to mitigate risk.
Pressure sensing in plastics processing has generally relied upon mercury. The metal’s unique properties enable it to transmit forces over a distance very repeatably. However, mercury’s inherent toxicity and propensity to bioaccumulate have inspired efforts to reduce its use as much as possible, even the small volumes used in pressure sensing.
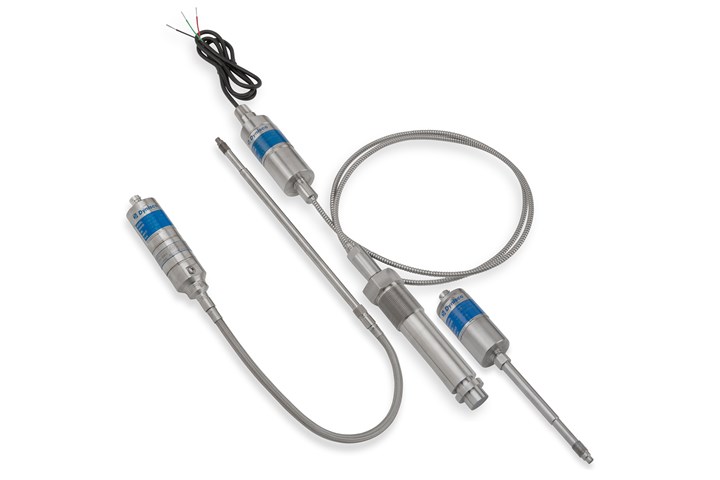
The new fill media is available on Dynisco’s SPX line of sensors. Source: Dynisco
For customers looking to make a change, Dynisco is offering a platform of pressure sensors with nontoxic fill media. The company offers four options in this space: a food-grade oil fill medium, an NaK very high-temperature medium, a capacitance sensor with no fill medium, and a new HTF (high temperature fluid) fill medium, suitable for operation up to 350° degrees, covering most uses in petrochemical processing. The new product is immediately available.
“A lot of people may not know what is in their pressure sensors,” says Bill Desrosiers, VP of sales, marketing and business development at Dynisco. “We’re really making sure they have a choice in the matter and can pick the right sensor that is best for their needs and meets sustainability.”
Melt pressure transducers are among the product categories where mercury is to be phased out under the Minamata Convention, of which the United States is a signatory, by 2025.
Automatic Feedback Control for Mixing
Dynisco will also be presenting the new capability of its Viscoindicator rheometer product. Originally introduced in 2016, the Viscoindicator measures viscosity continuously, providing data where it is needed in seconds. Now, data from the Viscoindicator can automatically feed back into feed or blending equipment.
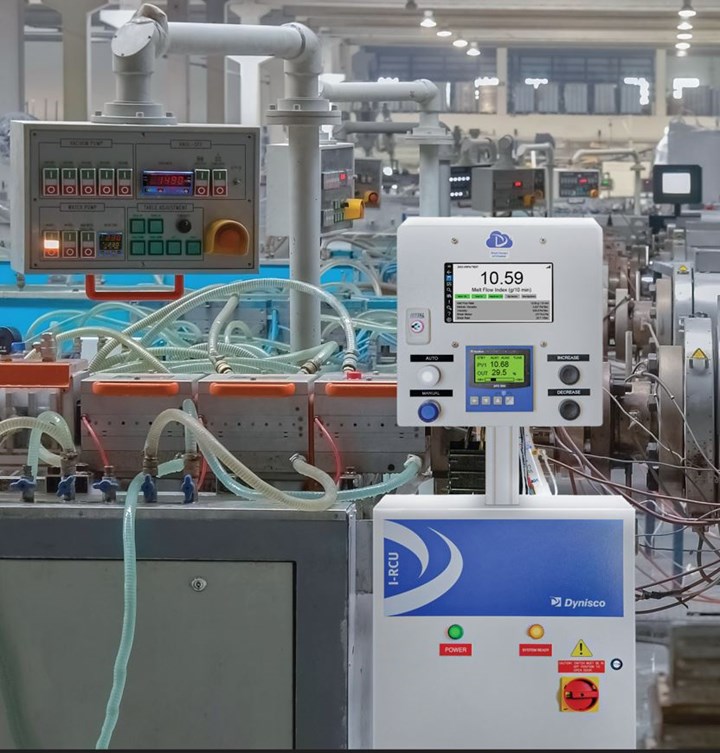
Viscoindicator now has feedback control outputs for feed and mixing. Source: Dynisco.
The Viscoindicator takes a measurement every 15 sec., which can be used to adjust the parameters of feed equipment to control the material properties and keep the appropriate balance. Dynisco will demonstrate this live at NPE2024, using two materials with different melt flow indices.
“It will automatically make adjustments based on your settings, explains Desrosiers. “If you’re a recycler and you want to change your melt flow rate and you need to add a peroxide, this can dispense that peroxide. You can blend a regrind with a virgin material to get a defined output. It’s a way to manage your extrusion process by the material itself, not through the machine, and in real-time.”
The system is compatible with any extrusion system with a existing sensor port, without modification. Dynisco expects the Viscoindicator with control will be especially useful in recycling, to provide flexibility in managing feedstock of varying properties and reduce waste.
Related Content
-
Purpose-Built System Enhances Capacity and Flexibility for Recycler
A Boston recycler invested in a turnkey shredding, granulation and elutriation system to expand its plastics reclaim business.
-
How to Optimize Injection Molding of PHA and PHA/PLA Blends
Here are processing guidelines aimed at both getting the PHA resin into the process without degrading it, and reducing residence time at melt temperatures.
-
The Importance of Mass Balance in Chemical Recycling
Approaches to mass balance can dramatically impact calculations of recycled content.