Three Wisconsin-based manufacturers combined forces to help in the fight again the global coronavirus in a partnership that continues to produce results. In October 2020, Teel Plastics, Baraboo, Wis., received a new Department of Defense contract to ramp up production of swab sticks to fight the global Coronavirus pandemic. To meet this challenge, the company needed to quickly expand its operations by adding numerous injection molding machines and move four existing extrusion lines to an all-new building. Auxiliary equipment builder AEC, based in New Berlin, Wis., and Aqua Poly Equipment Co., its Menomonee Falls, Wis., sales representative, provided a customized, turnkey central material handling and chilling system for the new building. As part of the project, Aqua Poly & AEC provided complete project management and installation services to help Teel meet the challenge by getting the new plant up and running in just four months.
Teel had been a major supplier of swab sticks used in Covid-19 test kits when it received the new DoD contract in 2020 to further ramp up its production capacity in response to the worldwide pandemic. The new contract required adding production capacity at its Baraboo headquarters, which included nine new injection molding machines and two new extrusion lines.
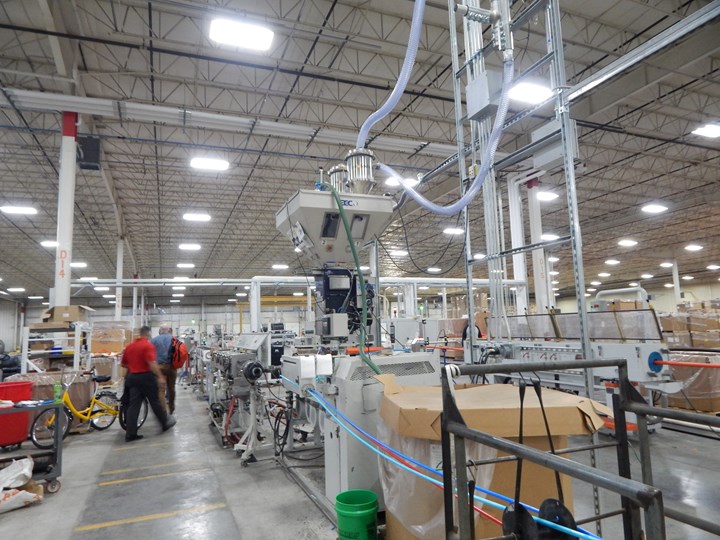
To expand Covid test swab production, Teel moved four existing extrusion lines to a new plant as part of the project with AEC and Aqua Poly. (Photos: AEC)
In order to meet the DoD contract needs, Teel management realized it needed additional space at its headquarters plant and decided to move four existing extrusion lines as part of the project. After locating a nearby facility with space for the existing extrusion lines and room for future expansion, Teel began looking for partners to help facilitate the move. The company was looking for a partner to help with planning, purchasing and installing a materials-handling and chilled-water system for the new plant. Since the new plant was acquired in October 2020 and the goal was to be in production by February 2021, it was crucial to complete the project quickly.
This is where AEC and Aqua Poly came in and proposed a custom solution for the project. After meeting with Teel to discuss the particulars of the project, AEC and Aqua Poly went to work. They teamed up to not only propose a design for the new plant’s central material-handling and water-chilling system, but they also proposed a plan to manage the installation of the new systems. This included sourcing and managing all local contractors for the project.
AEC and Aqua Poly’s solution included providing the following machinery, equipment, and services:
• Water chilling/central chilling system;
• Material handling to include railcar unloading, and conveying from railcars to silos and to the plant’s extruders (including all necessary piping);
• Bulk storage systems (silos);
• Blending systems;
• Complete installation services and project management.
A major advantage of the AEC/Aqua Poly proposal was simplifying the challenge for Teel with a solution that included total management of the project. “Our value proposition and quote were very strong,” says Pat Doyle, president of Aqua Poly. “We already had good relationships with many local contractors who we could call on to assist with the project. Plus, none of our competitors could offer the single-source responsibility that we proposed.”
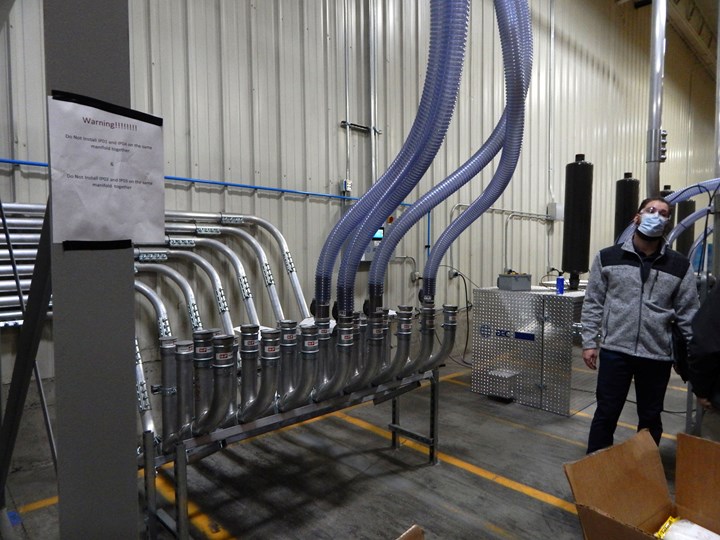
Teel installed a new material-handling system to include railcar unloading and conveying from railcars to silos and to the plant’s extruders, feeding a new blending system.
Notes Dustin Steinhorst, Teel’s maintenance manager, “Aqua Poly and AEC provided a complete package solution, which made coordinating install of our material handling and chilling system a breeze. With the tight timelines and a huge breadth of equipment to install, their partnership was vital to the success of our project. One year later, we have seen virtually no interruptions of system service. I wish all our new equipment was this reliable.”
Once Teel awarded the job to AEC/Aqua Poly, the work started immediately to meet the tight timeline. “We lived this project for four months,” recalls Doyle. “We had the resources to handle the scale of the project while providing total project management with a single point of contact for Teel.”
When assessing the project, AEC and Aqua Poly knew there were several factors that required an innovative approach. For instance, while the immediate need was to move the four existing extrusion lines and get them up and running ASAP, the new building had the capacity to accommodate eight full-size pipe extrusion lines and four to eight smaller extrusion lines, which played a key role in the design of the central materials-handling and chilling systems. The key innovations included:
• Winter Kooler: AEC provided an economizing cold-weather chiller system that uses the natural temperature difference in winter to help save electricity. While helping improve Teel’s bottom line, the new system also supports energy savings and environmental sustainability goals, which are an important part of Teel’s operating philosophy.
• Custom railcar unloading: This unusual custom system is designed to unload up to four different materials simultaneously, which dramatically reduces unloading times compared with a typical system that can only unload one railcar at a time. By adding pumps and an air lock in every silo, AEC and Aqua Poly minimized the potential costs associated with purchasing four separate large unloading systems.
• Customized silos: Aqua Poly supplied four bulk-storage silos with load cells under each silo to provide Teel with a more accurate way of measuring the material weights instead of typical volumetric point level sensors. Other custom features on the silos included discharge components, metal/angel-hair traps, and all conveying piping from the silos into the building.

Aqua Poly supplied four bulk-storage silos with load cells under each silo to provide Teel with a more accurate way of measuring the material weights instead of typical volumetric point level sensors.
“We set an aggressive timeline to get the new plant up and running,” Christian Herrild, Teel’s dir. of growth strategies. “With AEC and Aqua Poly’s help, we were successful in meeting that timeline. The facility has been operational since February 2021 and in full production since March of that year. We are now considering additional lines because of how busy we have been.” In fact, with zero service interruptions in over a year of full production, Teel has produced more than 2 billion swab sticks since March 2021.
Related Content
Understanding Melting in Single-Screw Extruders
You can better visualize the melting process by “flipping” the observation point so the barrel appears to be turning clockwise around a stationary screw.
Read MoreHow Screw Design Can Boost Output of Single-Screw Extruders
Optimizing screw design for a lower discharge temperature has been shown to significantly increase output rate.
Read MoreHow Polymer Melts in Single-Screw Extruders
Understanding how polymer melts in a single-screw extruder could help you optimize your screw design to eliminate defect-causing solid polymer fragments.
Read MoreHow to Select the Right Tooling for Pipe Extrusion
In pipe extrusion, selecting or building a complementary set of tooling often poses challenges due to a range of qualitative factors. Here’s some guidance to help you out.
Read MoreRead Next
Cumberland Granulators Works with Teel Plastics and KW Plastics to Help Meet Sustainability Goals
Cumberland Granulators division of ACS Group details the recent work they've done with Teel Plastics and KW Plastics to help them quantify the reduction of global warming potential at their plants.
Read MoreTeel Plastics Continues in Battle Against Coronavirus
Newly installed Davis-Standard extrusion lines address swab-stick demand.
Read MoreTeel Gets Government Contract for Swab Sticks
Grant will allow Teel to produce hundreds of millions more swab sticks for Covid-19 test kits.
Read More