Illig and Suedpack Collaborate on Certified Compostable, Biobased Food Containers
Made with BASF’s partially biobased Ecovio, these thermoformed containers with heat-sealable lids are especially suitable for vegetarian and vegan foods and dairy products.
We recently learned about a collaborative project between blown and cast film German manufacturer Suedpack and global thermoforming and tool systems manufacturer Illig Maschinenbau, that demonstrate that thermoformed food packaging with components that are certified compostable and predominantly biobased is possible under current market conditions.
The development, say the partners, is in keeping with the increasing trend and demand for compostable and biobased packaging solutions in more and more countries. In particular, food packaging with organic remnants is difficult to process in conventional mechanical recycling processes This makes industrially compostable containers a viable alternative where the appropriate infrastructure for composting exists. In this way, the food scraps, including the packaging, can be sent for organic recycling instead of thermal recycling.

The new tray with heat-sealable lid can be used to package vegetarian and vegan foods, as well as dairy products such as yogurt or cheese. It is predominantly made of BASF’s certified compostable (DIN EN 13432) partially biobased plastic Ecovio (a blend of BASF’s Ecoflex biodegradable aliphatic copolyester and 45% PLA), which was dyed green for this application.
Suedpack produced the film in an extrusion process and developed the laminate lidding film, which is also industrially compostable. Illig designed the thermoforming tool, thermoformed the trays from the film and sealed the lid. The result is a thin-walled food container that replicates the mold's shape in detail and can be produced at the same speed as similar packaging made from conventional plastics.
The ecovio bioplastic used for this case study has been specially optimized for film extrusion with subsequent thermoforming. It can be processed on standard mono- or co-extrusion machines into films with or without an additional oxygen barrier. The bioplastic has a high heat deflection temperature up to 95 C/203 F), is approved for contact with foodstuffs and has mechanical properties similar to those of PP.
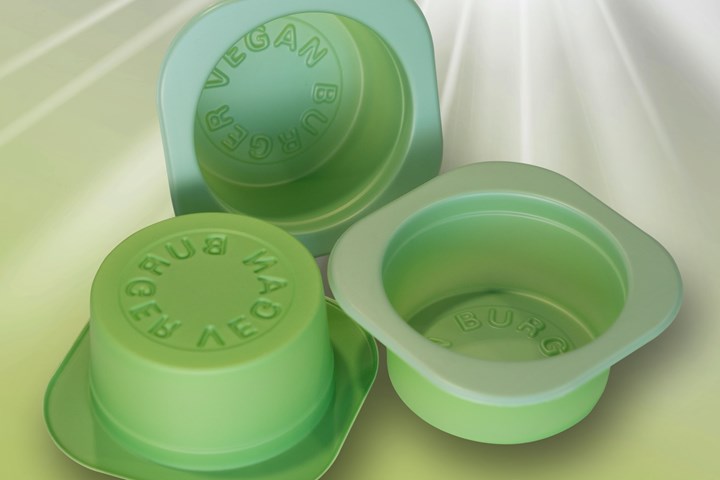
The flexible film developed by Suedpack for the lid consists of a multilayer, partially transparent laminate based on PLA and brown paper. All components are industrially compostable according to DIN EN 13432. The film is heat-sealable with other PLA-based materials and can also be optionally equipped with a barrier layer.
Said Dr. Jürgen Betz, responsible for R&D Extrusion at Suedpack, "Together with Illig, a leading global manufacturer of thermoforming and tooling systems, we were able to demonstrate that films made from Ecovio material can not only be produced effectively on common extrusion lines, but also show excellent properties when processed on thermoforming lines,"
According to Sven Engelmann, head of the Illig Technology Center and packaging development at Illig in Heilbronn, this joint project approach allowed them to demonstrate how certified compostable and biobased plastics can be easily thermoformed and further processed on standard machines. "We were able to run the same machine speed as with polypropylene. In particular, our thermoforming tool reproduces the lettering 'Vegan Burger' embedded in the bottom of the tray with great detail. This opens up numerous design possibilities for thermoformed, industrially compostable packaging."
Related Content
-
Avantium and U.S.’s Origin Materials Aim to Accelerate Production of FDCA and PEF
The partnership aims to bring together both companies’ technology platforms to produce FDCA from sustainable wood residues on an industrial scale.
-
At NPE2024, Follow These Megatrends in Materials and Additives
Offerings range from recycled, biobased, biodegradable and monomaterial structures that enhance recyclability to additives that are more efficient, sustainable and safer to use.
-
Honda Now Exploring UBQ’s Biobased Material Made from Unsorted Household Waste
UBQ is aiming to expand its reach for more sustainable automotive parts as well as non-automotive applications.