Plastic Molds for Chocolate “Molding” Formed From Aluminum Molds
Micelli Mold Co., one of a handful of chocolate mold makers globally, became one of Chinese injection molding machine maker Bole’s first U.S. customers, using its presses to mold polycarbonate chocolate molds in Long Island.
For nearly 200 years, Micelli Mold Co. (West Babylon, N.Y.) has supplied the molds chocolatiers use to shape molten chocolate into familiar shapes for some very familiar names. For six decades the chocolate molds it sold were metal, but starting in the late ‘80s, the company switched over to plastic molds that it would injection mold from aluminum tools. The use of aluminum tooling, the fact that many of these molds were created from polycarbonate and the need for flat, stable parts eventually led Micelli to Bole Machinery.
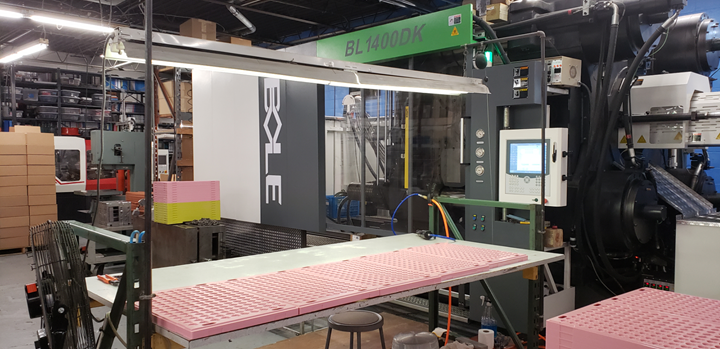
Long Island’s Micelli Mold utilizes a 1400-ton EK injection molding machine from Bole to create molds from polycarbonate for chocolate makers.
Bole Machinery Inc. (Stow, Oh.) the North American unit of China’s Chunglu Group, itself a subsidiary of Ningbo Shuangma Machinery Industry Co. Ltd., has been in U.S. almost four years, according to its president, Alfred Rak. Rak told Plastics Technology that its main office in Stow was opened in November 2018, created after the company formed its own U.S. subsidiary that spring to handle sales and service directly.
Cornering the Chocolate Mold Market
Today, Micelli claims to be the only company in North America that produces these high-tolerance chocolate molds, which are supplied to 700 chocolate companies, and one of only nine companies globally that make chocolate molds. Key to molding the molds, according to Micelli, is a stable platen design that reduces deflection, eliminating defects while also extending the life of the aluminum tool.
Bole says that Tim Goddeau, co-owner of Micelli, made his company one of the first owners of a Bole EK series machine in the U.S., buying one in 2015. Goddeau was attracted by the cost and the press’s toggle design. Of interest there, the patented, German-engineered toggle linkage design known as the “Center Clamp”. In traditional toggle designs, the toggle pins are placed near the outside edges of the platens, at times resulting in resulting in platen deflection, which “bends” the platen around the mold. Over time, this deflection can lead to parting line wear and ultimately result in a poor quality chocolate mold.
With the Center Clamp, Goddeau says the toggle lock is 100% horizontal and very efficient. Enough so that in some jobs, Micelli has been able to lower the force required while still making accurate parts. The company, which makes “artisan” chocolate molds for smaller chocolatiers, as well as industrial chocolate molds for household names, says part weights range from 1 pound for the smallest chocolate mold to up to 8 pounds for the largest. Wall thicknesses vary from 0.0150 to 0.0160 in., and up to 4 feet long by 1 ft wide, with outputs up to 244 pieces of chocolate at a time. Goddeau notes that flatness is absolutely critical as the the chocolate molds need to hold a tolerance of 0.0010 in over 4 feet. Much of the chocolate machinery in use today is made in Europe and requires high precision. Goddeau says it has customers that are able to make sure the tolerances on every cavity of the molds Micelli make are exact within 0.0002 in.
Micelli has been running that first machine—an 800-ton press—for the past five years, six days a week. Micelli manufactures about 250 chocolate molds each year, most of them designed for 100-200 pieces and the biggest producing 2000 pieces of chocolate. The molds are produced in the company’s five Bole injection molding machines, including a Bole DK two-platen machine, that range from 200 to 1400 tons in clamp force.
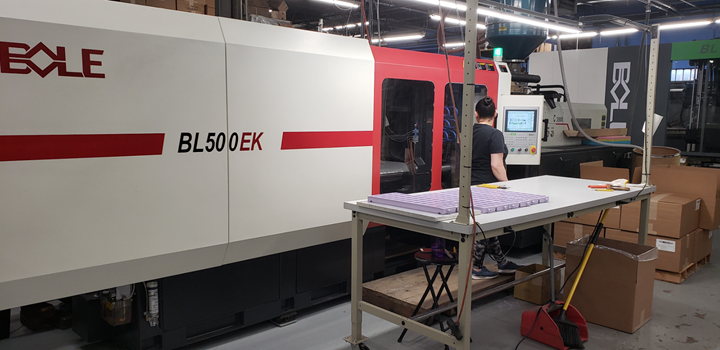
Micelli has five injection molding machines from Bole, ranging in clamp force from 200 to 1400 tons. It was one of the company’s first customers in the U.S.
Establishing a Base
Since winning the business from Micelli, Rak says Bole has become more established in North America. At present, the company has five employees and contracts with two service techs in the states. Stock machines up to 550 tons are maintained in inventory, as our spare parts. Rak says the company has the ability to run mold trials at its facility in Stow. At present, the company has a 1000-ton two-platen machine from its DK line on order, planning to use it to target automotive Tier Two and Three suppliers, with plans for an open house this fall, pandemic permitting.
Related Content
Thermoformer Maximizes Productivity with 3D Printing
Productive Plastics has created an extensive collection of 3D printed manufacturing aids that sharply reduce lead times.
Read MoreInjection Molder Changes Up Color Changes
An injection molder of trash cans, pallets, totes and other plus-size components, Rehrig Pacific’s machine fleet is composed of larger tonnage presses whose size makes material changes at the feed throat a potentially dizzying exercise.
Read MoreMedical Manufacturer Innovates with Additive Manufacturing and Extrusion Technology Hubs
Spectrum Plastics Group offers customers two technology hubs — one for extrusion, the other for additive manufacturing — to help bring ground-breaking products to market faster.
Read MoreOnline X-Ray Inspection Boosts Extrusion Quality
Höhle uses Sikora’s x-ray measuring systems for inline quality control of extruded microducts.
Read MoreRead Next
New North American Office & New Presses for Bole Machinery
Bole America in Stow, Ohio, offers new models of two-platen and servohydraulic toggle presses.
Read MoreNew Toggle Presses from China: All-Electric or Servo-Hydraulic
Bole North America introduces two new lines.
Read More